粉末冶金(PM)は、金属やセラミックスを含む幅広い材料から部品を製造できる汎用性の高い製造方法である。しかし、いくつかの要因から、主に小型部品の製造に限られている。最も大きな制限は、業界で使用されるプレス機の大きさで、一般的に1,500トン前後であるため、部品の平面積が約40~50平方インチに制限される。さらに、PMは複雑な形状を作ることができるが、鋳造や鍛造のような他の方法と比べると難易度が高い。さらに、PM部品は鋳造部品や鍛造部品の強度や延性に欠けることが多く、高い機械的性能を必要とする大型部品には不利になることがある。このような制約があるにもかかわらず、PMは、溶融、封じ込め、変形が困難な材料にとっては依然として有効な選択肢であり、深井戸掘削工具のような特定の用途に適しています。
キーポイントの説明
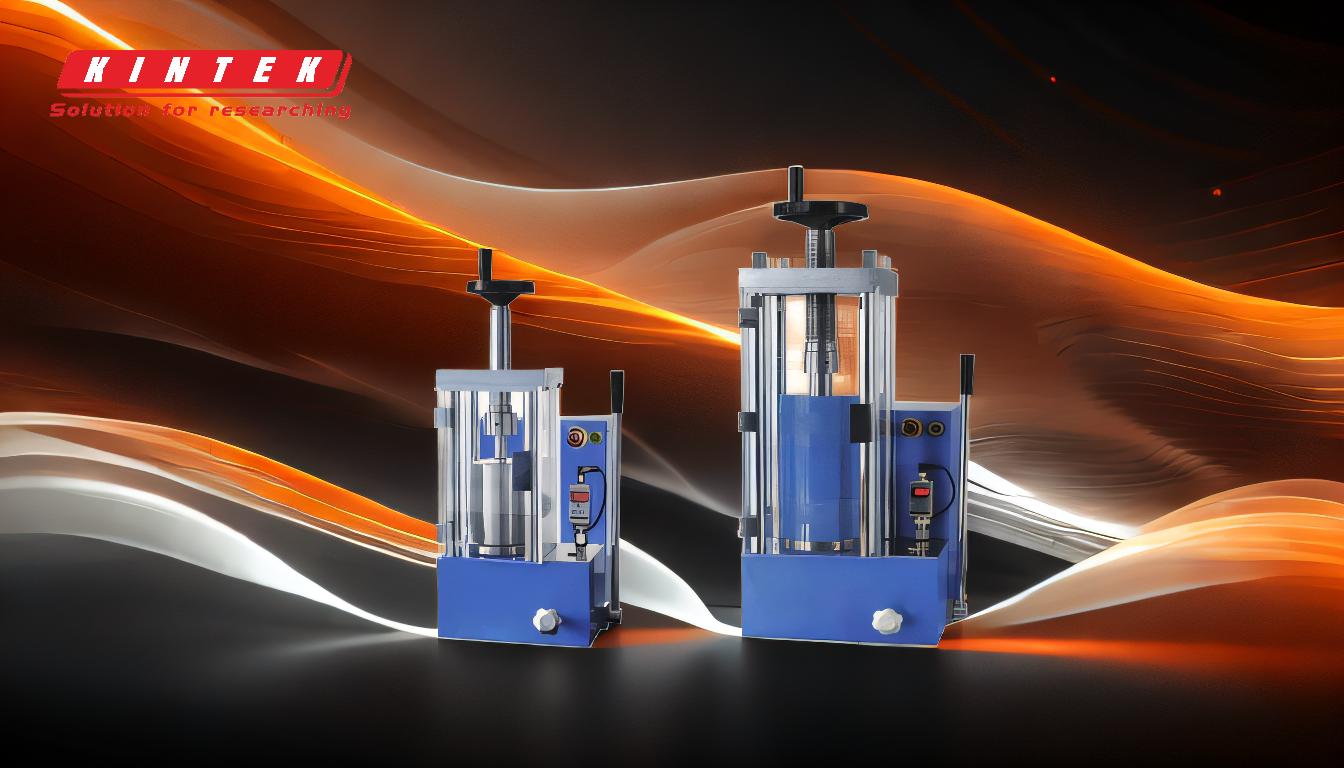
-
プレスサイズの制限:
- 粉末冶金で使用される最大のプレス機は約1,500トンで、実用的な部品サイズは平面面積で約40~50平方インチに制限される。
- この制約は、成形工程で均一な圧力分布が必要なためであり、部品が大きくなるとますます難しくなる。
- より大きな部品を生産するには、より大きなプレス機が必要ですが、そのような設備は業界では一般的ではありません。
-
複雑な形状への挑戦:
- 粉末冶金は複雑な形状を製造することができますが、鋳造や鍛造のような他の製造方法と比べると難易度が高くなります。
- 熟練した製造業者であれば、これらの課題を克服することも可能ですが、このプロセスでは本来、粉末の分布や成形を正確に制御する必要があり、複雑さやサイズが大きくなるほど難しくなります。
-
機械的特性:
- PM部品は一般的に、鋳造や鍛造で製造された部品と同レベルの強度と延性を達成することはできません。
- これは、粉末を圧縮して焼結するというPMプロセスの性質によるもので、潜在的な気孔や粒子間の結合の弱さにつながる。
- より高い機械的性能を必要とする大型部品では、このような制限があるため、PMは従来の方法と比較してあまり適していません。
-
材料の多様性:
- 粉末冶金は、その制限にもかかわらず、金属やセラミックスなど、加工できる材料の点で非常に汎用性が高い。
- このため、粉末冶金は、従来の方法では溶融、封入、変形が困難な材料にとって魅力的な選択肢となっている。
-
特殊な用途:
- 大きな部品には、金属粉末やセラミック粉末とバインダーの混合物を鋳型に充填する浸潤鋳造のような代替方法が使用される。
- この方法は、深井戸掘削用の多結晶ダイヤモンド複合材(PDC)ドリルビットの製造など、特殊な用途で採用されており、サイズの制約があるにもかかわらず、粉末冶金独自の利点が活用されている。
要約すると、大型部品の製造における粉末冶金の限界は、主にプレスサイズの制約、複雑な形状の課題、他の方法に比べて相対的に低い機械的特性によるものである。しかし、材料加工における汎用性と特殊用途への適性により、運用限界の範囲内では貴重な製造技術となっている。
総括表:
主な制限 | 説明 |
---|---|
プレスサイズの制約 | 最大プレスは1,500トンで、部品サイズは40~50平方インチに制限されます。 |
複雑な形状 | 鋳造や鍛造に比べて製造が難しい。 |
機械的特性 | 鋳造部品や鍛造部品よりも強度や延性が低い。 |
材料の多様性 | 金属やセラミックスの加工が可能で、溶融や変形が難しい材料に最適です。 |
特殊用途 | サイズの制限にもかかわらず、PDCビットのような深井戸掘削工具に使用されています。 |
粉末冶金がお客様の特殊なニーズにどのように対応できるかをご覧ください。 お問い合わせ !