化学的蒸着と物理的蒸着は、薄膜製造に用いられる2つの異なる技術であり、それぞれに独自のプロセス、利点、限界がある。化学蒸着(CVD)のような化学的蒸着は、薄膜を形成するために化学反応に依存し、多くの場合、高温を必要とし、不純物が生じる可能性がある。対照的に、物理蒸着(PVD)のような物理的蒸着は、基板上に材料を物理的に移動させるもので、一般的に低温で、腐食性の副生成物を伴わない。これらの違いを理解することは、希望するフィルム特性、基板との互換性、アプリケーションの要件に基づいて適切な方法を選択する上で非常に重要です。
キーポイントの説明
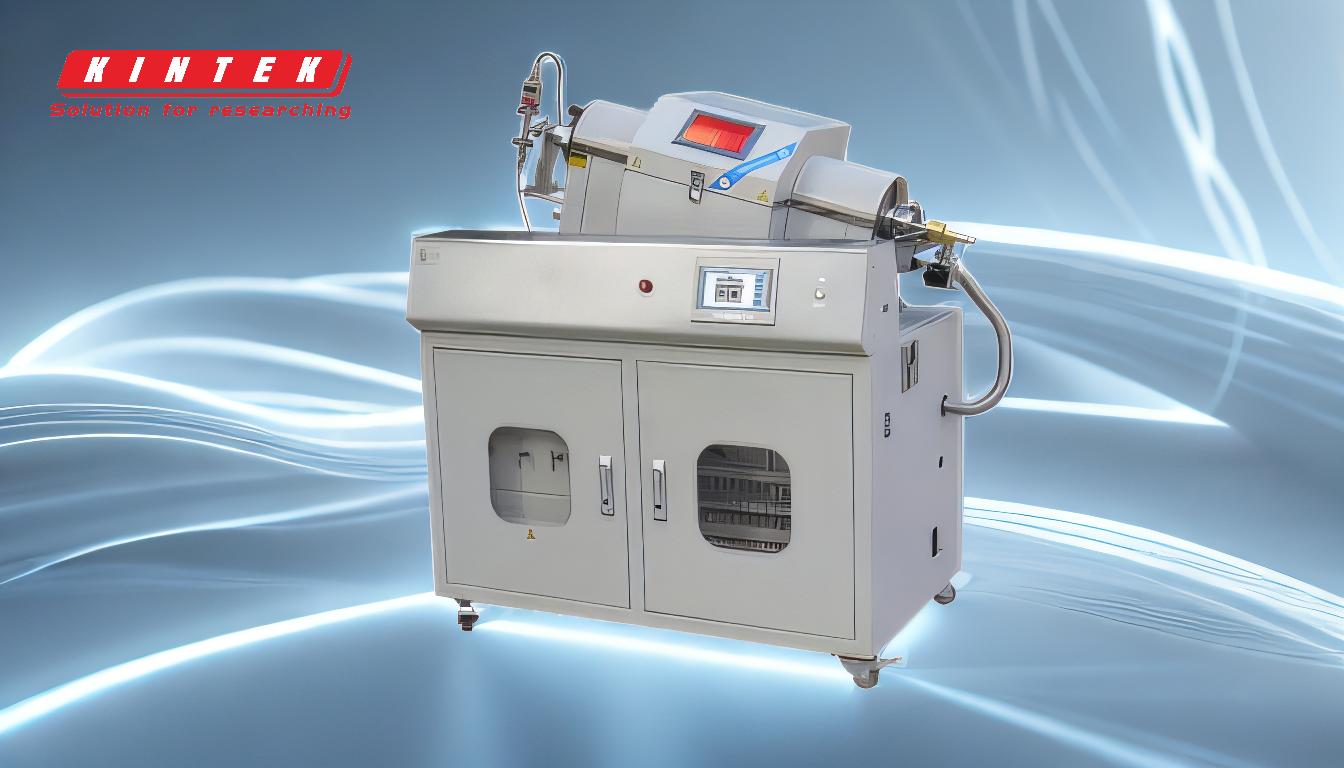
-
プロセスのメカニズム:
-
化学蒸着 (CVD):
- 気体状の前駆物質が化学反応を起こし、基材上に固体皮膜を形成する。
- 化学反応を活性化するために高温が必要で、腐食性のガス状副生成物の形成につながることが多い。
- 例えば、熱CVD、プラズマエンハンストCVD(PECVD)、原子層堆積法(ALD)などがある。
-
物理蒸着(PVD):
- ソース(スパッタリングや蒸着など)から基板への材料の物理的な移動を伴う。
- 化学反応に依存しないため、低温での成膜が可能。
- 例えば、スパッタリング、蒸着、電子ビーム物理蒸着(EBPVD)などがある。
-
化学蒸着 (CVD):
-
温度条件:
-
CVD:
- 通常、化学反応と膜の成長を促進するために高温(多くの場合500℃以上)を必要とする。
- 高温下では、材料によっては劣化や反りが生じるため、使用できる基板の種類が制限されることがある。
-
PVD:
- はるかに低い温度で実施できるため、熱に敏感な基板に適している。
- また、低温であれば、基板の損傷や変形のリスクも低減できる。
-
CVD:
-
膜の純度と不純物:
-
CVD:
- 化学反応は、特に前駆体や反応条件を注意深く管理しないと、フィルムに不純物を混入させる可能性がある。
- また、腐食性の副生成物が形成されることもあり、廃棄物の管理と安全性を確保するための新たな手順が必要となる。
-
PVD:
- 化学反応ではなく物理的な移動に基づくプロセスであるため、一般的に高純度のフィルムが得られる。
- 腐食性の副生成物が発生しないため、廃棄物管理が簡素化され、安全上の懸念も軽減される。
-
CVD:
-
蒸着率:
-
CVD:
- 一般的にPVDに比べて成膜速度が速く、厚膜を必要とする用途に適している。
- ただし、成膜速度は特定のCVD技術とプロセス・パラメーターによって異なる場合がある。
-
PVD:
- 一般に成膜速度は低いが、EBPVDのような技術では0.1~100μm/分の成膜速度を達成できる。
- 成膜速度の低さは、高品質で均一な膜を製造する能力によって相殺されることが多い。
-
CVD:
-
材料利用効率:
-
CVD:
- 副生成物の生成や前駆体ガスの潜在的な無駄により、材料の利用効率が低下する可能性がある。
-
PVD:
- EBPVDのような技術は、材料利用効率が非常に高いため、特定の用途では費用対効果が高い。
-
CVD:
-
用途:
-
CVD:
- 半導体製造、工具のコーティング、光学・電子デバイス用薄膜の製造によく使用される。
- 高温安定性と複雑な化学組成を必要とする用途に適している。
-
PVD:
- マイクロエレクトロニクス、光学、装飾コーティング用の薄膜製造に広く使用されている。
- 高純度フィルムや熱に敏感な基板との互換性を必要とする用途に最適。
-
CVD:
これらの重要な違いを理解することで、装置や消耗品の購入者は、温度要件、膜純度、蒸着速度、材料効率などの要素をバランスさせながら、特定のニーズに最も適した蒸着方法について、十分な情報を得た上で決定することができます。
要約表
側面 | 化学蒸着 (CVD) | 物理蒸着 (PVD) |
---|---|---|
プロセスメカニズム | 基板上に固体膜を形成するために、気体状前駆体間の化学反応に依存する。 | ソースから基板への材料の物理的移動(スパッタリングなど)を伴う。 |
温度 | 高温(しばしば500℃以上)が必要で、基材との適合性が制限される。 | 低温では、熱に弱い基板に適している。 |
フィルム純度 | 化学反応による潜在的不純物;腐食性副生成物が形成される可能性がある。 | 高純度膜;腐食性副生成物がない。 |
蒸着速度 | レートが高く、厚膜に適している。 | レートは低いが、高品質で均一なフィルムが得られる。 |
材料効率 | 副生成物やプリカーサーガスの浪費による効率の低下。 | 特にEBPVDのような技術では高効率。 |
用途 | 半導体製造、工具コーティング、光学/電子デバイス | マイクロエレクトロニクス、光学、装飾コーティング、感熱基板。 |
お客様のアプリケーションに適した成膜方法の選択にお困りですか? 今すぐ当社の専門家にお問い合わせください !