化学気相成長法(CVD)と物理気相成長法(PVD)は、さまざまな産業で使用されている2つの異なる薄膜形成技術である。CVDは、気体状の前駆物質を用いて化学反応を起こし、通常は高温で基板上に固体膜を形成する。これに対してPVDは、固体のターゲット材料を物理的に気化させ、低温で基板上に凝縮させる。CVDでは純度の高い膜が得られることが多いが、腐食性の副生成物が発生することがある。どちらの方法にも独自の利点があり、温度感受性、材料適合性、希望する膜特性など、アプリケーション固有の要件に基づいて選択されます。
キーポイントの説明
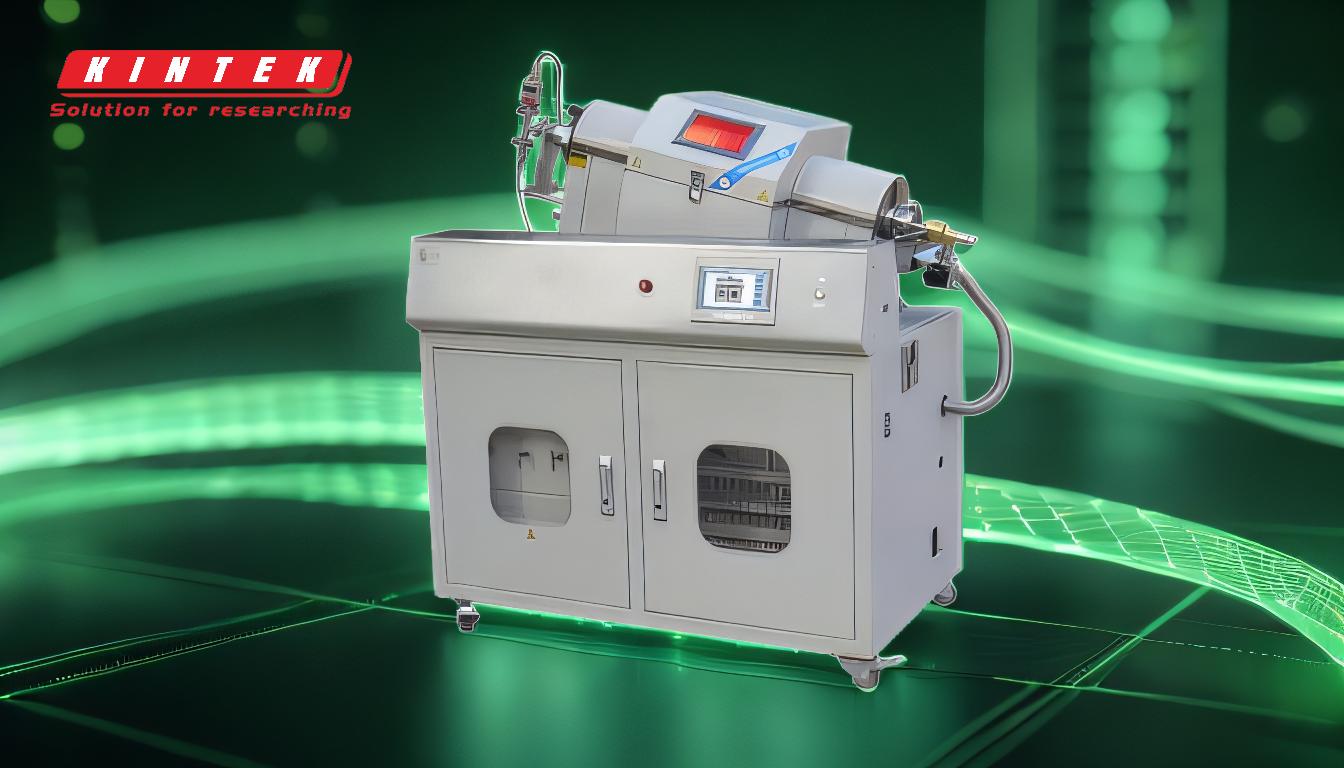
-
プリカーサータイプ:
- CVD:ガス状の前駆体を使用し、基板表面で化学反応または分解して固体膜を形成する。この化学変化がCVDの特徴である。
- PVD:蒸発、スパッタリング、昇華などの物理的プロセスによって気化した固体前駆体(ターゲット)を利用する。気化した材料は基板上に凝縮する。
-
温度条件:
- CVD:通常、高温(500℃~1100℃)で使用されるため、温度に敏感な基材への使用が制限されることがある。高温は化学反応を促進するために必要である。
- PVD:低温で実施できるため、高熱に耐えられない基材に適している。これは、プラスチックやその他の熱に弱い材料を含むアプリケーションに特に有利である。
-
蒸着メカニズム:
- CVD:ガス状の前駆体同士、または前駆体と基材との化学反応を伴う。その結果、化学的に結合した膜ができる。
- PVD:蒸発やスパッタリングなどの物理的プロセスに依存し、原子や分子が固体ターゲットから放出され、化学反応を伴わずに基板上に堆積する。
-
副生成物と不純物:
- CVD:化学反応中に腐食性のガス状副生成物が発生する可能性があり、その場合、追加的な取り扱いや廃棄措置が必要になることがある。また、フィルムに不純物が混入することもある。
- PVD:一般的に、化学反応を伴わない物理的プロセスを伴うため、副生成物が少なく、よりクリーンな膜が得られる。
-
成膜速度と効率:
- CVD:成膜速度は中~高速だが、化学反応が必要なためプロセスが遅くなることがある。
- PVD:電子ビーム物理蒸着法(EBPVD)のような特殊な技術では、優れた材料利用効率で高い蒸着速度(0.1~100μm/分)を達成できるが、一般的にCVDに比べて蒸着速度は低い。
-
フィルム特性:
- CVD:高純度で優れた適合性を持つ皮膜が得られるため、複雑な形状に均一な皮膜を必要とする用途に最適。
- PVD:良好な密着性と密度を持つ膜が得られるが、CVDに比べ適合性が劣る場合がある。膜厚や組成の精密な制御が必要な用途では、PVDが好まれることが多い。
-
用途:
- CVD:高品質で均一な膜を成膜できるため、半導体製造、光学コーティング、保護コーティングによく使用される。
- PVD:装飾用コーティング、耐摩耗性コーティング、薄膜太陽電池の製造に広く採用されており、低温でクリーンなプロセスが有利である。
これらの重要な違いを理解することで、装置や消耗品の購入者は、基材の材質、希望する膜特性、プロセス要件などの要因を考慮しながら、特定のニーズに最も適した成膜方法を、十分な情報に基づいて決定することができる。
要約表
側面 | CVD | PVD |
---|---|---|
前駆体タイプ | 化学反応または分解するガス状前駆体。 | 物理的過程で気化した固体前駆体。 |
温度 | 高温(500℃~1100℃)。 | 低温、熱に弱い基板に適している。 |
蒸着メカニズム | 化学反応は固体膜を形成する。 | 蒸発やスパッタリングなどの物理的プロセスによって膜が堆積する。 |
副産物 | 腐食性のガス状副生成物が発生する可能性がある。 | 副生成物が少なく、クリーンなプロセス。 |
蒸着速度 | 化学反応により遅い。 | 低レートだが、EBPVDのような技術は高レートを達成できる。 |
フィルム特性 | 高純度、優れたコンフォーマリティ | 密着性と密度が高く、適合性が低い。 |
用途 | 半導体、光学コーティング、保護コーティング | 装飾コーティング、耐摩耗コーティング、薄膜太陽電池。 |
お客様の用途に適した成膜方法の選択にお困りですか? 当社の専門家に今すぐお問い合わせください !