薄膜蒸着は材料科学と工学において重要なプロセスであり、基板上に材料の薄い層を作ることを可能にする。薄膜形成のための物理的方法は、その精度、汎用性、高品質な膜を作る能力により、広く使用されています。これらの方法は主に物理蒸着(PVD)のカテゴリーに属し、蒸着やスパッタリングなどの技術が含まれる。各手法には独自の特性、利点、用途があり、さまざまな産業や研究のニーズに適しています。
キーポイントの説明
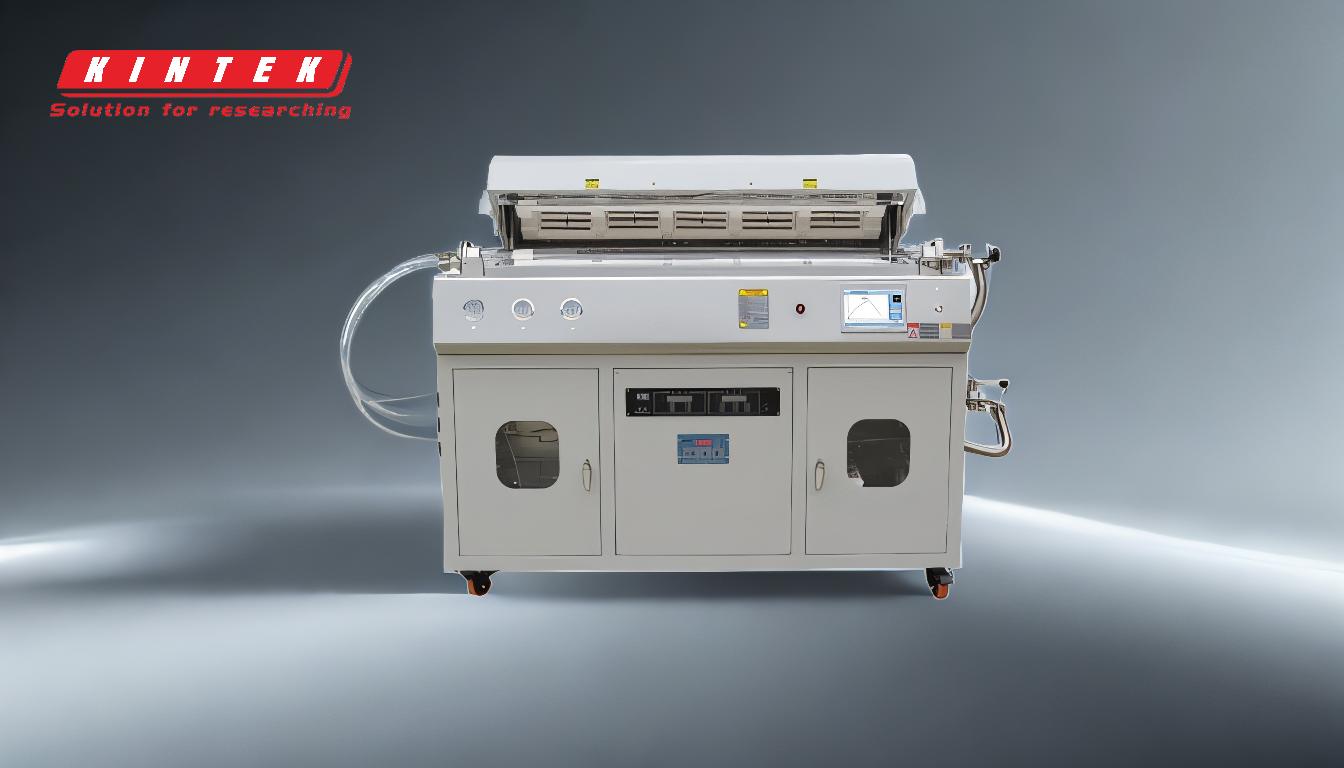
-
物理的気相成長法(PVD)の概要
- PVDは、ソースから基板への材料の物理的移動を伴う薄膜蒸着技術の一群である。
- このプロセスは通常、汚染を最小限に抑え、高純度の成膜を保証するために真空環境で行われる。
- PVD法は、均一で緻密な密着性の高い膜を作ることができるため、半導体、光学、コーティングなどの産業で広く使用されている。
-
蒸着技術
-
熱蒸発:
- ターゲット材料が蒸発するまで加熱し、基板上に凝縮する蒸気を形成する。
- 金属や単純化合物の蒸着によく用いられる。
- 利点簡単なセットアップ、高い蒸着率、低コスト。
- 制限事項融点の低い材料に限られ、ステップカバレッジが悪くなる可能性がある。
-
電子ビーム蒸着:
- 集束電子ビームを使用してターゲット材料を加熱・蒸発させる。
- 高融点材料に適しており、蒸着パラメーターの制御が容易。
- 用途光学コーティング、半導体デバイス、耐摩耗性コーティング。
-
分子線エピタキシー(MBE):
- 単結晶薄膜の成長に用いられる高度に制御された蒸着法。
- 超高真空条件下で作動し、正確なレイヤーバイレイヤー成長を可能にする。
- 用途先端半導体デバイス、量子ドット、ナノ構造。
-
熱蒸発:
-
スパッタリング技術
-
マグネトロンスパッタリング:
- 磁場を利用してスパッタリングプロセスを強化し、成膜速度と効率を高めます。
- 金属、合金、セラミックスなど幅広い材料に適しています。
- 利点優れた均一性、良好な接着性、複雑な形状への適合性。
- 用途薄膜トランジスタ、太陽電池、装飾用コーティング。
-
イオンビームスパッタリング:
- イオンビームを使用してターゲット材料から原子を離脱させ、基板上に堆積させる。
- 膜特性を精密に制御でき、高品質の光学コーティングに最適。
- 用途レーザー光学、反射防止コーティング、精密ミラー。
-
パルスレーザー堆積法(PLD):
- 高エネルギーレーザーパルスを使用してターゲットから材料をアブレーションし、プルームを形成して基板上に堆積させる。
- 酸化物や超伝導体などの複雑な材料を高い化学量論精度で蒸着できる。
- 用途高温超伝導体、強誘電体膜、多成分酸化物。
-
マグネトロンスパッタリング:
-
その他の物理蒸着法
-
カーボンコーティング:
- スパッタリングや蒸着法の一種で、電子顕微鏡用の炭素膜の成膜に用いられる。
- サンプルに導電層や保護層を提供する。
-
パルスレーザーアブレーション:
- PLDと似ているが、レーザーパルスを用いた材料の迅速な除去と蒸着に重点を置いている。
- 汚染を最小限に抑えた複雑な材料の蒸着に使用される。
-
カーボンコーティング:
-
物理蒸着法の利点
- 純度が高く、膜組成を制御できる
- 金属、セラミックス、ポリマーなど幅広い材料の成膜が可能。
- 蒸着膜の優れた密着性と均一性。
- 小規模な研究から大規模な工業用途まで適している。
-
物理蒸着法の応用
- エレクトロニクス:半導体デバイスにおける導電層と絶縁層の成膜。
- 光学:反射防止膜、反射膜、保護膜の製造。
- エネルギー:薄膜太陽電池と電池電極の製造。
- メディカル:生体適合性と耐久性を向上させる医療機器のコーティング。
- 航空宇宙:耐摩耗性コーティングと遮熱コーティングの応用。
要約すると、蒸着やスパッタリングなどの薄膜合成や成膜のための物理的手法は、その特性を精密に制御して高品質な膜を作るために不可欠である。これらの技術は汎用性が高く、拡張性に富み、さまざまな産業で広く利用されているため、現代の材料工学には欠かせないものとなっている。
要約表
方法 | 主な特徴 | 用途 |
---|---|---|
熱蒸着 | 簡単なセットアップ、高い蒸着率、低コスト | 金属、単純化合物 |
電子ビーム蒸着 | 高融点材料、精密制御 | 光学コーティング、半導体デバイス |
分子線エピタキシー(MBE) | 超高真空、単結晶成長 | 先端半導体、量子ドット |
マグネトロンスパッタリング | 優れた均一性、優れた密着性、複雑な形状 | 薄膜トランジスタ、太陽電池 |
イオンビームスパッタリング | 精密制御、高品質光学コーティング | レーザー光学、反射防止コーティング |
パルスレーザー堆積法 (PLD) | 高い化学量論精度、複雑な材料 | 高温超伝導体、強誘電体膜 |
物理的蒸着法がお客様の研究や生産をどのように強化できるかをご覧ください。 今すぐご連絡ください までご連絡ください!