炭化ケイ素(SiC)発熱体は、高い動作温度を必要とする工業用および実験用の幅広い用途で使用される汎用性の高い高性能部品です。これらのエレメントは、高温珪化と再結晶化によって加工された高品質のグリーンカーバイド珪素から作られており、ロッド、ストリップ、プレート、U字型など、さまざまな形状があります。1625℃までの温度で使用可能で、セラミック焼成、ガラス製造、金属溶解、焼結、ろう付けなどのプロセスに最適です。その耐久性、効率性、極端な温度への耐性から、建設、冶金、エレクトロニクスなどの産業で好まれている。
キーポイントの説明
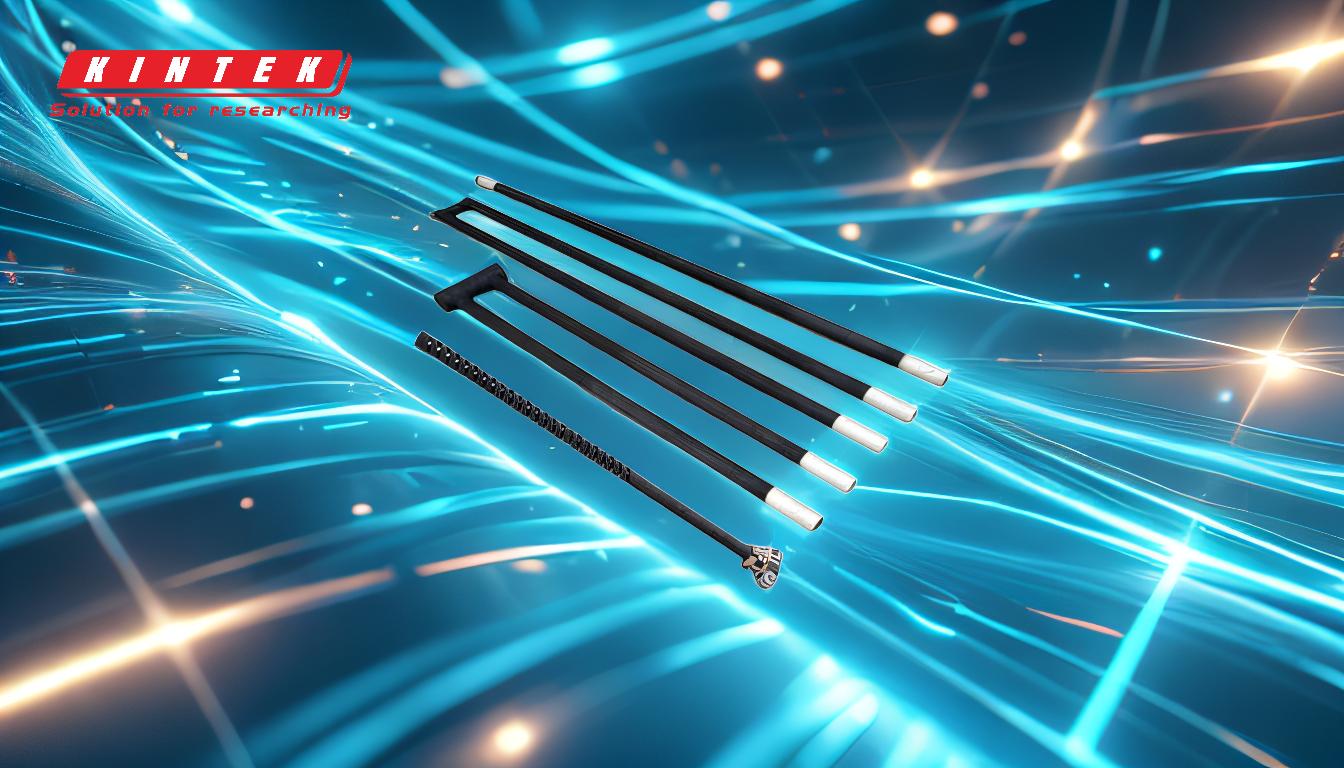
-
高温アプリケーション:
-
炭化ケイ素発熱体は、最高1625℃の超高温で動作するように設計されています。そのため、以下のような安定した高熱を必要とするプロセスに適しています:
- セラミック焼成:セラミックを高温で焼成し、適切な硬化と仕上げを行うための窯。
- フロートガラスの製造:精密で均一な加熱が要求される板ガラス製造に不可欠。
- 非鉄金属溶解:アルミニウム、銅、亜鉛などの金属を溶かす炉に使用される。
- 焼結とろう付け:材料が高熱下で接着または高密度化される冶金プロセスにおいて重要。
-
炭化ケイ素発熱体は、最高1625℃の超高温で動作するように設計されています。そのため、以下のような安定した高熱を必要とするプロセスに適しています:
-
工業および研究室での汎用性:
-
炭化ケイ素発熱体は、以下のような様々な機器に使用されています:
- 工業用電気炉:熱処理や材料試験などのプロセス用の中・高温工業炉で一般的に使用される。
- 実験用電気炉:精密な温度制御が必要な研究開発用途に最適。
- 水平管状炉および回転管状炉:制御された環境で均一な加熱を必要とするプロセス用の特殊炉に使用される。
-
炭化ケイ素発熱体は、以下のような様々な機器に使用されています:
-
耐久性と効率:
- 炭化ケイ素発熱体は、耐久性に優れ、過酷な使用条件にも耐えることで知られています。酸化や熱衝撃に強く、高温での連続使用でも長寿命です。そのため、メンテナンスコストとダウンタイムが削減され、産業用アプリケーションの費用対効果に優れたソリューションとなります。
-
カスタマイズ可能な形状と構成:
- このエレメントは、ロッド、ストリップ、プレート、U字型など、さまざまな形状で製造することができ、さまざまな炉の設計や用途に適合します。水平または垂直に設置でき、並列、直列、または混合構成で接続できるため、設計と運転に柔軟性があります。
-
先端産業への応用:
-
炭化ケイ素発熱体は、次のような先端産業で広く使用されています:
- エレクトロニクスと半導体:高純度材料と部品の製造のために。
- 耐火物と冶金:耐火物製造および金属加工用の炉。
- ガラスとクリスタルの製造:ガラス・水晶材料の溶解・成形用
-
炭化ケイ素発熱体は、次のような先端産業で広く使用されています:
-
他の発熱体との比較:
- 二珪化モリブデン(MoSi2)発熱体も高温用途で使用されていますが、炭化ケイ素発熱体は、酸化に対する耐性が高く、特定の工業プロセスでより優れた性能を発揮するなど、明確な利点があります。そのため、安定した信頼性の高い高温加熱を必要とする用途に適しています。
まとめると、炭化ケイ素発熱体は、高温能力、耐久性、汎用性が求められる産業やプロセスにおいて不可欠な存在です。極端な温度でも効率的に動作する能力とカスタマイズ可能な設計により、幅広い用途で信頼性が高く、コスト効率の高いソリューションとなっています。
概要表
特徴 | 詳細 |
---|---|
温度範囲 | 1625℃まで |
利用可能な形状 | ロッド、ストリップ、プレート、U字型 |
用途 | セラミック焼成、ガラス製造、金属溶解、焼結、ろう付け |
対象産業 | 建設, 冶金, エレクトロニクス, 半導体, 耐火物 |
主な利点 | 高耐久性、耐酸化性、耐熱衝撃性 |
カスタマイズ | 水平/垂直設置、並列/直列/混合構成 |
炭化ケイ素ヒーターで高温プロセスをアップグレードします。 今すぐ までご連絡ください!