半導体製造における蒸着工程は、デバイスの機能に不可欠な高品質で高性能な固体材料や薄膜を作成するために使用される重要なステップです。化学的気相成長法(CVD)、プラズマエンハンスドCVD(PECVD)、物理的気相成長法(PVD)などのさまざまな手法を用いて、アルミニウムなどの二次層を基板上に堆積させます。このプロセスは通常真空チャンバー内で行われ、ランプアップ、エッチング、コーティング、ランプダウンなどのステップが含まれる。低圧CVD(LPCVD)、原子層蒸着(ALD)などの蒸着技術が採用され、半導体デバイスの性能と信頼性に不可欠な精密な材料積層が行われる。
キーポイントの説明
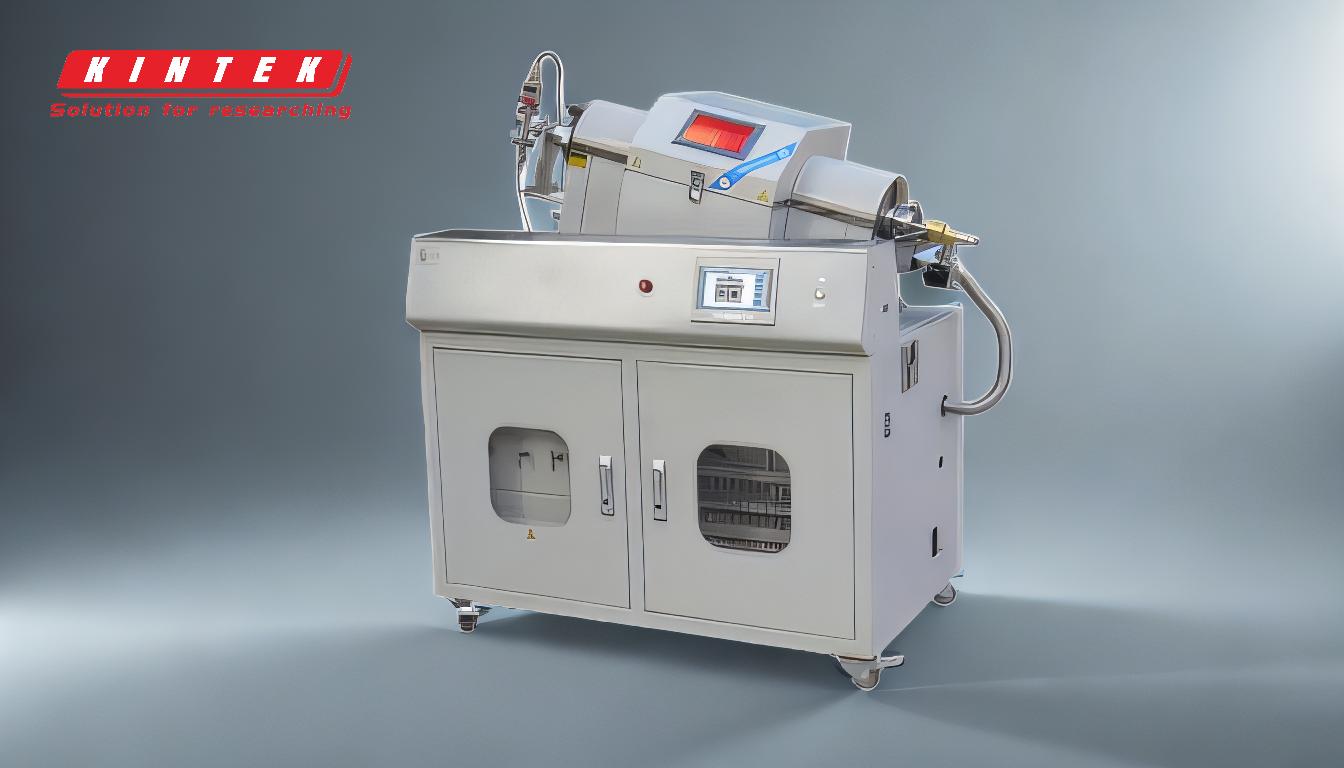
-
半導体製造における成膜の目的:
- 成膜プロセスは、半導体デバイスの機能層を形成する薄膜や固体材料を作成するために使用される。
- これらの層は、デバイスの電気的、熱的、機械的特性にとって重要であり、高性能と信頼性を保証します。
-
蒸着に使用される材料:
- 一次材料:アルミニウムは、その優れた導電性と半導体プロセスとの適合性により、基板の主層に一般的に使用される。
- 副材料:タングステン、二酸化ケイ素、窒化物などの他の材料は、絶縁性、導電性、保護性の部品を形成するために二次層として蒸着される。
-
蒸着技術:
-
化学気相成長法 (CVD):ガス状反応体を用いて固体材料を基材上に析出させるプロセス。例えば、以下のようなものがある:
- HDP-CVD (高密度プラズマCVD):高品質で緻密な膜を形成する。
- プラズマエンハンストCVD (PECVD):低温で化学反応を促進するためにプラズマを利用する。
- CVDタングステン:特にタングステン層の蒸着に使用される。
- 物理蒸着(PVD):スパッタリングや蒸着などの物理的な方法で材料を堆積させる。
- 原子層蒸着(ALD):超薄膜を1層ずつ蒸着する精密な技術。
-
化学気相成長法 (CVD):ガス状反応体を用いて固体材料を基材上に析出させるプロセス。例えば、以下のようなものがある:
-
成膜プロセスのステップ:
- ランプアップ:真空チャンバーは、蒸着に理想的な条件を作り出すために、徐々に温度を上げ、圧力を下げることによって準備される。
- エッチング:汚染物質を除去し、蒸着材料の密着性を向上させるため、プラズマエッチングで基板を洗浄する。
- コーティング:蒸着する材料を基板上に投影し、薄膜を形成する。
- ランプダウン:チャンバーは冷却システムを用いて室温と常圧に戻される。
-
一般的な蒸着技術:
- 低圧CVD (LPCVD):減圧で動作し、均一な成膜が可能。
- 亜大気圧CVD (SACVD):大気圧以下の条件を必要とする特定の用途に使用される。
- 大気圧CVD (APCVD):大気圧で動作し、特定の材料の成膜を行う。
- 超高真空CVD (UHV-CVD):先端用途の高純度膜に用いられる。
- エピタキシャル成長(Epi):基板上に単結晶層を成長させ、高性能デバイスを実現。
-
半導体製造との統合:
- 蒸着プロセスは、フォトリソグラフィー、エッチング、ドーピングなどの他の製造工程と統合され、複雑な半導体構造を作り出す。
- 例えば、蒸着後、フォトレジストによるパターニングとエッチングを行い、蒸着層上に特定の特徴を定義する。
-
用途と重要性:
- 蒸着は、半導体デバイスの相互接続、ゲート酸化物、絶縁層を形成するために不可欠である。
- マイクロプロセッサー、メモリーチップ、センサーなどの先端技術に必要な材料の正確な積層を保証します。
成膜プロセスとその様々な技術を理解することで、半導体メーカーは要求される電気的・機械的特性を備えたデバイスを製造することができ、現代のエレクトロニクスにおける高い性能と信頼性を確保することができる。
総括表
アスペクト | 詳細 |
---|---|
目的 | 半導体デバイスの機能を実現する薄膜や固体材料を創製する。 |
主要材料 | 導電性と互換性のためのアルミニウム。 |
副材料 | タングステン、二酸化ケイ素、絶縁と保護のための窒化物。 |
技術 | CVD、PECVD、PVD、ALD、LPCVD、SACVD、APCVD、UHV-CVD、エピタキシャル成長。 |
プロセスステップ | ランプアップ、エッチング、コーティング、ランプダウン |
用途 | インターコネクト、ゲート酸化膜、マイクロプロセッサーやセンサーの絶縁層。 |
先進の成膜技術で半導体製造を強化する方法をご覧ください。 私たちの専門家に今すぐご連絡ください !