熱間鍛造と冷間鍛造は、ユニークな特性、利点、および欠点を持つ2つの異なる金属加工プロセスです。熱間鍛造は、一般的に再結晶点以上の高温で金属を成形するのに対し、冷間鍛造は室温または室温付近で行われる。これらの方法のどちらを選択するかは、材料特性、所望の部品の複雑さ、生産量、コスト考慮などの要因に依存します。以下では、2つのプロセスの違い、用途、限界に焦点を当て、詳細に比較しています。
キーポイントの説明
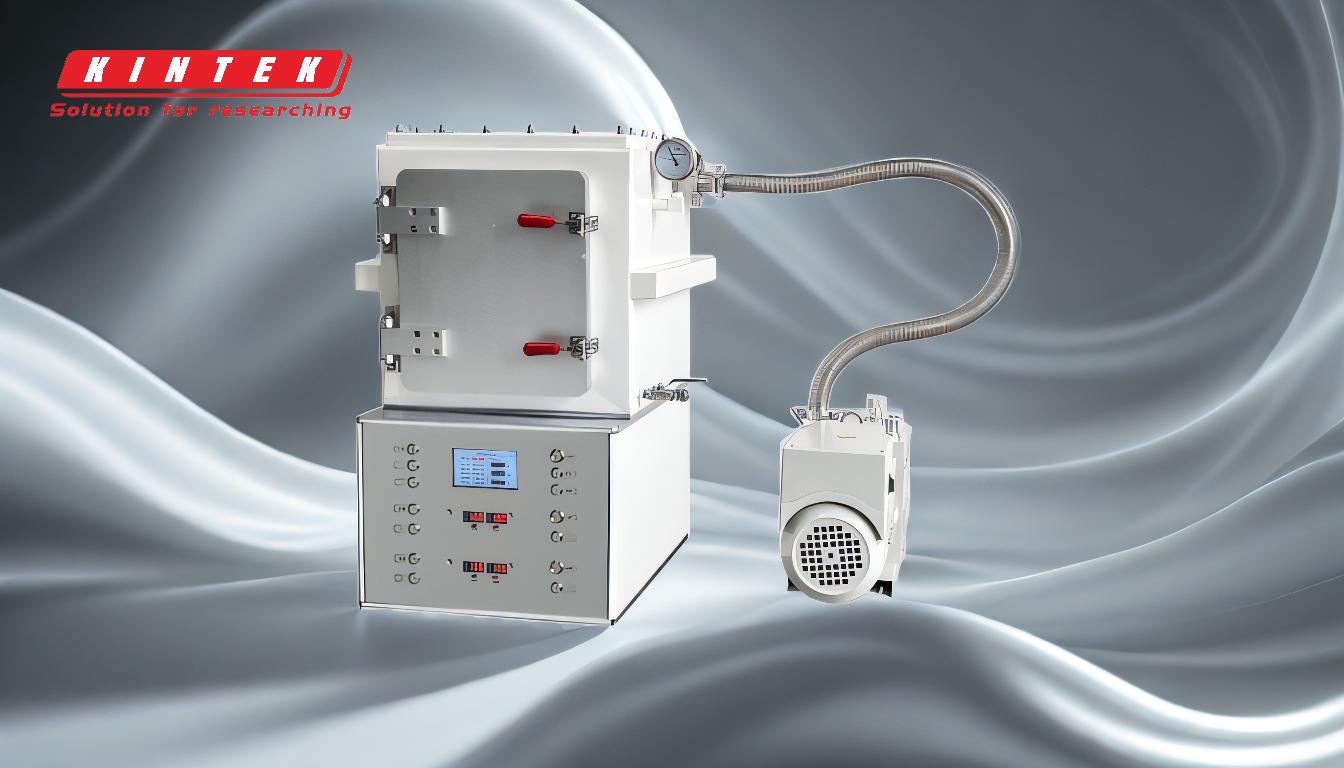
-
温度と素材の挙動:
- 熱間鍛造:金属の再結晶点以上の温度で行われ、鋼の場合は通常950℃から1250℃の間。この高温によって金属の降伏強度が低下し、成形や変形が容易になる。このプロセスはまた、結晶粒組織を微細化し、靭性や延性などの機械的特性を向上させる。
- 冷間鍛造:室温または室温付近で伝導する。金属は高い降伏強度を保持し、変形させるためにより大きな力を必要とする。冷間鍛造は、ひずみ硬化によって材料の強度を高めるが、延性を低下させる可能性がある。
-
組織と機械的性質:
- 熱間鍛造:プロセス中の再結晶により、微細で均一な結晶粒組織が得られます。これにより、材料の靭性と耐疲労性が向上し、高応力用途に適している。
- 冷間鍛造:ひずみ硬化が起こり、材料の強度と硬度が向上する。しかし、再結晶が起こらないため、残留応力や延性が低下し、材料特性を回復するために焼鈍が必要になる可能性がある。
-
部品の複雑さと精度:
- 熱間鍛造:高温での金属の流動特性により、あまり複雑でない大きな部品に適している。厳しい公差を達成するのは難しく、しばしば二次加工が必要になる。
- 冷間鍛造:より小さく、より複雑な部品を、より高精度に、より優れた表面仕上げで製造できる。そのため、追加の機械加工の必要性が減り、大量生産において費用対効果が高くなる。
-
金型コスト:
- 熱間鍛造:金型は極端な温度と磨耗にさらされるため、頻繁なメンテナン スや交換が必要になる。このため、金型費用が増加し、少量生産では熱間鍛造の経済性が低くなる。
- 冷間鍛造:金型の熱応力が小さく、工具寿命が長い。しかし、金型の初期設計と製造コストが高くなるため、大規模生産に適している。
-
素材適性:
- 熱間鍛造:鋼、チタン、ニッケル合金など変形抵抗の高い金属に最適。低温での成形が難しい素材にも用いられる。
- 冷間鍛造:アルミニウム、銅、低炭素鋼のような柔らかい金属に最適で、過度の力を加えなくても容易に変形させることができる。
-
エネルギー消費と環境への影響:
- 熱間鍛造:金属を高温に加熱するために多大なエネルギーを必要とし、エネルギー消費量と環境負荷が高くなる。
- 冷間鍛造:加熱が不要なためエネルギー効率が高く、環境に優しい。
-
用途:
- 熱間鍛造:航空宇宙、自動車(クランクシャフト、コネクティングロッドなど)、重機械など、高強度部品を必要とする産業で一般的に使用されている。
- 冷間鍛造:ファスナー、ボルト、スクリュー、その他自動車産業やエレクトロニクス産業における小型で高精度な部品の生産に適している。
-
制限事項:
- 熱間鍛造:微細構造の制御が限定的で、二次加工要件が高く、多孔質または多材料の部品を製造できない。金型コストが高く、短納期生産には不向き。
- 冷間鍛造:より軟らかい金属やより単純な形状に限定される。ひずみ硬化は、延性を回復するために追加の熱処理が必要になる場合がある。
要約すると、熱間鍛造と冷間鍛造にはそれぞれ明確な利点と限界があります。熱間鍛造は、洗練された結晶粒構造を持つ大 型の高強度部品に理想的であり、一方、冷間鍛造は、 最小限の機械加工で小型の精密部品を製造するのに優れてい る。両者の選択は、材料特性、部品の複雑さ、生産量を含む用途の特定の要件に依存します。
要約表
側面 | 熱間鍛造 | 冷間鍛造 |
---|---|---|
温度 | 再結晶点以上(鋼の場合950℃~1250) | 室温または室温付近 |
材料の挙動 | 降伏強度の低下、結晶粒組織の微細化、靭性と延性の向上 | 高降伏強さ、ひずみ硬化、強度の向上、延性の低下 |
部品の複雑さ | 大型で複雑度の低い部品に最適 | 高精度で複雑な小型部品に最適 |
金型コスト | 極端な温度と摩耗のため高い | 熱応力が低く、工具寿命が長い。 |
材料適性 | 鋼、チタン、ニッケル合金 | アルミニウム、銅、低炭素鋼 |
エネルギー消費 | 暖房による高いエネルギー消費 | エネルギー効率に優れ、加熱が不要 |
用途 | 航空宇宙、自動車(クランクシャフト、コンロッド)、重機械 | ファスナー、ボルト、ネジ、自動車、電子機器 |
制限事項 | 組織制御の制限、二次加工、高い金型コスト | より軟らかい金属に限定され、ひずみ硬化には焼鈍が必要な場合がある。 |
お客様のプロジェクトに適した鍛造プロセスの選択にお困りですか? 当社の専門家に今すぐご連絡ください !