選択的レーザー焼結法(SLS)は、非常に複雑で機能的なパーツを最小限の後処理で製造できるなど、独自の利点を持つ3Dプリンティング技術である。しかし、装置や材料のコストが高く、熟練したオペレーターが必要であるなど、大きな欠点もあります。この技術は、複雑な設計を必要とする用途には特に適しているが、大規模生産には費用対効果が悪いかもしれない。対照的に粉末冶金は、加工中の摩擦により均一な部品が得られない可能性があるが、中程度の複雑な形状や大規模な製造には経済的である。
キーポイントの説明
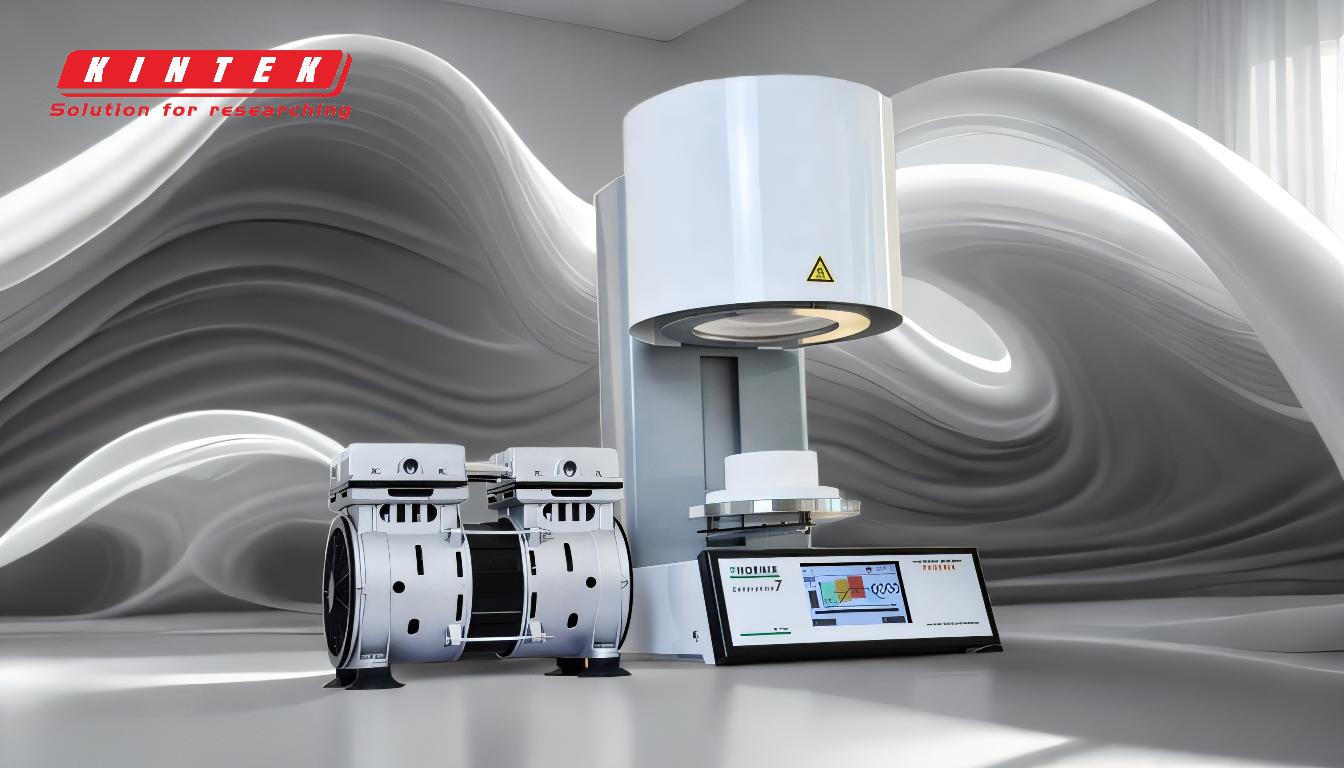
-
SLSの利点:
- 複雑で機能的な形状:SLSは、従来の焼結や粉末冶金では困難または不可能な複雑な形状を作り出すことに優れています。そのため、複雑な内部構造や微細なディテールを持つ部品の試作や製造に最適です。
- 最小限の後処理:SLSによって製造される部品は、多くの場合、追加の仕上げ加工をほとんど必要としません。
- 材料の多様性:SLS は、ポリマー、金属、セラミックなど、幅広い材料に対応できるため、特定の用途に合わせて柔軟に材料を選択できます。
-
SLSの欠点:
- 高いコスト:SLSマシンの初期投資額は大きく、25万ドルを超えることが多い。さらに、SLSに使用される材料は高価であるため、生産コスト全体がさらに上昇します。
- 熟練オペレーターの要件:SLSマシンの操作には専門的な知識とトレーニングが必要なため、人件費がかさみ、中小企業にとっては利用しにくい。
- 限られたスケーラビリティ:SLSは少量生産やプロトタイピングには優れているが、生産速度が遅く、単位あたりのコストが高いため、大規模な製造にはコスト効率が悪い。
-
粉末冶金との比較:
- 費用対効果:粉末冶金はSLSよりも一般的に安価であるため、中複雑部品の大規模生産に適しています。
- 操作の容易さ:SLSとは異なり、粉末冶金は熟練したオペレーターを必要としないため、人件費を削減し、製造工程を簡素化できる。
- 均一性の問題:しかし、粉末冶金では、プレス段階での粉末と金型間の摩擦により、部品が不均一になり、最終製品の機械的特性に影響を与える可能性がある。
-
用途と適性:
- SLS:航空宇宙部品、医療機器、カスタム金型など、高い複雑性が要求される用途に最適。機能的なプロトタイプを迅速に製造できるため、設計の反復が重要な産業で重宝される。
- 粉末冶金:自動車部品、ギア、ベアリングなど、中程度の複雑さを持つ部品の大量生産に適している。コスト効率と拡張性が高いため、大量生産に適している。
-
今後の検討事項:
- 技術の進歩:SLS技術が進化すれば、コストが下がり、このプロセスがより幅広い産業にとって利用しやすくなる可能性がある。材料科学の向上もSLSの応用範囲を広げる可能性がある。
- ハイブリッド・アプローチ:SLSを粉末冶金などの他の製造技術と組み合わせることで、複雑さ、コスト、拡張性のバランスを取ることができ、先端製造業に新たな可能性をもたらす可能性がある。
要約すると、SLSは複雑で機能的な部品を作るための比類ない能力を提供するが、コストと運用上の大きな課題を伴う。粉末冶金は、設計の複雑さという点では汎用性に劣るが、大規模生産にはより経済的なソリューションを提供する。これらの技術のどちらを選択するかは、複雑さ、生産量、予算の制約など、アプリケーションの具体的な要件によって決まる。
要約表
側面 | 選択的レーザー焼結 (SLS) | 粉末冶金 |
---|---|---|
複雑さ | 複雑なジオメトリや複雑な形状を得意とする。 | 中程度の複雑な形状に限定。 |
コスト | 設備費と材料費が高く、大規模生産ではコスト効率が悪い。 | 大規模生産ではより経済的。 |
後処理 | 必要な後処理は最小限。 | 均一性に問題があるため、追加仕上げが必要な場合がある。 |
オペレーター・スキル | 熟練したオペレーターが必要 | 操作が簡単なため、人件費が削減できる。 |
拡張性 | 少量生産や試作に最適。 | 大量生産に最適。 |
用途 | 航空宇宙、医療機器、カスタム工具 | 自動車部品、ギア、ベアリング。 |
SLSまたは粉末冶金により、お客様の製造プロセスがどのように変わるかをご覧ください。 今すぐご連絡ください までご連絡ください!