熱間プレスと圧縮成形は、特に複合材料、セラミック、ポリマーの製造において、材料を成形するために使用される2つの異なる製造プロセスである。どちらも熱と圧力を加えるが、そのメカニズム、用途、結果は大きく異なる。ホットプレスは加圧と焼結を同時に行うため、相変化や合金形成が促進され、活性化焼結プロセスとなる。一方、圧縮成形は、あらかじめ計量した材料を金型キャビティに入れ、熱と圧力を加えて材料を成形する。トランスファー成形は、圧縮成形の一種で、プランジャーとシリンダーシステムを使って、金型キャビティに穴を開けて材料を導入します。
主なポイントを説明します:
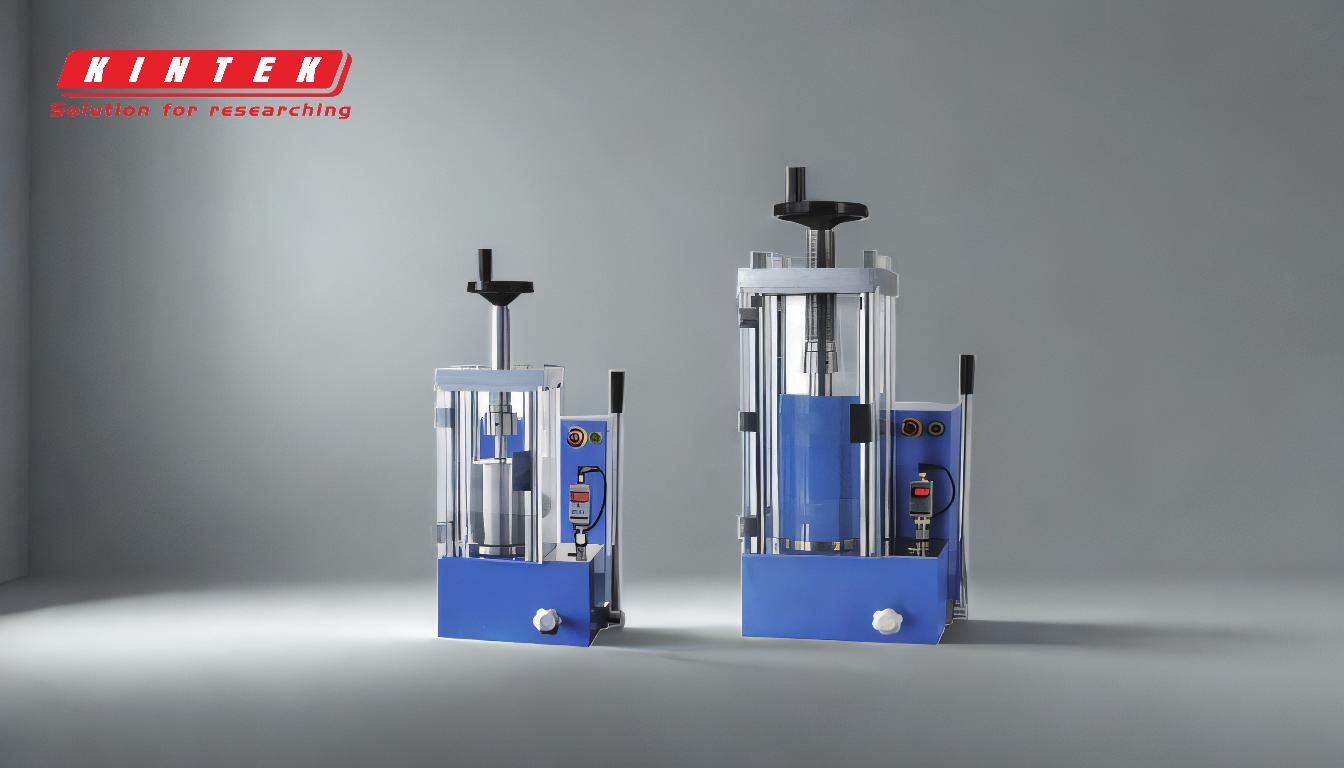
-
動作のメカニズム:
- ホットプレス:ホットプレスは、プレスと焼結のプロセスを統合したものである。材料は同時に高温と高圧にさらされるため、急速な高密度化と結合が促進される。この方法は、セラミックスや高度な複合材料など、高密度の構造を必要とする材料に特に有効である。
- 圧縮成形:圧縮成形では、あらかじめ計量された材料が、加熱された金型のキャビティに直接入れられる。その後、金型を閉じ、圧力を加えて材料を成形する。この工程は、熱硬化性プラスチックやゴムコンパウンドによく使われる。
-
材料の流れと充填:
- ホットプレス:熱間プレスの材料は通常、粉末状または顆粒状で、熱と圧力の下で圧縮・焼結される。この工程により、均一な密度と最小限の気孔率が保証されます。
- 圧縮成形:圧縮成形では、材料は通常、シートやビレットなど、あらかじめ成形された状態にある。材料は流動し、圧力下で金型キャビティに充填されますが、熱間プレスに比べ、流動はあまり制御されません。
-
用途:
- ホットプレス:この方法は、セラミック部品、金属マトリックス複合材料、先端合金などの高性能材料の製造に広く使用されている。特に高い強度と密度が要求される材料に有効です。
- 圧縮成形:圧縮成形は、自動車部品、電気絶縁体、消費財などの大型で複雑な部品の製造によく使われる。また、シールやガスケットなどのゴム製品の製造にも使用される。
-
利点と限界:
-
ホットプレス:
- 利点:高密度製品、加工時間の短縮、材料特性の向上。
- 制限事項:設備コストが高く、高温・高圧に耐えられる材料に限定される。
-
圧縮成形:
- 利点:大型で複雑な部品に適しており、大量生産に適した費用対効果に優れている。
- 制限事項:熱間プレスに比べ、サイクルタイムが長く、材料が無駄になる可能性がある。
-
ホットプレス:
-
トランスファー成形:
- メカニズム:トランスファー成形は、圧縮成形の特殊な形態で、プランジャーとシリンダーシステムを使用して、金型キャビティに穴を通して材料を移送します。この方法は、材料の配置をより正確に制御することができ、複雑なデザインに特に有効です。
- 用途:トランスファー成形は、電子部品の封入、複雑なゴム部品の製造、複雑な形状の部品の製造などによく使われる。
まとめると、熱間プレス成形と圧縮成形はどちらも材料加工に不可欠な技術であるが、その目的は異なり、適合する材料や用途も異なる。熱間プレス成形は高密度で高性能な材料に理想的ですが、圧縮成形は大型で複雑な部品により汎用性があり、費用対効果に優れています。トランスファー成形は、複雑な設計にさらなる精度を提供し、圧縮成形の貴重なバリエーションとなっています。
総括表
側面 | ホットプレス | 圧縮成形 |
---|---|---|
メカニズム | 高熱と高圧下でプレスと焼結を同時に行う。 | 加熱した金型のキャビティに材料を入れ、圧力をかけて成形する。 |
材料の形状 | 粉末状または粒状、圧縮、焼結。 | 予備成形状態(シートまたはビレット)、加圧下で流動。 |
用途 | セラミックス、金属基複合材料、合金などの高性能材料。 | 自動車部品、ゴム製シール、ガスケットなどの大型で複雑な部品。 |
利点 | 高密度製品、加工時間の短縮、材料特性の向上。 | 大量生産のための費用対効果、多様な材料適合性。 |
制限事項 | 設備コストが高い、高温・高圧材料に限定される。 | サイクルタイムが長く、材料が無駄になる可能性があり、材料の流れをコントロールしにくい。 |
お客様の材料に適した製造プロセスの選択にお困りですか? 当社の専門家に今すぐご連絡ください にお問い合わせください!