スパッタプロセスは、基板上に材料の薄膜を堆積させるために広く使用されている物理的気相成長(PVD)技術である。真空を作り、不活性ガスを導入し、ガスをイオン化してプラズマを形成し、プラズマを使ってターゲット材料から原子を放出させ、基板上に堆積させる。このプロセスは高度に制御されており、高純度で均一なコーティングの成膜を保証する。以下では、スパッタリング・プロセスのステップを詳しく説明する。
要点の説明
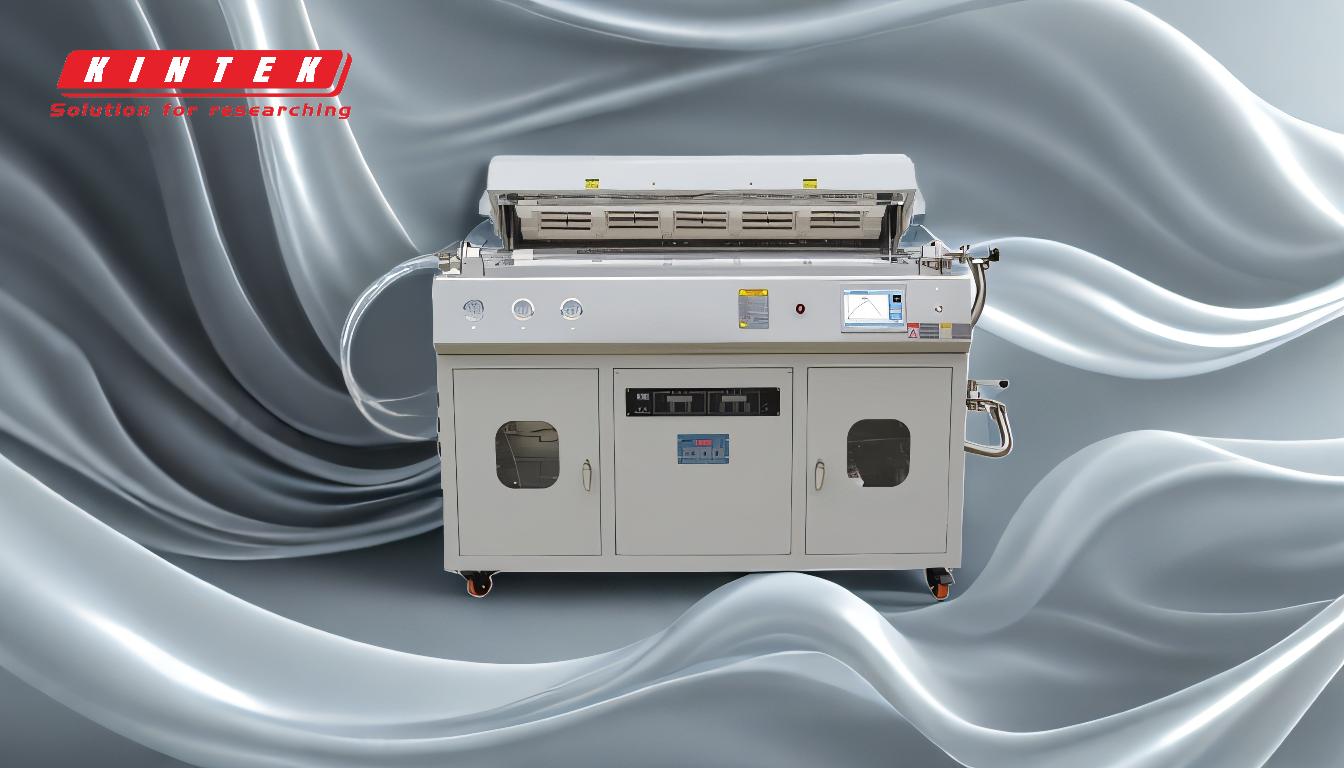
-
反応チャンバー内を真空にする
- 最初のステップでは、水分、不純物、残留ガスを除去するために反応チャンバーを真空にする。
- 通常、圧力は約1Pa(0.0000145psi)まで下げられ、プロセスのためのクリーンな環境が作られる。
- 真空にすることで、汚染物質が成膜を妨げないようにすることができ、これは高品質のコーティングを実現するために非常に重要です。
-
不活性ガスの導入
- 真空が確立したら、不活性ガス(通常はアルゴン)をチャンバーに導入する。
- 不活性ガスは化学的に不活性であるため、プロセス中の不要な反応を最小限に抑えることができる。
- ガスの圧力は、通常10-¹~10-³ mbarの範囲で、プラズマ形成に理想的な低圧雰囲気になるように調整される。
-
チャンバーの加熱
- チャンバーは、成膜する材料によって150℃から750℃(302°Fから1382°F)の範囲で加熱される。
- 加熱は、基材へのコーティングの適切な付着を確実にし、また、蒸着膜の微細構造や特性に影響を与えることがある。
-
プラズマの発生
- 高電圧(3~5kV)をかけてアルゴンガスをイオン化し、プラズマを発生させる。
- プラズマは、正電荷を帯びたアルゴンイオン(Ar⁺)と自由電子からなる。
- 磁場はプラズマを閉じ込め、制御するためにしばしば使用され、イオン化プロセスの効率を高めます。
-
ターゲットに向かってイオンを加速する
- プラスに帯電したAr⁺イオンは、ターゲット材(コーティング材の元)に向かって加速されます。
- ターゲットはマイナスに帯電しており、イオンを引き寄せる電界が発生します。
- イオンがターゲットに衝突するとエネルギーが移動し、原子がターゲット表面から放出される。
-
スパッタされた原子の基板への輸送
- 放出された原子は、低圧環境を通って基板に向かって輸送される。
- 圧力が低いため、原子間の衝突が最小限に抑えられ、材料の流れが確実になる。
- このステップは、基板全体で均一な成膜を達成するために重要である。
-
薄膜の成膜
- スパッタされた原子は基板表面に凝縮し、薄膜を形成する。
- 蒸着された原子のエネルギーは表面の移動度を高め、密着性と膜質の向上につながる。
- このプロセスは、所望の膜厚になるまで続けられる。
-
プロセスパラメーターの制御
- プロセス全体を通して、圧力、温度、電圧、磁場強度などのパラメーターは慎重に制御される。
- これらのパラメータは、成膜速度、膜質、最終コーティングの特性に影響を与える。
- 特定の材料や用途に合わせてプロセスを最適化するための調整も可能である。
スパッタプロセスは、基板上に材料の薄膜を成膜するための精密で汎用性の高い方法である。真空の形成から成膜までの各工程を注意深く制御することで、メーカーは優れた密着性と純度を備えた高品質で均一な膜を得ることができる。このため、スパッタリングは、電子機器、光学機器、航空宇宙産業など、精度と性能が重視される産業で好まれる技術となっている。
総括表
ステップ | 主な内容 |
---|---|
1.真空を作る | チャンバーを~1Paまで排気し、汚染物質を除去する。 |
2.不活性ガスの導入 | プラズマ形成のためにアルゴンガスを10-¹~10-³ mbarで加える。 |
3.チャンバーの加熱 | 150℃~750℃に加熱し、接着性とフィルム特性を高める。 |
4.プラズマの発生 | 3~5kVを印加してアルゴンをイオン化し、プラズマを発生させる。 |
5.加速するイオン | プラスに帯電したAr⁺イオンがマイナスに帯電したターゲットに衝突する。 |
6.原子の輸送 | スパッタされた原子は低圧環境で基板に流れる。 |
7.薄膜の蒸着 | 基板上に原子が凝縮し、均一で高品質な被膜が形成される。 |
8.パラメーターの制御 | 圧力、温度、電圧、磁場を調整し、最適な結果を得ることができます。 |
高品質の薄膜蒸着ソリューションが必要ですか? 当社の専門家に今すぐご連絡ください までご連絡ください!