スパッタリング堆積は薄膜堆積に広く使用されている技術ですが、効率、コスト、適用範囲に影響を与える可能性のあるいくつかの欠点があります。これらには、過熱、電荷の蓄積、材料の高コスト、化学量論制御の難しさ、反応性スパッタリングの課題などの問題が含まれます。これらの欠点を理解することは、特定の用途に適切な堆積方法を選択するために重要です。
重要なポイントの説明:
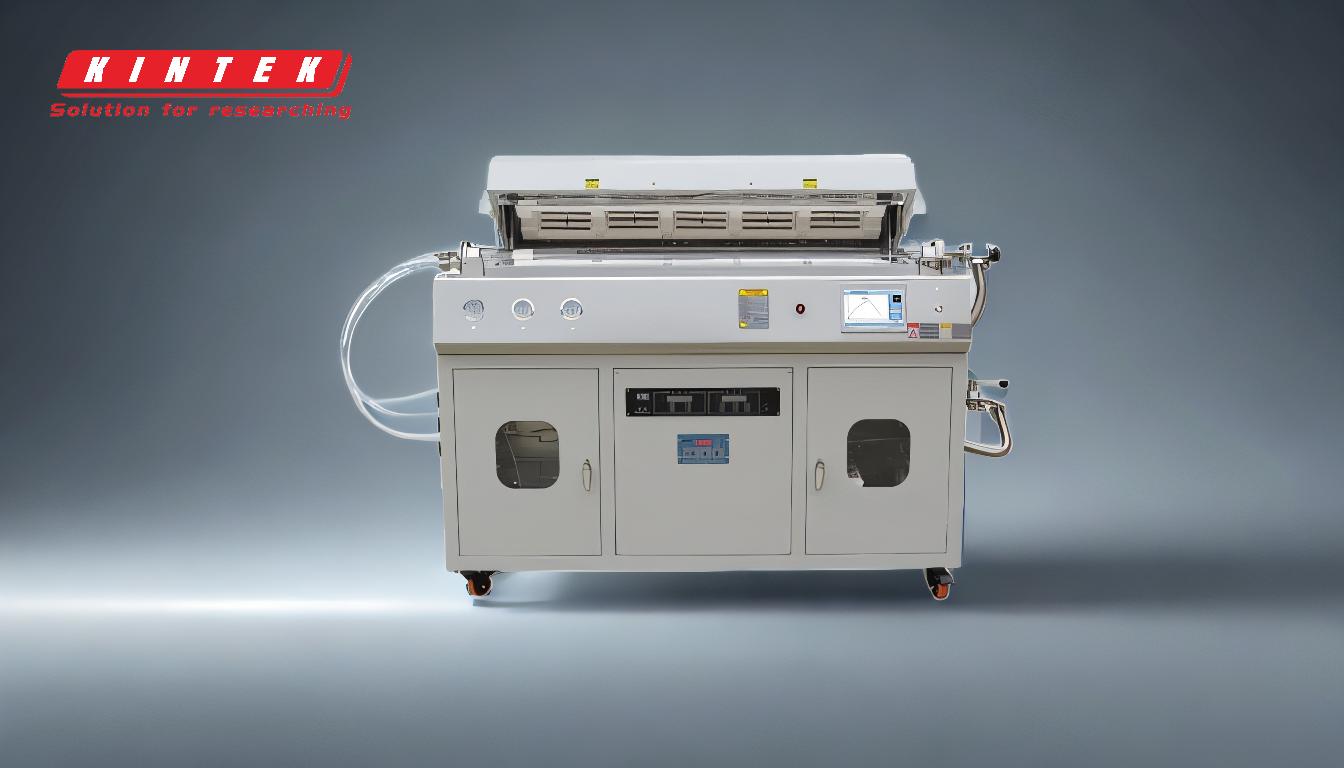
-
RFスパッタリングにおける過熱:
- RF スパッタリングでは、電波を生成するためにより高い電力入力が必要となるため、過熱が発生する可能性があります。これは、基板の完全性や堆積膜の品質を維持するために正確な温度制御が必要な用途では特に問題となります。
-
DCスパッタリングにおける電荷の蓄積:
- DC スパッタリングでは、チャンバー内に多数のイオンが存在するため、ターゲット材料に電荷が蓄積する可能性があります。これにより、アーク放電やターゲットへの損傷が発生し、蒸着プロセスの効率が低下し、薄膜に欠陥が生じる可能性があります。
-
材料費が高い:
- スパッタリングに使用される材料、特に金属は非常に高価になる場合があります。このコストの高さにより、予算の制約が重要な考慮事項となる特定の用途でのスパッタリングの使用が制限される可能性があります。
-
ストイキオメトリー制御の難しさ:
- 堆積膜で所望の化学組成(化学量論)を達成することは困難な場合があります。これは、複数の元素の堆積を正確に制御する必要がある複雑な材料に特に当てはまります。
-
反応性スパッタリングにおける課題:
- 反応性スパッタリングでは、反応性ガスを使用して基板上に化合物を形成するため、望ましくない結果が生じる可能性があります。これらには、非化学量論的化合物の形成や不純物の取り込みが含まれ、薄膜の性能を低下させる可能性があります。
-
装置の複雑さとコスト:
- スパッタリング システムは複雑で、設備とメンテナンスの面で多額の投資が必要です。高真空条件とプロセスパラメータの正確な制御の必要性により、システム全体のコストと複雑さが増大します。
-
制限された堆積速度:
- 他の堆積技術と比較して、スパッタリングは堆積速度が比較的低い場合があります。これは、速度が重要な要素である高スループットの製造プロセスでは不利になる可能性があります。
-
汚染の可能性:
- スパッタリングプロセスでは、特に真空チャンバーやターゲット材料が十分に清浄でない場合、薄膜に汚染物質が混入する可能性があります。これは、最終製品の品質と性能に影響を与える可能性があります。
これらの欠点を理解することは、さまざまな用途でスパッタリング堆積の使用について情報に基づいた決定を下すために不可欠です。高品質の薄膜や材料の多用途性など、多くの利点がありますが、特定のプロジェクトで最良の結果を確実に得るには、欠点を慎重に考慮する必要があります。
概要表:
短所 | 説明 |
---|---|
RFスパッタリングにおける過熱 | 高電力入力は過熱を引き起こし、基板の完全性と膜の品質に影響を与えます。 |
DCスパッタリングにおける電荷の蓄積 | イオンの蓄積はアーク放電を引き起こし、ターゲットに損傷を与え、蒸着効率を低下させます。 |
材料費が高い | 高価な材料、特に金属は、予算重視の用途を制限します。 |
ストイキオメトリー制御の難しさ | 複雑な材料の正確な化学組成を達成する際の課題。 |
反応性スパッタリングにおける課題 | 反応性ガスは非化学量論的化合物や不純物の原因となり、フィルムの性能を低下させる可能性があります。 |
装置の複雑さとコスト | システムの複雑さと真空要件により、機器とメンテナンスに多額の投資が必要になります。 |
制限された堆積速度 | 他の技術と比較して堆積速度が遅いため、高スループットプロセスに影響を与えます。 |
汚染の可能性 | 真空チャンバーまたはターゲットからの汚染物質は、膜の品質と性能を低下させる可能性があります。 |
プロジェクトに適した蒸着方法の選択にサポートが必要ですか? 今すぐ専門家にお問い合わせください カスタマイズされたソリューションを実現します。