冷間静水圧プレス (CIP) の原理
ブレーズ・パスカルの圧力概念に基づくCIPの原理の理解
冷間静水圧プレス (CIP) は、ブレーズ パスカルによって提案された原理 (パスカルの法則として知られています) に基づいた材料の加工方法です。この原理によれば、密閉された流体内に加えられた圧力は、大きさを変えることなく流体全体の全方向に伝達されます。
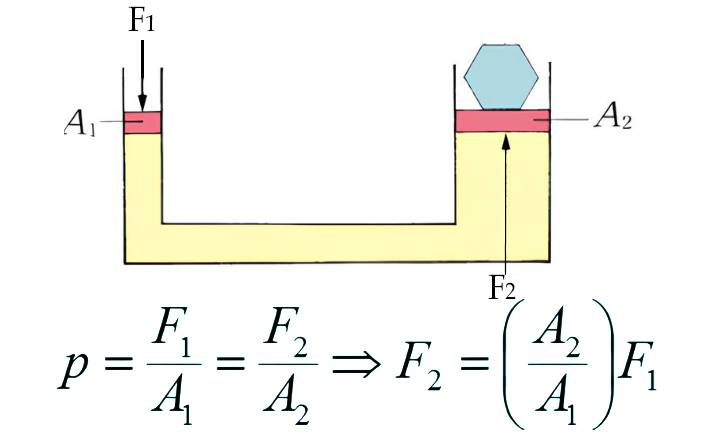
CIPでは、粉末を変形抵抗の低いエラストマー型に封入して圧縮します。次に、金型に均一な液体圧力がかかり、粉末が圧縮されます。これにより、非常に緻密な固体が形成されます。
CIP は、プラスチック、グラファイト、粉末冶金、セラミック、スパッタリング ターゲットなど、さまざまな材料の処理に使用できます。これは、粉末をさまざまなサイズや形状のコンポーネントに成形および圧縮する多用途の方法です。
粉末材料を成形型に封入し、液圧を加える工程
CIP加工では、粉末材料をゴム袋などの変形抵抗の低い成形型に封入します。次に、液体圧力が金型に均一に加えられ、粉末が圧縮されます。この液圧が金型全体に伝わり、成形体の表面全体が均一に圧縮されます。
CIP は室温で実行され、ウレタン、ゴム、ポリ塩化ビニルなどのエラストマー材料で作られた金型を使用します。 CIP で使用される流体は通常、油または水であり、操作中に適用される圧力は通常 60,000 lbs/in2 (400 MPa) から 150,000 lbs/in2 (1000 MPa) の範囲です。
CIP の利点は、歪みを軽減し、精度を向上させ、空気の巻き込みや空隙のリスクを最小限に抑えることができることです。医療、航空宇宙、自動車などのさまざまな業界で部品の製造に広く使用されています。
金型プレスはCIPと同様の方法です。金型と下パンチで囲まれた空間に粉末材料を充填する工程です。次に、上下のパンチ間の距離を狭めて圧縮します。
全体として、CIP は粉末材料を固体コンポーネントに成形および圧縮するための効果的な方法であり、高レベルの精度を提供し、欠陥のリスクを軽減します。
CIPと金型プレスの比較
金型プレス入門
金型プレスは、冷間静水圧プレス (CIP) に似た材料加工方法です。金型と下パンチで囲まれた空間に粉末材料を充填するプレス法です。次に、上下のパンチ間の距離を狭めて圧縮します。
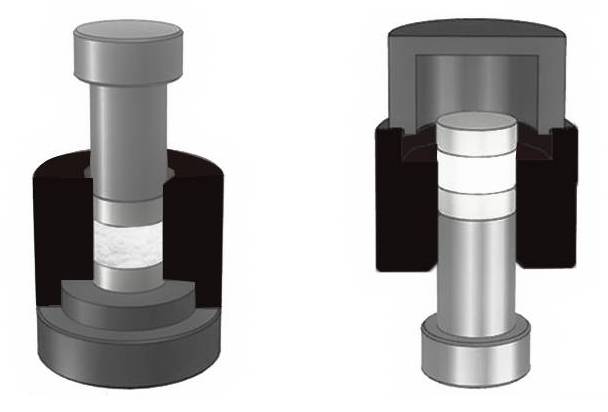
産業用金型プレス装置の自動化プロセス
産業現場で使用される金型プレス装置は、一連の自動化されたプロセスで構成されています。これらのプロセスには、粉末の充填、圧縮、成形体の取り出しが含まれます。単動プレスは下パンチを固定した状態で粉末を圧縮成形する一般的な方法です。
CIPと金型プレスの加圧工程の違い
CIP と金型プレスの主な違いは、使用する加圧プロセスにあります。 CIPは液圧を利用して材料に静水圧を加えるのに対し、金型プレスは一軸の圧力のみを加えます。この違いにより、密度分布の異なる製品が製造されます。
CIP成形品と金型プレス成形品の密度分布の比較
CIPは金型との摩擦がないため、均一な密度と均質性を備えた製品を製造します。一方、金型プレスでは密度分布にばらつきが生じる場合があります。金型プレスにより製造される成形体の下部は上部に比べて密度が低くなる傾向にあります。これは、粉末と金型やパンチとの間、および粉末粒子間の摩擦によるものです。
まとめると、CIP と金型プレスは両方ともさまざまな業界で使用されている材料加工方法です。粉末材料の使用や圧縮などの共通点はありますが、加圧プロセスとそれによる成形品の密度分布が異なります。 CIP は均一な密度と均質性を提供しますが、金型プレスでは密度にばらつきが生じる可能性があります。
CIP処理の種類
CIP成形法は大きく2種類に分類されます。粉末を充填する成形型と圧力を伝達する圧力媒体の関係により、湿式バッグ法と乾式バッグ法に分かれます。
ウェットバッグプロセス
ウェットバッグ法では、下図に示すように、粉末を成形型に充填し、高圧容器の外側で密閉してから圧力媒体に直接浸漬します。次に、金型の外面に静水圧を加えて、粉末を圧縮して所定の形状にします。複雑な形状や大型品の多品種少量生産や試作研究に適しています。
制限事項:
- サイクルタイム: 濡れたバッグの場合は 5 ~ 30 分
- 冷たい(室温)
- 均一な緑色濃度
- 一軸プレスより遅い
- ワックスレス、複雑な形状
- 部品には後加工が必要な場合があります
ドライバッグプロセス
ドライバッグプロセスでは、一度に 1 部品ずつ自動化され、粉末が成形型に充填され、高圧容器内に気密に密閉されます。次に、圧力媒体を圧力容器に導入し、金型の外面に静水圧を加えて粉末を圧縮して所定の形状にします。この方法は、さまざまな形状の部品をコスト効率よく製造するのに適しています。
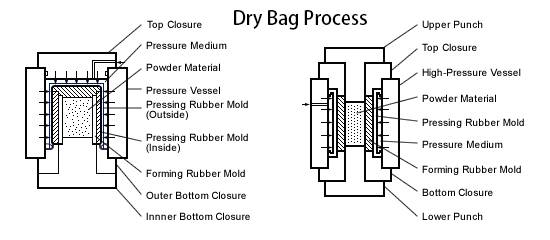
制限事項:
- サイクルタイム: 3 ~ 5 分
- 温かい(100℃)
- 焼結後を排除
- 高温(2200℃)
- 機械的および物理的特性を向上させます
- サイクル時間は遅くなる場合があります: 10 ~ 15 時間
- ニアネットシェイプ
- 全密度
ウェットバッグCIP
ウェットバッグとドライバッグという 2 種類の CIP 方法が長年にわたって進化してきました。混合形状の製造には、いわゆるウェットバッグ法が使用されます。現在、世界中で直径 50 ~ 2000 mm のサイズのウェットバッグ プレスが 3,000 台以上使用されていると推定されています。
CIPプロセスの応用例
ニアネットシェイプ処理テクノロジとして、CIP は通常、次のアプリケーションで使用されます。
- 材料が比較的高価であるため、ニアネットシェイププロセスを使用して廃棄物(例えば、加工屑の形で)を最小限に抑える用途では、経済的および環境的に大きな利点が得られます。
- 材料の機械加工が難しく、粉末加工によって部品を成形する方が現実的である用途。
- 部品の幾何学的複雑さにより高価な工具が必要な用途 (HIP の犠牲キャニスターなど)。 CIP は、比較的安価で再利用可能な (または使い捨て可能な) 柔軟なツールを利用し、複雑な形状の製造を可能にします。
- 特定の機械的性能を達成するために微細構造の均一性と均質性が必要とされる用途。粉末を静水圧的に処理すると、一軸プレスや鋳造などの他のプロセスに比べて相対的な利点が得られます。
- 複数の材料または段階的な構造が必要な用途。一部のアプリケーションでは従来の接合技術が適さないため、CIP はソリッドステート接合プロセスを提供します。
CIP プロセスは何年も前に開発されましたが、金属の商業用途は比較的限られていました。従来の用途は、パイプ、油圧継手、薄壁の容器ライナーなど、アスペクト比の高い管状または中実部品などのプリフォームや比較的単純な形状に焦点を当てていました。最近、CIP は、高価値セクターにわたる比較的高度なアプリケーションとして検討されています。たとえば、自動車用途には、コンロッド用の鍛造プリフォームや車両用カムフェーザー システムのアルミニウム部品が含まれます。航空宇宙用途には、蓄冷式推力室が含まれます。発電用途には、核分裂炉部品、原子炉の構造部品、将来の原子力システムの燃料被覆材や構造材料に使用される酸化物分散強化フェライト合金が含まれます。防衛用途には、ミサイル弾頭ケーシングが含まれます。 CIP+HIP は、スティンガー ミサイルの弾頭ケーシングを製造するために導入されました (生産量は 2000 万まで)。
市場の細分化
製品タイプに基づいて、冷間静水圧プレス (CIP) 装置市場は次のように分かれています。
- ウェットバッグプレス
ウェットバッグプロセスでは、粉末材料をフレックスモールドバッグに封入し、圧力容器内の高圧液体に浸漬します。次に、金型の外面に静水圧を加えて、粉末を圧縮して所定の形状にします。多形状、少量から大量生産、大型製品のプレス加工に最適な加工です。
CIP プロセスと HIP プロセスは両方とも、マルチマテリアル構造を使用します。CIP ではセラミック粉末を含むポリマーシェル、HIP ではハイエンド粉末冶金合金を使用した溶接軟鋼シート材料ケーシングです。したがって、どちらの方法も、複数材料の積層造形による構造の単一ステップの前処理の機会を提供します。このアプローチは、小規模なシリーズやプロトタイプを生産する場合に特に有益である可能性があり、より少ない処理ステップと時間で部品の複雑性を高めることができるため、製造コストも削減できる可能性があります。
ウェットバッグ工程の詳細
ウェットバッグ工程の説明
ウェットバッグ技術とは、粉末を型に充填し、密閉して成型する方法です。次に、金型を圧力容器内の圧力流体に浸します。等静圧が金型の外面に適用され、粉末が圧縮されて固体の塊になります。多形状、少量から大量生産に適した加工です。
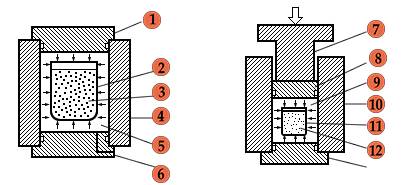
ウェットバッグプロセスはドライバッグプロセスほど一般的ではありませんが、依然として広く使用されています。現在、世界中で 3,000 台を超える湿式バッグ プレスが使用されており、そのサイズは直径 50 mm から 2,000 mm まであります。大容量ポンプと改良されたローディング機構により、完了までに通常 5 ~ 30 分かかるプロセスのスピードアップに役立ちます。
ウェットバッグプロセスの各種生産への適合性
ウェットバッグ法は、複雑な形状や大型の製品、試作研究など、さまざまな生産に適しています。他の方法では実現が難しい複雑な形状の製品の製造が可能になります。少量生産にも適しており、大量生産にも対応可能です。
ウェットバッグプロセスの構造タイプ:外部加圧式とピストン直圧式
ウェットバッグプロセスには外部加圧式とピストン直圧式の2つの構造タイプがあります。
外部加圧式は、圧力容器内に圧力媒体を外部から加圧する方式です。圧力媒体が金型の外部から適用され、内部の粉末が圧縮されます。
一方、ピストン直接加圧式は、高圧容器内に封入された圧力媒体を、トップクロージャの代わりにピストンを設置して直接加圧する方式です。このタイプのウェットバッグプロセスでは外部からの加圧が不要となり、効率が向上します。
全体として、ウェットバッグプロセスは粉末を成形するためのユニークな方法を提供し、さまざまな種類の生産に適しています。複雑な形状の製品も製作可能で、少量生産から量産まで対応可能です。ウェットバッグプロセスの 2 つの構造タイプにより、成形プロセスの柔軟性と効率が向上します。
ドライバッグ工程の詳細
ドライバッグ工程の説明
ドライバッグ法は、成形ゴム型に充填された粉末を高圧容器内の加圧ゴム型に圧力を伝えて成形する方法です。自動運転の省力化により、単純かつ多品種の製品を大量生産するのに適した方式です。
ドライバッグプロセスの量産適性
ドライバッグプレスは、圧力容器に柔軟な膜が作られており、すべてのプレスサイクル中に利用されるという点でウェットバッグとは異なります。この膜は圧力流体を金型から遮断し、「ドライバッグ」となります。このプロセスは、フレックスモールドが湿った粉末で汚染されないため、非常にクリーンです。さらに、容器の洗浄も少なくて済みます。この方法はサイクルが速く、粉末製品の自動大量生産に非常に理想的です。
ドライバッグプロセス方式の分類:周方向+軸方向加圧方式と周方向加圧方式
ドライバッグプロセスは、周方向+軸加圧方式と周方向加圧方式の2方式に分類されます。円周+軸加圧方式は圧力容器内に圧力媒体を外部から加圧する方式であり、円周加圧方式は高圧容器内に封入された圧力媒体を上部クロージャの代わりにピストンを設置して直接加圧する方式です。
ドライバッグ技術は材料の大量生産に最適です。このプロセスには通常わずか 1 分しかかからず、ウェットバッグ技術よりもはるかに高速です。
当社の製品にご興味がございましたら、当社の Web サイト ( https://kindle-tech.com/product-categories/isostatic-press ) をご覧ください。ここでは常にイノベーションが優先されています。当社の研究開発チームは、業界のトレンドを注意深くフォローし、常に可能性の限界を押し広げている経験豊富なエンジニアと科学者で構成されています。当社の実験装置には最新の技術が組み込まれており、実験中に正確で再現性のある結果が確実に得られます。高精度の機器からインテリジェントな制御システムに至るまで、当社の製品は実験作業に無限の可能性をもたらします。
無料相談はお問い合わせください
KINTEK LAB SOLUTION の製品とサービスは、世界中のお客様に認められています。弊社スタッフがどんなご質問にも喜んで対応させていただきます。無料相談にお問い合わせいただき、製品スペシャリストにご相談いただき、アプリケーションのニーズに最適なソリューションを見つけてください。