焼結と溶融は、どちらも材料の結合や成形に使われるプロセスだが、温度、必要なエネルギー、プロセス中の材料の物理的状態という点で根本的に異なる。溶融は、材料を融点まで加熱し、固体状態から液体状態へと変化させる。一方、焼結は熱と圧力を利用して、材料を液化させることなく粒子同士を結合させるため、エネルギー効率が高く、融点の高い材料に適している。焼結は、強度や硬度といった最終製品の特性をよりよく制御できるため、金属やセラミックスから複雑な形状や部品を作る際によく使用される。
主なポイントの説明
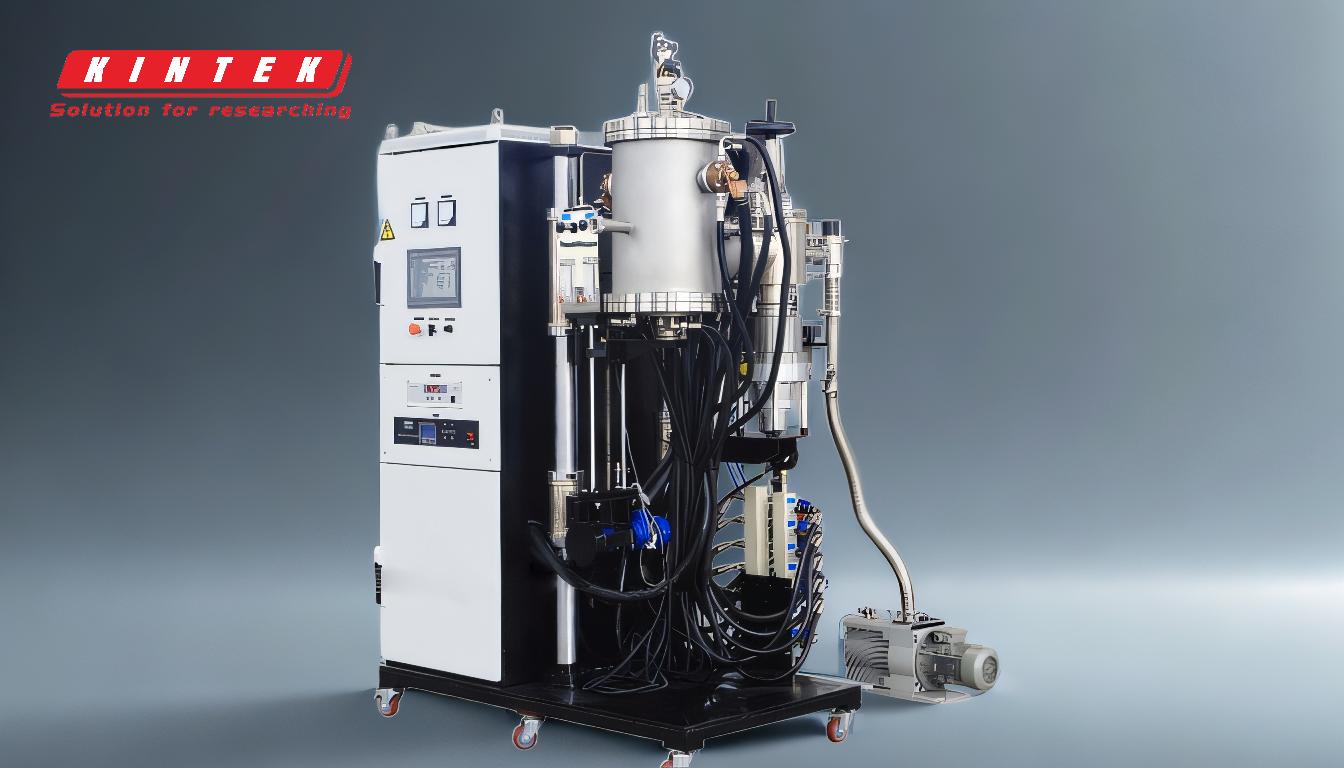
-
温度条件:
- 溶融:材料を融点以上に加熱し、固体から液体への完全な相変化を起こす。このプロセスは高エネルギーを必要とし、融点が極めて高い材料には実用的でないことが多い。
- 焼結:材料の融点以下の温度で作動。熱と圧力を利用して、材料を液化させることなく粒子を結合させるため、エネルギー効率が高く、高融点材料に適している。
-
材料の物理的状態:
- 溶融:材料が液体状態に移行するため、冷却時に気孔、収縮、密度の不均一性などの欠陥が生じる可能性がある。
- 焼結:材料はプロセスを通じて固体の状態を維持するため、最終製品の微細構造と特性をよりよく制御できる。
-
エネルギー効率:
- 溶融:材料の融点に到達し、それを維持する必要があるため、エネルギー消費が大きい。
- 焼結:低温で作動し、材料を液化させる必要がないため、エネルギー効率が高い。
-
最終製品の管理:
- 溶融:液体状態であるため、最終製品の特性をコントロールすることが難しく、不一致が生じる可能性がある。
- 焼結:材料が固体のままであり、工程がより予測しやすいため、強度、硬度、密度などの最終製品の特性をよりコントロールしやすくなる。
-
用途と適性:
- 溶融:鋳造、成形、合金の作成によく使用される。中程度の融点を持つ材料に適している。
- 焼結:金属、セラミック、その他の高融点材料から複雑な形状、部品、コンポーネントを作成するのに理想的。粉末冶金、積層造形、先端材料合成によく使用される。
-
材料特性:
- 溶融:相変化と冷却プロセスにより材料特性が変化し、欠陥が生じる可能性がある。
- 焼結:固体結合と制御された微細構造を維持することにより、強度、硬度、耐摩耗性などの材料特性を向上させる。
-
プロセスの複雑性:
- 溶融:コンセプトは単純だが、特に融点の高い材料や酸化しやすい材料では制御が難しい。
- 焼結:温度、圧力、時間の精密な制御が必要なため、より複雑であるが、高品質の部品を製造する上で、より高い柔軟性と一貫性を提供する。
これらの重要な違いを理解することで、装置や消耗品の購入者は、特定の材料や用途のニーズに最適なプロセスを、十分な情報に基づいて決定することができる。
要約表
側面 | 溶解 | 焼結 |
---|---|---|
温度 | 材料の融点に達する必要がある(高エネルギー)。 | 融点以下で作動する(エネルギー効率が高い)。 |
物理的状態 | 液体状態に移行するため、潜在的な欠陥が発生する可能性がある。 | 固体のままであるため、微細構造の制御が容易である。 |
エネルギー効率 | 相変化によるエネルギー消費が大きい。 | 液化が起こらないため、エネルギー効率が高い。 |
製品のコントロール | 液状であるため制御が難しく、一貫性に欠ける。 | 強度、硬度、密度などの特性をよりコントロールできる。 |
用途 | 鋳造、成形、合金の作成に使用。 | 複雑な形状、粉末冶金、積層造形に最適。 |
材料特性 | 相変化や冷却欠陥により特性が変化することがある。 | 強度や耐摩耗性などの特性を向上させる。 |
プロセスの複雑さ | シンプルだが、高融点材料の制御が難しい。 | より複雑だが、一貫性と高品質の結果が得られる。 |
お客様の素材に適したプロセスの選択にお困りですか? 当社の専門家に今すぐご連絡ください にお問い合わせください!