熱蒸着(TVD)、特に熱蒸発法は、その簡便さと費用対効果の高さから、薄膜蒸着において広く使われている技術である。しかし、TVDにはいくつかの欠点があり、特定のシナリオでの適用を制限している。これらの欠点には、膜の均一性の低さ、不純物レベルの高さ、低密度の膜質、適度な膜応力、拡張性の制限などがある。さらに、熱蒸発法は比較的融点の低い材料に限られ、るつぼからの汚染を受けやすい。これらの制限により、高純度、高密度、または多成分の材料を必要とする高度な用途には適していません。
キーポイントの説明
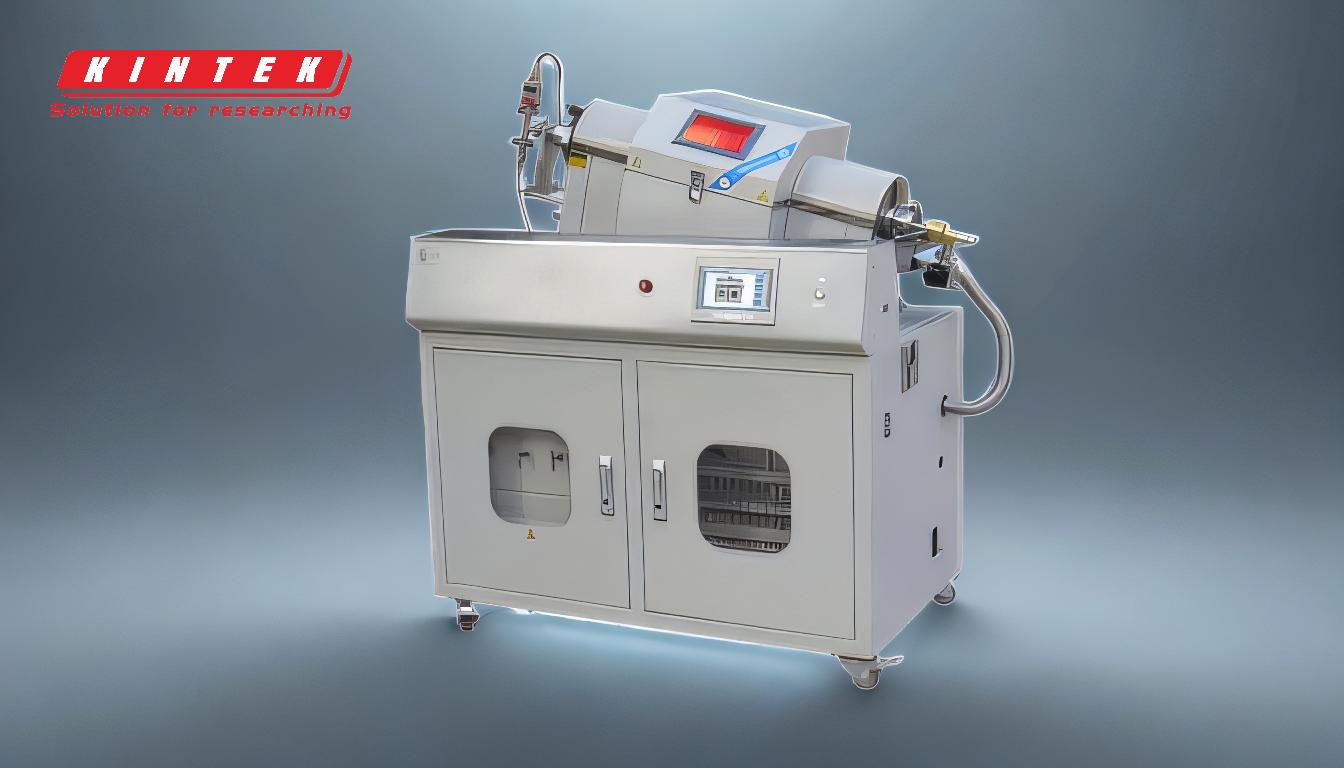
-
膜の均一性が悪い:
- プラネタリーシステムやマスクを使用しない場合、熱蒸発によって基板全体の膜厚が不均一になることが多い。これは、精密で均一なコーティングを必要とする用途にとっては重大な欠点である。
- 均一性の欠如は、材料特性の一貫性の欠如につながり、エレクトロニクスや光学のような産業では特に問題となる。
-
高い不純物レベル:
- 熱蒸着は一般的に、物理蒸着(PVD)法の中で最も不純物レベルが高い。これは、るつぼや蒸発源材料からの汚染によるものである。
- 不純物が多いと蒸着膜の性能が低下するため、半導体製造などの高純度用途には適さない。
-
低密度膜の品質:
- 熱蒸発法で製造された膜は密度が低いことが多く、機械的・電気的特性に影響を及ぼすことがある。これはイオンアシスト技術で改善できるが、プロセスが複雑になり、コストがかかる。
- 低密度フィルムは欠陥が発生しやすく、用途によっては必要な耐久性が得られない場合があります。
-
適度なフィルム応力:
- 熱蒸着によって成膜されたフィルムは、しばしば適度な応力を示し、経時的にクラックや層間剥離などの問題につながることがある。
- これは、フィルムが機械的ストレスや熱サイクルに耐える必要がある用途では特に問題となる。
-
限られたスケーラビリティ:
- 熱蒸着は、大面積や高スループットの用途には容易に拡張できない。このプロセスは、スパッタリングや化学気相成長(CVD)のような他の成膜方法と比べると、一般的に遅く、効率も低い。
- この制限により、工業規模の生産にはあまり魅力的ではない。
-
材料の制限:
- 熱蒸発法は、主に比較的融点の低い材料に適している。耐火性金属や非常に高い温度を必要とする材料の蒸着には有効ではない。
- このため、この方法で蒸着できる材料の範囲が制限され、汎用性が制限される。
-
るつぼの汚染:
- 熱蒸着においてるつぼを使用すると、蒸着膜に汚染物質が混入し、純度や品質がさらに低下する可能性がある。
- これは、半導体や光学産業など、高純度の材料を必要とする用途にとっては重大な欠点である。
-
多成分材料の課題:
- 熱蒸発は、蒸気圧、核生成、成長速度が成分によって異なるため、多成分材料の蒸着にはあまり効果的ではない。
- このため、多くの高度な用途に不可欠な均一な組成を達成することが難しくなる。
まとめると、熱蒸発法はシンプルでコスト効率の高い薄膜蒸着法ではあるが、均一性が低い、不純物レベルが高い、膜密度が低い、応力が中程度、拡張性に限界がある、材料に制限がある、るつぼが汚染される、多成分材料に課題があるなどの欠点があり、高度な用途や高精度の用途には適していない。熱蒸発法の詳細については、以下をご覧ください。 熱蒸発 .
総括表:
デメリット | 特徴 |
---|---|
膜の均一性が悪い | 厚みが均一でない、材料特性が一定でない、電子機器に問題がある。 |
高い不純物レベル | るつぼや原料からの汚染で、高純度用途には適さない。 |
低密度フィルムの品質 | 欠陥が発生しやすく、機械的・電気的特性に影響を与える。 |
中程度の膜応力 | クラックや剥離を引き起こし、機械的または熱的ストレス下で問題が発生する。 |
限られたスケーラビリティ | 大面積や高スループットの産業用アプリケーションには適さない。 |
材料の制限 | 低融点材料に限定されるため、汎用性が制限される。 |
るつぼの汚染 | 不純物が混入し、フィルムの純度と品質を低下させる。 |
多成分材料の課題 | 高度な用途で均質な組成を達成するのは難しい。 |
薄膜成膜のためのより良いソリューションが必要ですか? 当社の専門家に今すぐご連絡ください 先進的な選択肢をご検討ください!