電子ビーム蒸着は高度な薄膜蒸着技術であり、高温の材料を蒸発させ、高い蒸着速度を正確に達成できるなど、独自の利点がある。しかし、設備コストが高い、電子回路が複雑、安全性に問題があるなどの欠点もある。この方法は、眼科用コーティングやソーラーパネルなど、高純度・高精度が要求される用途には特に適しているが、小規模・実験室での使用には費用対効果が悪いかもしれない。以下では、主な利点と欠点について詳しく説明する。
キーポイントの説明
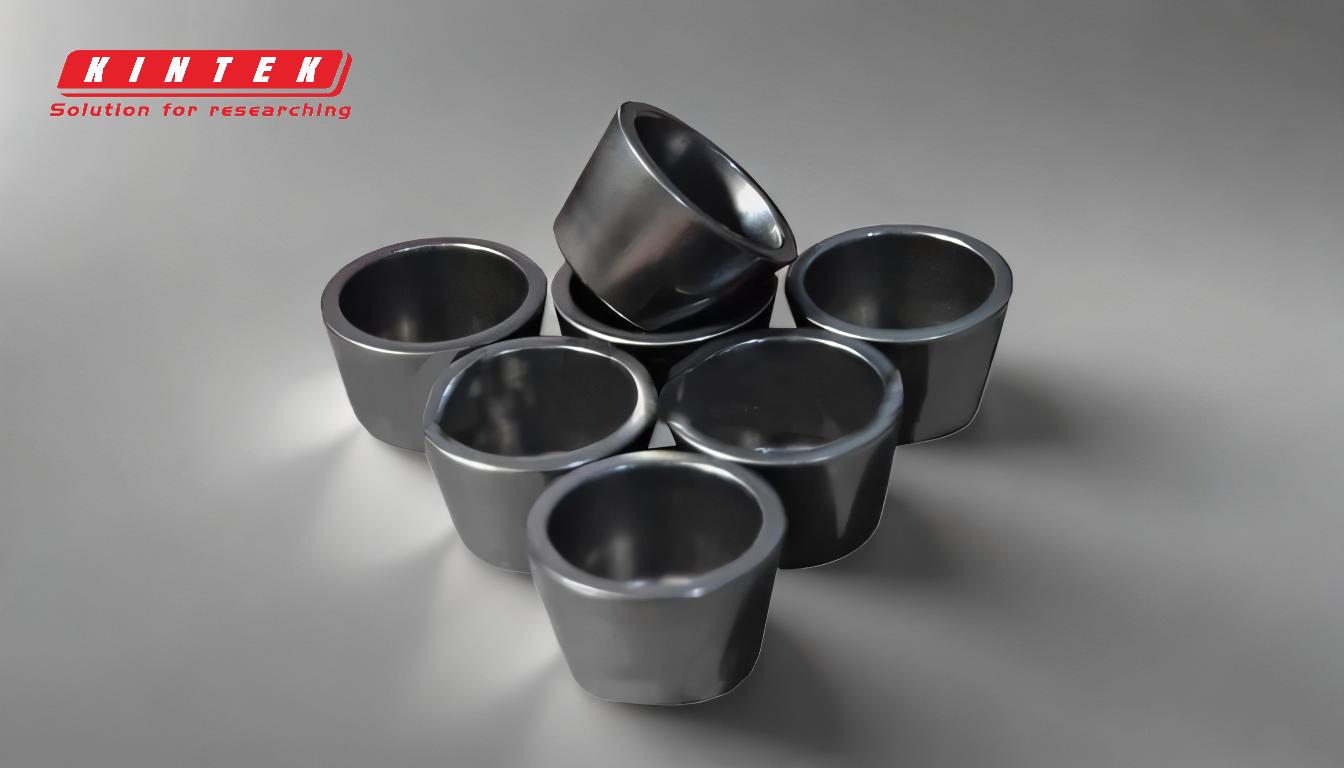
電子ビーム蒸着の利点:
-
高温物質を蒸発させる能力:
- 電子ビーム蒸発法は、材料を局所的に加熱することに優れているため、他の方法では加工が困難な耐火性金属やその他の高温材料の蒸発が可能である。
- この能力は、タングステンやタンタルのような高融点の材料を必要とする用途では極めて重要である。
-
高い蒸着率:
- このプロセスは非常に高い蒸着速度を達成できるため、大規模生産やスピードが重要な用途に効率的である。
- これは、スループットが重要な要素となるソーラーパネル製造のような業界では特に有益である。
-
精密さと純粋さ:
- 電子ビーム蒸着は、原子・分子レベルでの純粋で精密な金属皮膜の転写を可能にする。
- このため、光学コーティングや半導体製造など、高い精度が要求される用途に最適である。
-
真空適合材料による多用途性:
- この技術は、真空に適合する物質であれば、高温下で分解しない限り、ほとんどすべての物質を蒸発させることができる。
- この汎用性により、金属、セラミック、一部のポリマーなど、幅広い素材に適している。
-
局所暖房:
- 材料全体を加熱する抵抗蒸発とは異なり、電子ビーム蒸発は小さな領域にエネルギーを集中させるため、コンタミネーションが減少し、効率が向上する。
電子ビーム蒸着の欠点:
-
高い設備コスト:
- 電子ビーム蒸発に必要な装置は、フィラメント蒸発やボート蒸発よりもかなり高価である。
- そのため、小規模な事業や予算が限られている研究室にとっては、あまり魅力的な選択肢ではない。
-
複雑でコストのかかるドライブ・エレクトロニクス:
- この技術は複雑な駆動電子機器に依存しており、全体的なコストとメンテナンスの必要性を高めている。
- 電子ビームを正確に制御する必要があるため、システムの複雑さはさらに増す。
-
高電圧の安全上の危険
- このプロセスには高電圧がかかるため、オペレーターには重大な安全上のリスクがある。
- このようなリスクを軽減するためには、適切な安全プロトコルとトレーニングが不可欠であり、運用コストを増加させる。
-
限られたスケーラビリティ:
- 電子ビーム蒸着は抵抗蒸着ほど簡単に拡張できないため、大面積のコーティングや大量生産が必要な用途には適していない。
- この制限により、その使用は特定の高精度またはニッチな用途に限定される。
-
物質の分解リスク:
- この方法は幅広い材料に対応できるが、化合物によっては局所的な強い加熱で分解するものもあり、特定の有機材料やデリケートな材料への適用は制限される。
用途と適性:
-
高精度産業:
- 電子ビーム蒸着は、眼科用コーティング、半導体製造、ソーラーパネル製造など、高い精度と純度が要求される産業で広く使用されている。
- 高温の材料を扱い、精密なコーティングを提供するその能力は、これらの分野で不可欠なものとなっている。
-
ニッチで特殊なアプリケーション:
- この技術は、耐火性金属の蒸着や超薄膜の作成など、他の方法では不十分な特殊な用途に選ばれることが多い。
-
コストを考慮する:
- この技術は強力ではあるが、高コストで複雑なため、一般的な実験室での使用や小規模なプロジェクトでは実用的ではない。
- このような用途では、抵抗蒸着やスパッタリングのような、よりシンプルで費用対効果の高い方法が好まれるかもしれない。
結論
電子ビーム蒸着は、特に高精度で高温の用途において、明確な利点を持つ強力で汎用性の高い薄膜蒸着技術である。しかし、その高いコスト、複雑さ、安全性の懸念から、小規模な用途やあまり特殊でない用途には適していない。成膜法を選択する際には、これらの要因をアプリケーションの特定の要件と照らし合わせて、最も適切な技術を決定することが不可欠である。
総括表:
アスペクト | メリット | デメリット |
---|---|---|
高温材料 | タングステンやタンタルなどの耐火性金属を蒸発させることができる。 | 設備コストが高い。 |
堆積率 | 高い蒸着率を実現し、大量生産に最適。 | 複雑で高価な駆動エレクトロニクス。 |
精密さと純粋さ | 原子レベルの精度を実現し、光学コーティングや半導体に適している。 | 高電圧の安全上の危険 |
汎用性 | 金属やセラミックなど、真空と互換性のある材料に対応。 | 大面積コーティングのための拡張性に限界がある。 |
局所加熱 | 狭い範囲にエネルギーを集中させることで、汚染を減らす。 | 敏感な化合物に対する物質分解のリスク。 |
適切な薄膜形成法の選択にお困りですか? 専門家にご相談ください オーダーメイドのソリューションのために!