プラズマ窒化層の厚さは、特定の用途やプロセスパラメータに応じて、通常、数百ナノメートルから数ミクロンの範囲になります。プラズマ窒化は、金属部品の耐摩耗性、疲労強度、耐食性を向上させる表面硬化技術です。窒化層の厚さは、材料組成、プロセス温度、持続時間、使用するプラズマの種類などの要因によって影響されます。ほとんどの産業用途では、基材の完全性を損なうことなく最適な性能を確保するために、窒化層の厚さが慎重に制御されます。
重要なポイントの説明:
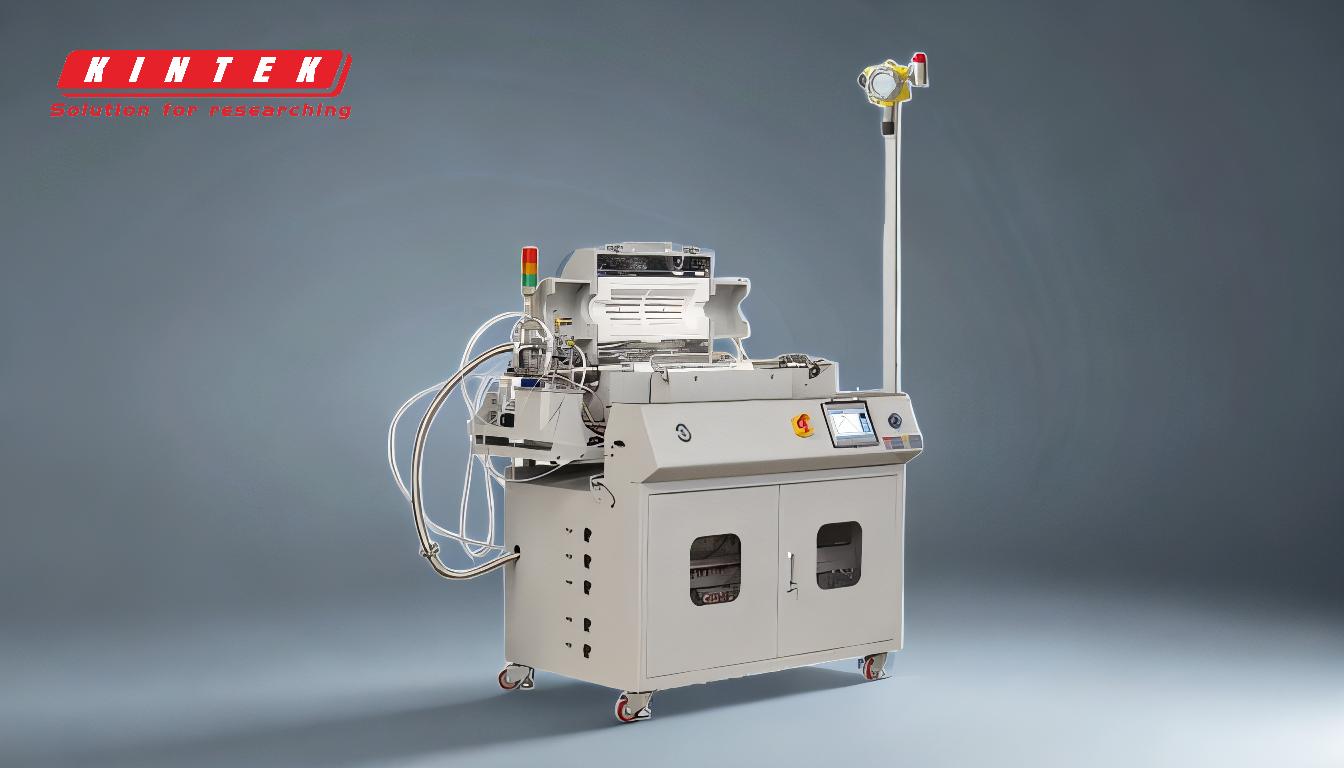
-
一般的な厚さの範囲:
- プラズマ窒化層の厚さは一般に次の範囲です。 0.25ミクロン~5ミクロン 。この範囲はほとんどの産業用途に適しており、表面硬度とコンポーネントの耐久性のバランスが取れています。
- 場合によっては、特に特殊な用途では、厚さが最大 10ミクロン 材料やプロセス条件によっては、それ以上になります。
-
厚さに影響を与える要因:
- 材料構成: 処理される材料の種類は、窒化層の厚さに大きく影響します。たとえば、合金元素の多い鋼は、窒素の拡散が促進されるため、より厚い層を形成する傾向があります。
- プロセス温度: 一般に、温度が高くなると窒素の拡散速度が増加し、窒化層が厚くなります。ただし、温度が高すぎると基材が劣化する可能性があります。
- プロセス期間: 窒化時間を長くすると窒素の拡散が大きくなり、層が厚くなります。時間と厚さの関係は、多くの場合、特定の範囲内では線形です。
- プラズマパラメータ: プラズマ ガス (窒素、水素、アルゴン混合物など) の電力、圧力、組成は窒化反応速度に影響し、その結果層の厚さに影響します。
-
測定と制御:
- 窒化層の厚さは通常、次のような手法を使用して測定されます。 微小硬度試験 、 光学顕微鏡 、 または 走査型電子顕微鏡 (SEM) 。これらの方法により、品質管理のための正確で信頼性の高いデータが提供されます。
- 所望の層の厚さと均一性を達成するには、窒化プロセスの正確な制御が不可欠です。高度なプラズマ窒化システムには、一貫した結果を保証するためのリアルタイム監視およびフィードバック メカニズムが組み込まれていることがよくあります。
-
アプリケーションと考慮事項:
- 耐摩耗性: 厚い窒化層は、ギア、ベアリング、切削工具など、高い耐摩耗性が必要な用途でよく使用されます。
- 疲労強度: 繰り返し荷重を受けるコンポーネントの場合、窒化層を注意深く制御することで疲労寿命を大幅に向上させることができます。
- 耐食性: プラズマ窒化は主に耐摩耗性を向上させますが、特に酸化などの後処理プロセスと組み合わせることで、ある程度の耐食性も提供します。
-
他の表面処理との比較:
- 浸炭や物理蒸着 (PVD) などの他の表面硬化技術と比較して、プラズマ窒化は硬度、密着性、均一性の独自の組み合わせを提供します。多くの場合、窒化層の厚さは他の方法よりも安定しており、制御が容易です。
これらの重要なポイントを理解することで、機器および消耗品の購入者は、プラズマ窒化プロセスについて情報に基づいた決定を下すことができ、選択したパラメータと機器がアプリケーションの特定の要件を確実に満たすことができます。
概要表:
側面 | 詳細 |
---|---|
一般的な厚さの範囲 | 0.25ミクロン~5ミクロン(特殊用途の場合は最大10ミクロン) |
厚さに影響を与える要因 | 材料組成、プロセス温度、継続時間、およびプラズマパラメータ |
測定技術 | 微小硬度試験、光学顕微鏡、SEM |
主な用途 | 耐摩耗性、疲労強度、耐食性 |
他の方法との比較 | 浸炭やPVDよりも安定性が高く、制御が容易 |
プラズマ窒化プロセスを最適化するためのサポートが必要ですか? 今すぐ専門家にお問い合わせください カスタマイズされたソリューションを実現します。