化学気相成長法(CVD)は、酸化やその他の成膜技術に比べ、特に精度、汎用性、材料特性の面で大きな利点がある。CVDは、高純度で均一な薄膜やナノ粒子を作成することができ、厚さや表面の平滑性を高度に制御することができる。CVDは拡張性に優れ、視線を通さないため複雑な形状のコーティングも可能である。さらにCVDでは、温度、圧力、ガスフローなどのパラメーターを調整することで、化学的・物理的特性を調整した材料を合成することができる。酸化と比較して、CVDはより優れた電気伝導性と熱伝導性を提供し、混合適合性を改善し、環境フットプリントを削減することで、先端材料アプリケーションのための優れた選択肢となっている。
キーポイントの説明
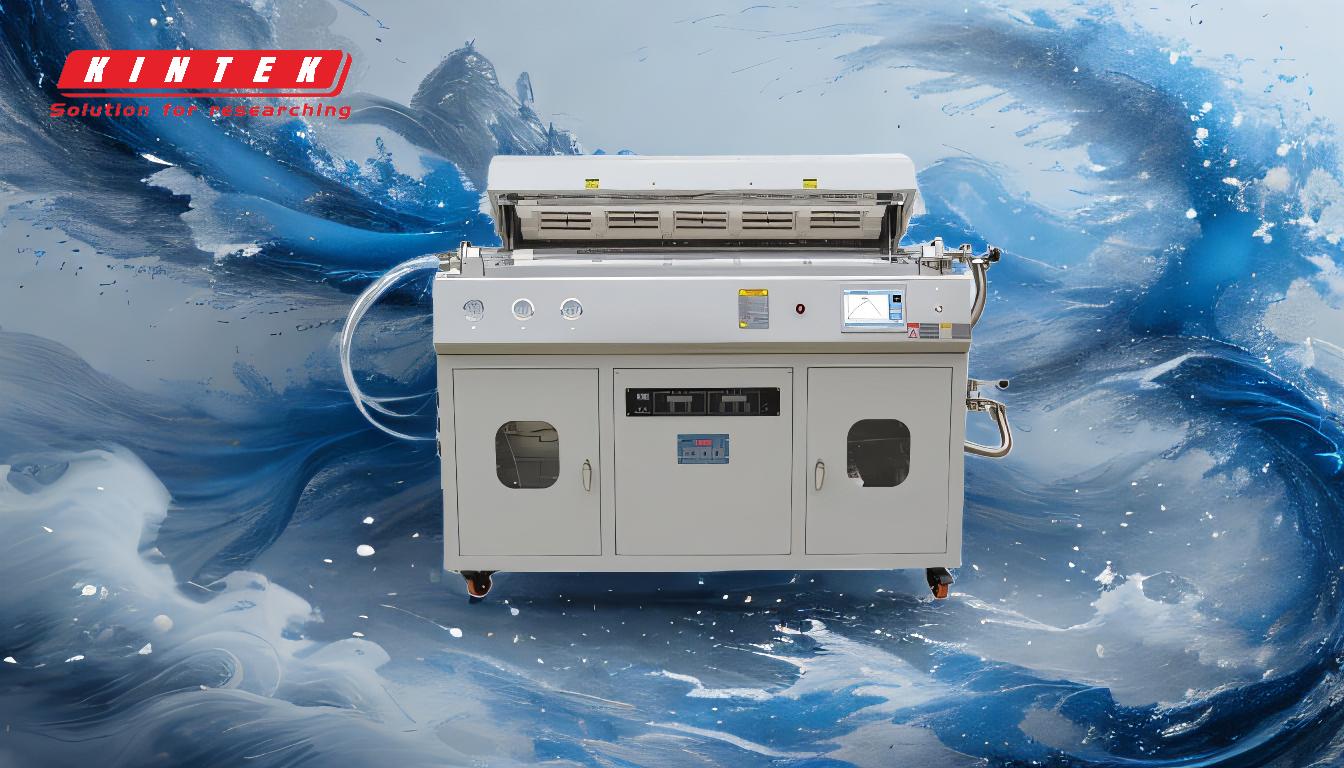
-
精度とコントロール:
- CVDは、膜厚、表面平滑性、材料純度を比類なく制御できる。この精度は、温度、圧力、ガス流量、ガス濃度などのパラメーターを調整することで達成される。
- 酸素との表面反応に頼る酸化とは異なり、CVDは化学反応を利用して材料を堆積させるため、均一な特性を持つ極薄の層を形成することができる。そのため、電気回路のように精度が重要な用途に最適です。
-
材料合成における多様性:
- CVDは、耐食性、耐摩耗性、高純度などの特性を持つ、セラミック、金属、ガラスを含むさまざまな材料を成膜することができる。
- 単結晶や多結晶の薄膜、アモルファス薄膜など、純粋な材料から複雑な材料まで、酸化プロセスと比較して比較的低温で製造することができる。
-
非直視下蒸着:
- 酸化に対するCVDの最も大きな利点のひとつは、複雑な形状や深い凹み、穴を均一にコーティングできることである。これは、非直視型の性質によるもので、複雑な形状を均一に被覆することができる。
- 一方、酸化は表面反応に限定されるため、同じレベルの被覆や均一性を達成することはできない。
-
スケーラビリティと経済性:
- CVDは拡張性が高いため、小規模な研究にも大規模な工業生産にも適している。成膜速度が速く、厚いコーティングを経済的に製造できる。
- 高温や特殊な環境条件を必要とする酸化とは異なり、CVDは通常、超高真空を必要としないため、運用コストを削減できる。
-
材料特性の向上:
- CVDは、酸化と比較して、優れた電気伝導性と熱伝導性、滑らかな表面、他の材料との優れた混合適合性を持つ材料を生成します。
- また、このプロセスは、高ストレス環境や極端な温度変化にも耐える耐久性のあるコーティングをもたらし、要求の厳しい用途に適しています。
-
環境および運用上の利点:
- CVDは、他の成膜技術に比べてCO2排出量を削減できるため、より環境に優しい選択肢となる。
- 耐腐食性や高純度など、特定の特性に合わせてガスを最適化できるため、酸化に比べて運用上の利点がさらに高まります。
-
先端技術への応用:
- CVDは、超薄膜で高純度の層を形成できるため、電気回路、半導体、精密部品の製造に広く使用されている。
- 以下のような技術がある。 マイクロ波プラズマ化学気相成長法 は、プラズマを活用して成膜速度と材料品質を向上させ、先端材料合成における用途をさらに拡大する。
まとめると、CVDは精度、汎用性、拡張性、材料性能において酸化を凌駕しており、最新の材料成膜やコーティング用途に適した選択肢となっている。
総括表
アドバンテージ | CVD | 酸化 |
---|---|---|
精度とコントロール | 厚み、平滑度、純度の高いコントロール。 | 表面反応による精度の限界。 |
材料の多様性 | セラミックス、金属、ガラスをそれぞれの特性に合わせた形で成膜する。 | 酸化物や表面反応に限定される。 |
非直視下蒸着 | 複雑な形状を均一にコーティング。 | 複雑な形状を効果的にコーティングできない。 |
拡張性 | 研究用や産業用に高い拡張性を持つ。 | 拡張性が低く、しばしば高温を必要とする。 |
材料特性 | 優れた電気・熱伝導性と耐久性。 | 導電性が劣り、コーティングの耐久性が劣る。 |
環境への影響 | CO2排出量の削減と運転効率の向上。 | 高温条件による環境負荷の増大。 |
CVDの可能性を最大限に引き出します。 私たちの専門家に今すぐご連絡ください までご連絡ください!