物理的気相成長法(PVD)と化学的気相成長法(CVD)は、広く使用されている2つの薄膜蒸着技術であり、それぞれ異なる原理、プロセス、用途を持っている。主な違いは、成膜メカニズム、必要な温度、材料の適合性、得られるコーティング特性にあります。PVDは蒸発やスパッタリングなどの物理的プロセスによって薄膜を成膜するのに対し、CVDは気体状の前駆物質と基板との化学反応によって成膜する。PVDは低温で作動するため、熱に弱い材料に適しているのに対し、CVDは高温を必要とするため、より厚く複雑なコーティングが可能になる。どちらの方法にも独自の利点があり、PVDは耐久性と精度に優れ、CVDは汎用性が高く、より幅広い素材のコーティングが可能です。
キーポイントの説明
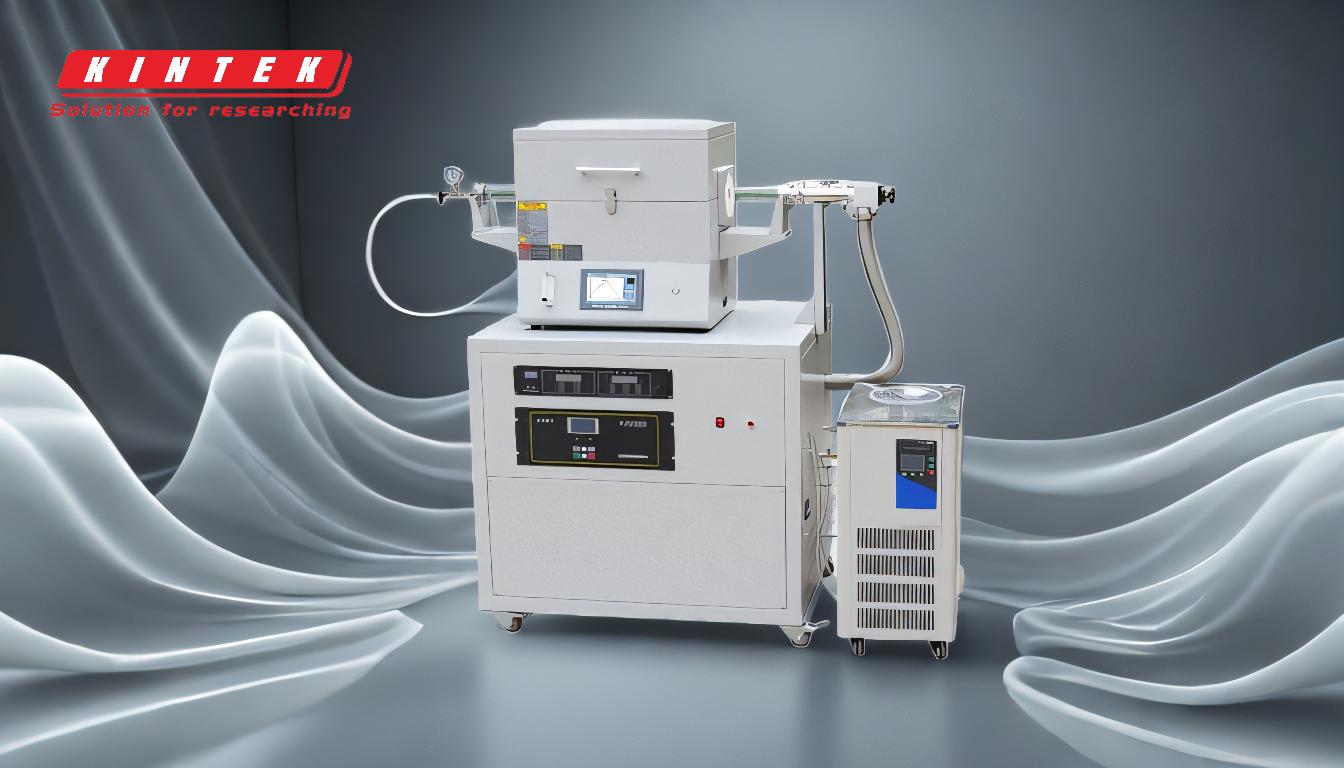
-
成膜メカニズム:
- PVD:蒸発、スパッタリング、イオンプレーティングなどの物理的プロセスを使用して、材料を固体ソースから基板に転写する。このプロセスでは、基板上に蒸気を凝縮させ、薄く滑らかなコーティングを形成する。
- CVD:気体状の前駆物質と基材表面の化学反応を利用する。気体は化学的に分解または反応して固体皮膜を形成し、この皮膜は多方向に蒸着される。
-
温度要件:
- PVD:比較的低い温度、通常250℃~450℃で作動する。このため、熱に敏感な材料や基板に適している。
- CVD:450℃から1050℃の高温を必要とする。高温は成膜に必要な化学反応を促進するが、高熱に耐えられない材料での使用は制限される。
-
素材適合性:
- PVD:主に金属やセラミックなどの固体コーティング材料を使用し、気化させて基材に蒸着させる。耐久性の高い超硬質薄膜(3~5μm)の形成に適している。
- CVD:ガス状の前駆体を利用するため、金属、セラミック、ポリマーなど、より多様な材料の成膜が可能。CVDコーティングは一般的に厚く(10~20μm)、複雑な形状にも適用できる。
-
コーティング特性:
- PVD:密着性に優れ、薄く滑らかで耐久性の高い皮膜を形成する。コーティングは圧縮応力を示すことが多く、断続切削(フライス加工など)などの用途に適している。
- CVD:被膜が厚くなり、粗くなることもある。高温プロセスにより引張応力が発生するため、CVDは連続切削加工(旋盤加工など)に適している。
-
プロセス環境:
- PVD:コンタミネーションを最小限に抑え、蒸着プロセスを正確に制御する真空条件下で実施。
- CVD:特定の用途に応じて、大気圧または減圧で行うことができる。このプロセスには、特殊な前駆体材料や、ガスの流量と組成の慎重な制御が必要とされることが多い。
-
アプリケーション:
- PVD:切削工具、医療機器、装飾コーティングなど、高い耐摩耗性が要求される用途によく使用される。低温での使用が可能なため、熱に弱い基材に最適。
- CVD:半導体製造、光学コーティング、高温環境の保護層など、厚く複雑なコーティングを必要とする用途に適している。
-
利点と限界:
- PVDの利点:高い耐久性、低温動作、コーティング膜厚の正確な制御。複雑な形状の場合、均一性が制限されることがある。
- CVDの利点:幅広い素材へのコーティングが可能で、複雑な形状への均一な成膜が可能。高温が要求されること、特殊な前駆体が必要であることなどが制限となる。
これらの重要な違いを理解することで、装置や消耗品の購入者は、精度、耐久性、材料適合性など、特定のニーズに最も適した蒸着法について、十分な情報を得た上で決定することができる。
総括表:
アスペクト | PVD | CVD |
---|---|---|
成膜メカニズム | 物理プロセス(蒸発、スパッタリング) | ガス状前駆体と基質との化学反応 |
温度 | 低 (250°C-450°C) | 高 (450°C-1050°C) |
素材適合性 | 金属、セラミックス(固体ソース) | 金属、セラミックス、ポリマー(ガス状前駆体) |
コーティング特性 | 薄く、滑らかで、耐久性がある(3~5μm) | より厚く、より粗い(10~20μm) |
プロセス環境 | 真空状態 | 大気圧または減圧 |
アプリケーション | 切削工具、医療機器、装飾コーティング | 半導体、光学コーティング、高温保護層 |
プロジェクトでPVDとCVDのどちらを使用するか決めるのにお困りですか? 専門家にご相談ください !