ダイヤモンドライクコーティング(DLC)は、主に化学的気相成長法(CVD)や物理的気相成長法(PVD)といった高度な成膜技術を用いて施される。マイクロ波プラズマCVD(MPCVD)、DCアークプラズマスプレーCVD(DAPCVD)、ホットワイヤーCVD(HFCVD)などのCVD法は、チャンバー内でガス分子(水素やメタンなど)を分解し、工具表面に純粋なダイヤモンド膜を堆積させます。一方、PVDは、原料を蒸発させて工具上に凝縮させ、薄いDLC層を形成します。これらのプロセスでは、高品質のコーティングを実現するために、温度、ガス組成、エネルギー源を正確に制御する必要があります。
キーポイントの説明
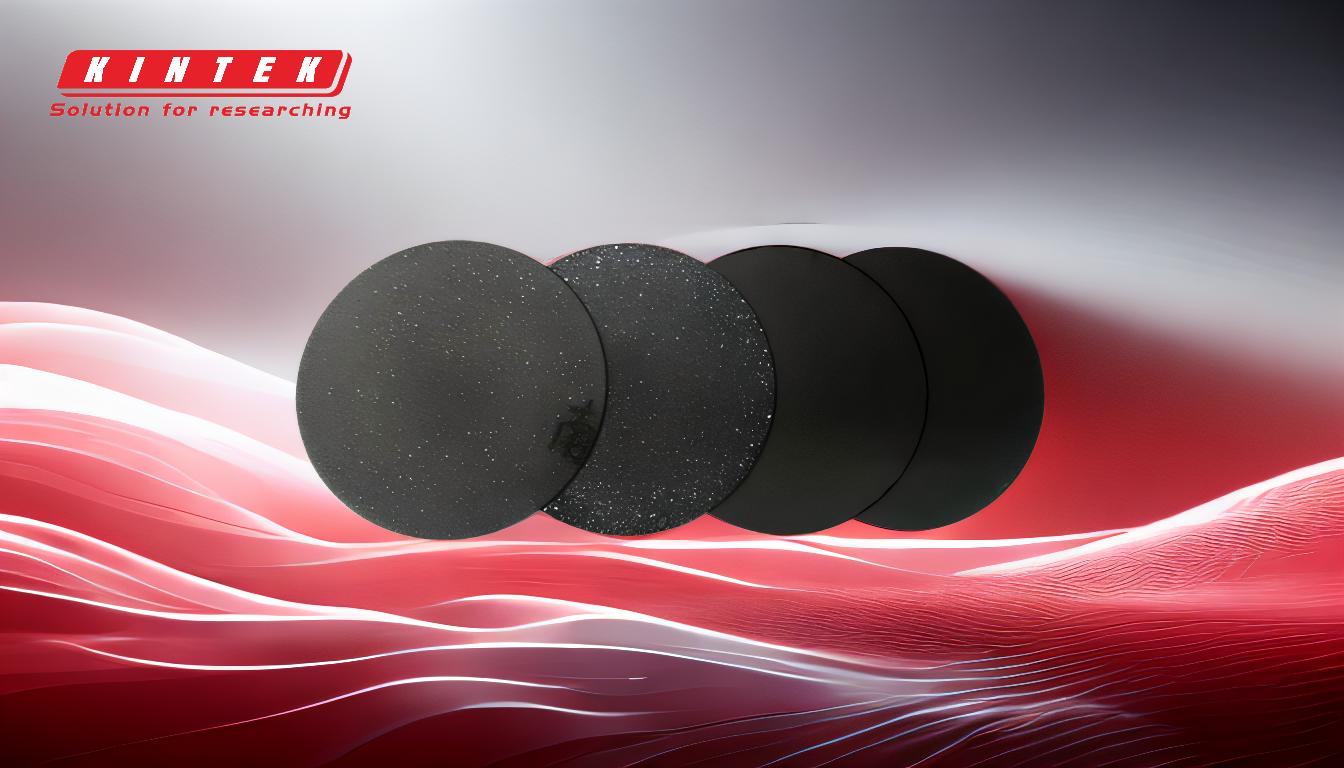
-
化学気相成長(CVD)法:
- マイクロ波プラズマCVD (MPCVD):この技術では、マイクロ波エネルギーを使ってプラズマを発生させ、水素やメタンなどのガス分子を反応性の炭素原子に分解する。これらの原子は基板上に堆積し、ダイヤモンドのようなコーティングを形成する。MPCVDは、高品質で均一なコーティングを生成することで知られている。
- DCアークプラズマスプレーCVD (DAPCVD):この方法では、直流アークを使用して高エネルギーのプラズマを発生させる。プラズマは混合ガスを分解し、その結果生じた炭素原子が工具表面に堆積する。DAPCVDは、複雑な形状や大きな表面のコーティングに効果的です。
- ホットワイヤーCVD (HFCVD):このプロセスでは、タングステンワイヤーを2,300℃以上に加熱して混合ガスを分解する。その後、活性化された炭素原子が基板上に堆積し、ダイヤモンド膜が形成される。HFCVD法は高温用途に適しており、優れた密着性を実現します。
-
物理蒸着(PVD)法:
- DLCコーティング用PVD:PVDは、真空チャンバー内で原料を蒸発させ、工具表面に凝縮させる。この方法は、非晶質でsp2とsp3の炭素結合が混在するダイヤモンドライクカーボン(DLC)コーティングの成膜に使用されます。PVDは、摩擦が少なく耐摩耗性に優れた、薄くて硬いコーティング(厚さ0.5~2.5ミクロン)を形成するのに理想的です。
-
プロセスパラメーターと条件:
- ガス組成:水素とメタンに代表されるガスの選択は、望ましい炭素析出を達成するために非常に重要である。これらのガスの比率は、コーティングの品質と特性に影響する。
- 温度コントロール:ガス分子を活性化し、適切な成膜を行うには高温(750℃以上)が必要である。欠陥を防ぎ、均一なコーティングを実現するためには、正確な温度制御が不可欠である。
- エネルギー源:成膜プロセスに必要なプラズマや熱を発生させるために、マイクロ波、DCアーク、加熱フィラメントなど、さまざまなエネルギー源が使用される。エネルギー源の選択は、特定のCVD法と希望するコーティング特性によって決まります。
-
用途と利点:
- 工具コーティング:ダイヤモンドライクコーティングは、優れた硬度、耐摩耗性、低摩擦性を提供することにより、ドリルやエンドミルなどの切削工具の性能を向上させるために広く使用されています。
- 工業用途:これらのコーティングは、耐久性と性能が重要な自動車部品、医療機器、電子機器など、さまざまな産業用途にも使用されています。
これらの重要なポイントを理解することで、機器や消耗品の購入者は、特定のニーズに適したコーティング方法について十分な情報を得た上で決定することができ、工具や部品の最適な性能と寿命を確保することができます。
まとめ表
方法 | 主な特徴 | 用途 |
---|---|---|
MPCVD | マイクロ波エネルギーを使用し、均一で高品質なコーティングを実現 | 切削工具、電子機器、高精度部品 |
DAPCVD | 複雑な形状や大きな表面をコーティングするためのDCアークプラズマ | 自動車部品、産業用工具、大規模アプリケーション |
HFCVD | 高温用加熱タングステンワイヤーと優れた密着性 | 高温工具、医療機器、耐久性コーティング |
PVD | 薄く、硬く、摩擦の少ないコーティングのために、原料を蒸発・凝縮させる。 | 耐摩耗性、低摩擦性、薄いコーティング(0.5~2.5 µm)を必要とする工具 |
お客様のニーズに最適なDLCコーティングをご提案します。 今すぐ専門家にご相談ください !