プラズマ蒸着は、薄膜製造に使用される多用途の技術であり、プラズマを利用して蒸着プロセスを強化または促進します。さまざまな方法の中でも、プラズマ化学蒸着 (PECVD) は、プラズマを活用して従来の CVD 方法と比較して低温での蒸着を可能にする著名なアプローチです。プラズマベースの方法は、温度に敏感な基板上に高品質の薄膜を堆積するのに特に有利です。以下では、そのメカニズム、利点、用途に焦点を当てて、プラズマ蒸着の主要な方法を検討します。
重要なポイントの説明:
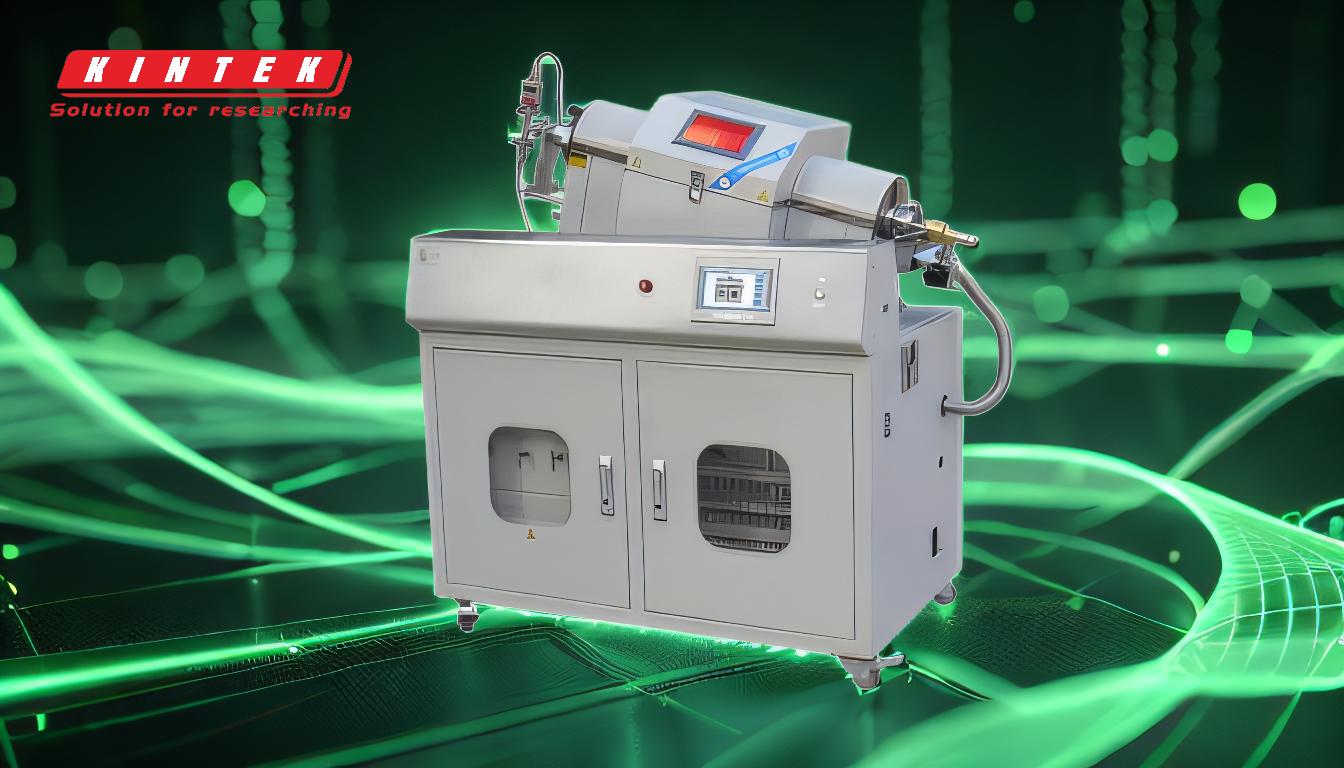
-
プラズマ化学蒸着 (PECVD)
- PECVD は、最も広く使用されているプラズマ堆積法の 1 つです。プラズマを利用して前駆体ガスから反応種を生成し、基板上に堆積して薄膜を形成します。
- プラズマは、前駆体ガス内の化学結合を切断するのに必要なエネルギーを提供し、低温での堆積を可能にします。
- この方法は、半導体や太陽電池の製造で一般的に使用される窒化シリコン、二酸化シリコン、アモルファスシリコンなどの材料を堆積するのに最適です。
- 詳しくはこちら 化学蒸着 およびその血漿強化型。
-
マイクロ波プラズマ化学蒸着 (MPCVD)
- MPCVD では、マイクロ波エネルギーを使用してプラズマを生成し、前駆体ガスをイオン化し、堆積プロセスを促進します。
- この方法は、高品質のダイヤモンド膜やその他の先端材料を製造できることで知られています。
- マイクロ波を使用すると均一なプラズマ分布が保証され、一貫した膜特性が得られます。
-
リモートプラズマ化学蒸着 (RPECVD)
- RPECVD では、基板から離れた場所でプラズマが生成されるため、高エネルギー イオンによる基板損傷のリスクが軽減されます。
- この方法は、ポリマーや有機材料などのデリケートな基板上に膜を堆積する場合に特に役立ちます。
- RPECVD は、光電子デバイスやフレキシブルエレクトロニクスの製造によく使用されます。
-
低エネルギープラズマ化学蒸着 (LEPECVD)
- LEPECVD は、低エネルギーのプラズマを使用して基板へのダメージを最小限に抑えながら、効率的な成膜を可能にします。
- この方法は、ナノテクノロジーやマイクロエレクトロニクスなど、膜の厚さと組成を正確に制御する必要がある用途に適しています。
-
原子層化学蒸着 (ALCVD)
- ALCVD は原子層堆積 (ALD) とプラズマ活性化を組み合わせて、高度に制御された均一な薄膜を実現します。
- プラズマは前駆体ガスの反応性を高め、正確な層ごとの成長を可能にします。
- この方法は、High-k 誘電体や半導体デバイス用のその他の先端材料の製造に広く使用されています。
-
燃焼化学蒸着 (CCVD)
- CCVD では、燃焼炎を使用してプラズマを生成し、薄膜を堆積します。
- この方法は費用対効果が高く、拡張性が高いため、大面積のコーティングや工業用途に適しています。
- CCVD は、金属酸化物やその他の機能性コーティングの堆積によく使用されます。
-
ホットフィラメント化学蒸着 (HFCVD)
- HFCVD では、高温のフィラメントを利用してプラズマを生成し、前駆体ガスを分解します。
- この方法は、ダイヤモンド ライク カーボン (DLC) フィルムやその他の硬質コーティングの堆積に一般的に使用されます。
- HFCVD はそのシンプルさと堅牢性により、産業用途でよく選ばれています。
これらのプラズマ蒸着方法はそれぞれ、基板の適合性、膜品質、プロセスの拡張性など、アプリケーションの特定の要件に応じて独自の利点を提供します。これらの方法はプラズマを活用することで、より低温での高性能薄膜の堆積を可能にし、さまざまな産業にわたってその用途を拡大しています。
概要表:
方法 | 主な特長 | アプリケーション |
---|---|---|
PECVD | 低温成膜にはプラズマを使用します。半導体や太陽電池に最適です。 | 窒化ケイ素、二酸化ケイ素、アモルファスシリコンの堆積。 |
MPCVD | マイクロ波で生成されたプラズマ。高品質のダイヤモンド膜を生成します。 | 先進的な材料、均一なフィルム特性。 |
RPECVD | 遠隔プラズマ生成。基板へのダメージを軽減します。 | オプトエレクトロニクス、フレキシブルエレクトロニクス、繊細な基板。 |
LEPECVD | 低エネルギープラズマ。基板へのダメージを最小限に抑えます。 | ナノテクノロジー、マイクロエレクトロニクス、精密なフィルム制御。 |
ALCVD | ALD とプラズマ活性化を組み合わせます。正確な層ごとの成長。 | High-k 誘電体、半導体デバイス。 |
CCVD | 燃焼炎により生成されるプラズマ。コスト効率が高く、拡張性にも優れています。 | 大面積コーティング、金属酸化物、工業用途。 |
HFCVD | 熱いフィラメントで生成されたプラズマ。堅牢かつシンプル。 | ダイヤモンドライクカーボン(DLC)膜、ハードコーティング。 |
薄膜製造プロセスを強化する準備はできていますか? 今すぐお問い合わせください プラズマ蒸着ソリューションの詳細については、こちらをご覧ください。