物理蒸着(PVD)と原子層蒸着(ALD)は、さまざまな産業で使用されている2つの異なる薄膜蒸着技術で、それぞれ独自のプロセス、利点、用途があります。PVDは、蒸発やスパッタリングなどの物理的プロセスに頼って材料を蒸着させますが、多くの場合、低温で高い蒸着速度が得られるため、より単純な形状や合金の蒸着に適しています。対照的に、ALDは化学プロセスであり、逐次的で自己限定的な反応を用いて、複雑な形状や高精度の用途に理想的な、正確な膜厚制御が可能な超薄膜、コンフォーマル膜を成膜する。PVDが "line-of-sight "プロセスであるのに対し、ALDは等方性コーティングを提供し、すべての表面で均一な被覆を保証します。
キーポイントの説明
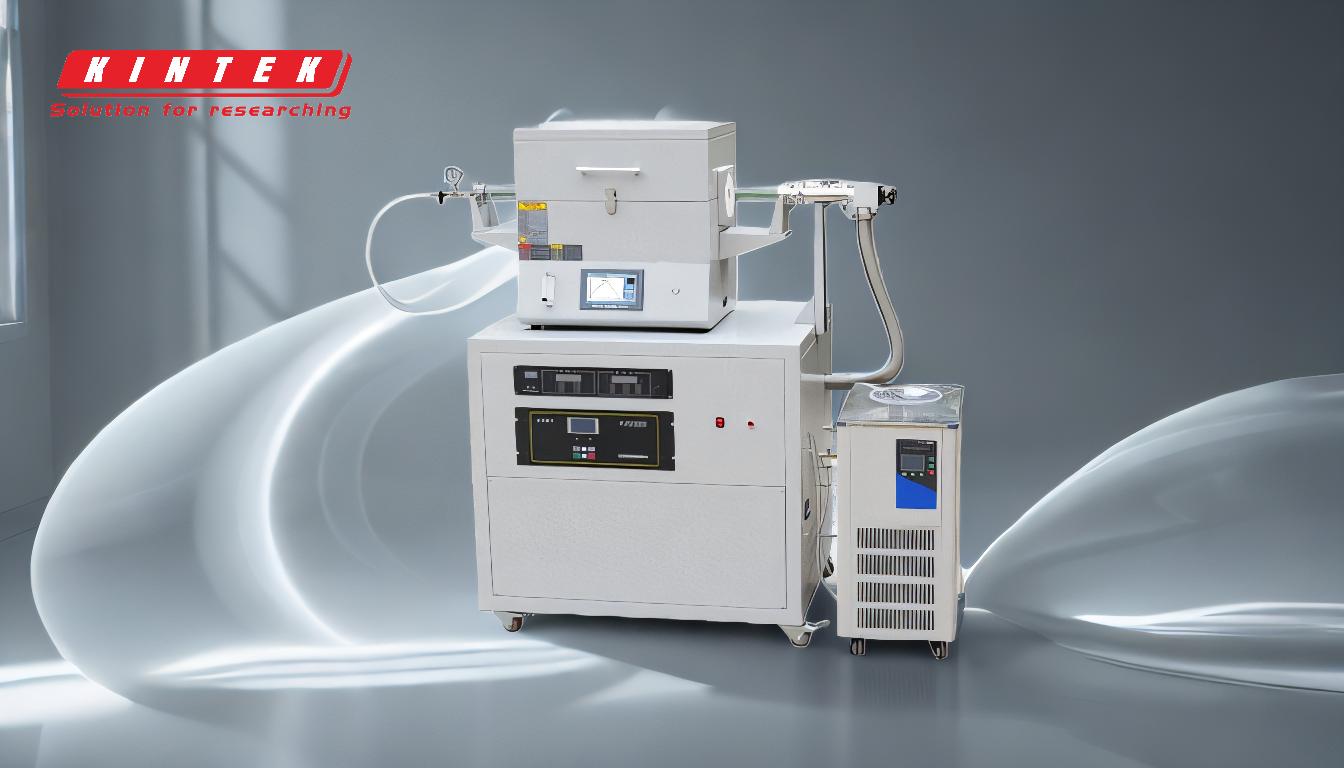
-
プロセス・メカニズム:
- PVD:蒸発やスパッタリングなどの物理的プロセスで、固体材料を気化させ、基板上に凝縮させる。このプロセスは化学反応に頼らず、真空条件下で行われる。
- ALD:基板上に化学結合単分子膜を形成するために、前駆物質と反応物質の連続パルスを使用する化学プロセス。各ステップは自己制限的で、膜厚を正確に制御できる。
-
温度要件:
- PVD:比較的低温で実施できるため、温度に敏感な基板に適している。これは、特に熱応力が低いことが要求される用途に有利である。
- ALD:通常、膜成長に必要な化学反応を促進するために、より高い温度を必要とする。しかし、ALDは場合によっては低温プロセスにも適応できる。
-
堆積率:
- PVD:成膜速度は0.1~100μm/minと高速で、成膜方法(EBPVDなど)により異なる。このため、高速コーティングが必要な用途に適している。
- ALD:レイヤー・バイ・レイヤー成長メカニズムにより、成膜速度が大幅に低下。各サイクルは1原子層のみを成膜するため、全体的な成膜速度は遅くなるが、精度は非常に高い。
-
コーティングの均一性と均一性:
- PVD:ライン・オブ・サイト」プロセス。つまり、光源に直接照射される面だけがコーティングされる。このため、複雑な形状や複雑な形状を持つ基板には効果が限定される。
- ALD:等方性コーティングを提供し、複雑な形状を含むすべての表面で均一な被覆を保証します。このため、ALDは高い適合性が要求される用途に最適です。
-
材料の利用と効率:
- PVD:特にEBPVDのような方法では、高い原料利用効率。このプロセスは原材料の使用量において効率的であり、大規模生産において費用対効果が高い。
- ALD:ALDは高精度である一方、プロセスのシーケンシャルな性質と正確な前駆体の供給が必要なため、材料の使用量という点では効率が低くなる可能性がある。
-
アプリケーション:
- PVD:装飾コーティング、工具用ハードコーティング、合金蒸着など、高い蒸着速度を必要とする用途によく使用される。また、より単純な基板形状にも適している。
- ALD:半導体製造、MEMSデバイス、先端光学など、精密な膜厚制御が可能な超薄膜コンフォーマルフィルムを必要とする用途に最適。
-
安全性と取り扱い:
- PVD:有毒な化学薬品に頼らず、高い基板温度も必要としないため、一般的に安全で取り扱いが容易。腐食性の副産物が発生しにくい。
- ALD:ALDも安全ではあるが、反応性前駆体を扱うため、化学反応や副生成物を管理するために、より厳格な安全プロトコルが必要になる場合がある。
-
コストとスケーラビリティ:
- PVD:成膜速度が速く、プロセス要件が単純なため、大規模生産ではコスト効率が高いことが多い。工業用途にも拡張可能。
- ALD:より高価で速度も遅いため、大量生産には向かない。しかし、その精度と適合性は、高価値で特殊な用途での使用を正当化する。
これらの重要な違いを理解することで、装置や消耗品の購入者は、速度、精度、費用対効果のいずれを優先するかにかかわらず、特定のニーズに最も適した蒸着技術について、十分な情報に基づいた決定を下すことができる。
総括表:
アスペクト | PVD | ALD |
---|---|---|
プロセス・メカニズム | 蒸発やスパッタリングなどの物理的プロセス | 連続的な自己限定反応を伴う化学プロセス |
温度 | 低温、高感度基板に最適 | 温度は高めだが、低温プロセスにも適応可能 |
蒸着率 | ハイ(0.1~100μm/分) | 低い(レイヤーごとの成長) |
コーティングの均一性 | 視線方向、複雑な形状には制限あり | 等方性であらゆる表面を均一にカバー |
材料効率 | 高い材料利用率 | 逐次処理のため効率が悪い |
アプリケーション | 装飾コーティング, ハードコーティング, 合金蒸着 | 半導体製造、MEMSデバイス、先端光学 |
安全性 | より安全で、有害な化学物質が少ない | 反応性前駆体の取り扱いが必要 |
コストとスケーラビリティ | 大量生産に適したコスト効率 | 高価、高価値の特殊用途に適する |
適切な薄膜形成技術の選択にお困りですか? 専門家にご相談ください 個別指導のために!