RFスパッタリングにおけるプラズマは部分的に電離した気体であり、特に非導電性または低導電性材料の薄膜成膜において重要な役割を果たす。プラズマは高周波の交流電流によって維持され、プラズマ内の電子を加速・反転させることで運動エネルギーを発生させる。このプロセスでは、ターゲット材料の上方に二次イオンを捕捉する必要がないため、マグネトロンスパッタリングなどの従来の方法と比較して、プラズマを低圧で作動させることができる。電磁場への応答性や高い運動エネルギーといったプラズマのユニークな特性は、原子レベルでの精密かつ純粋な薄膜成膜を実現するために不可欠なものである。
キーポイントの説明
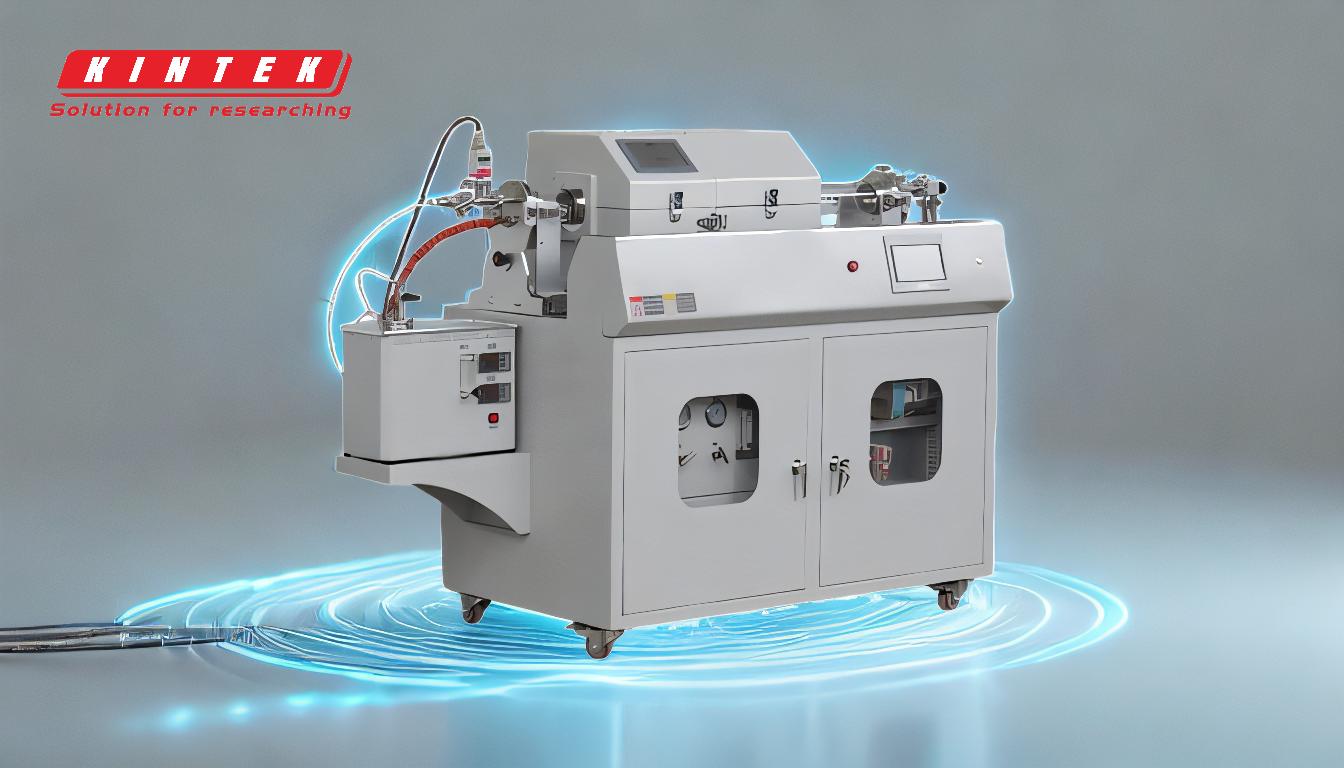
-
RFスパッタリングにおけるプラズマの定義:
- プラズマは部分的に電離した気体で、しばしば物質の第4の状態と呼ばれ、自由電子、イオン、中性の原子または分子から構成される。
- RFスパッタリングでは、一般に高周波(RF)範囲(例えば13.56 MHz)の高周波交流電流を流すことでプラズマを維持する。
- この交流電流によって電子が振動し、運動エネルギーを得て、プラズマ状態の維持に不可欠となる。
-
RFスパッタリングにおけるプラズマの役割:
- プラズマは、スパッタリングとして知られるプロセスで、ターゲット材料から原子を離脱させるのに必要な高い運動エネルギーを提供する。
- プラズマからのエネルギーは通常の熱エネルギーよりもはるかに高く、原子レベルでの精密で純粋な薄膜成膜を可能にする。
- この高エネルギー環境は、低温処理が可能なため、温度に敏感な基板への薄膜成膜に特に有利です。
-
DCプラズマに対するRFプラズマの利点:
- RFスパッタリングは、直流電源では効果的にスパッタリングできない非導電性または低導電性のターゲット材料に特に有効である。
- RFスパッタリングの交流電流は、絶縁材料のDCスパッタリングでよく見られる問題であるターゲット表面への電荷蓄積を防ぐ。
- RFプラズマはDCプラズマに比べてはるかに低い圧力で維持できるため、二次イオントラップの必要性が減り、プロセス効率が向上する。
-
RFプラズマにおける運動エネルギー生成:
- RFスパッタリングの交流電流は、電子を前後に加速し、運動エネルギーを発生させる。
- この運動エネルギーはプラズマ中のガス原子に伝達され、ガス原子をイオン化してプラズマ状態を維持する。
- このプロセスは効率が高く、成膜プロセスを精密に制御できるため、高品質の薄膜を必要とする用途に最適である。
-
従来のマグネトロンスパッタリングとの比較:
- 従来のマグネトロンスパッタリングでは、二次イオンをターゲット材料の上方にトラップすることでプラズマを維持するため、より高い圧力が必要となる。
- 一方、RFスパッタリングは、このトラッピング機構に依存しないため、より低い圧力と高い効率で作動することができる。
- この違いにより、RFスパッタリングはデリケートな基板や温度に敏感な基板への薄膜成膜に適している。
-
RFスパッタリングプラズマの用途:
- RFスパッタリングは、酸化物や窒化物などの絶縁材料の薄膜を成膜するために、半導体産業で広く使用されている。
- RFスパッタリングはまた、光学コーティングや太陽電池など、膜特性の精密な制御が不可欠な先端材料の製造にも用いられている。
- 低温で薄膜を成膜できることから、RFスパッタリングは、温度に敏感な材料を使用する用途に適した方法となっている。
これらの重要な点を理解することで、RFスパッタリングにおいてプラズマが果たす重要な役割と、他のスパッタリング法に対する優位性を理解することができる。この知識は、特定の用途に適したスパッタリング技術を選択することの重要性を浮き彫りにするため、装置や消耗品の購入者にとって特に貴重である。
総括表:
アスペクト | 詳細 |
---|---|
定義 | 高周波交流で維持される部分電離ガス。 |
役割 | ターゲット材料から原子をスパッタリングするための高い運動エネルギーを提供する。 |
DCプラズマを超える利点 | 非導電性材料で動作し、電荷の蓄積を防止し、圧力が低い。 |
運動エネルギー生成 | 交流電流で電子を加速し、ガス原子を効率よくイオン化。 |
マグネトロンとの比較 | デリケートな基板や温度に敏感な基板に理想的な、より低い圧力で動作します。 |
用途 | 半導体産業、光学コーティング、太陽電池、先端材料。 |
RFスパッタリングで薄膜成膜プロセスを最適化しましょう。 今すぐ専門家にお問い合わせください !