真空焼入れは、金属加工品を硬化させるために真空環境で行われる特殊な熱処理プロセスです。真空ポンプを使用してチャンバー内の空気を除去することで、酸化と脱炭を排除し、変形を最小限に抑えた高品質の結果を保証します。このプロセスでは、ワークピースをゆっくりと加熱して熱応力を低減し、その後、オイルや不活性ガスなどの媒体を使用して急速に冷却します。真空焼き入れは、優れた機械的特性を持つ、明るくきれいな表面を作るのに理想的であり、航空宇宙や工具製造など、精度と耐久性が要求される産業に適しています。
キーポイントの説明
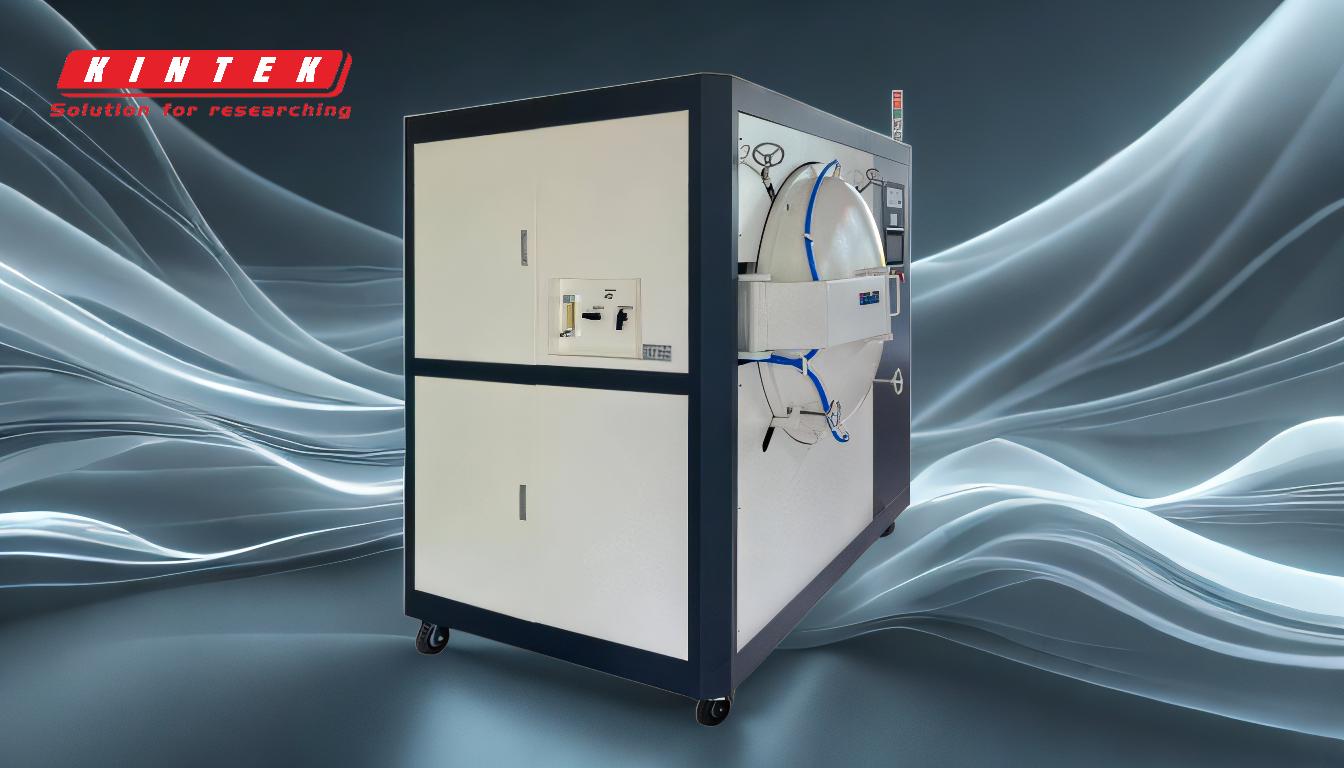
-
真空焼入れの定義とプロセス:
- 真空焼入れは、金属加工品を硬化させるために真空環境で行われる熱処理方法です。
- このプロセスでは、真空ポンプを使用して密閉されたチャンバーから空気を除去し、加熱および冷却中に酸化や汚染が起こらないようにします。
- この方法は、予測可能で高品質な結果を得るのに特に効果的です。
-
真空焼入れの利点:
- 表面品質:空気がないため、酸化や脱炭を防ぎ、明るくきれいな表面を実現。
- 最小限の変形:真空炉でゆっくりと加熱するため、内部の熱応力が減少し、変形が小さく高精度が得られます。
- 汎用性:長尺のロッド、シャフト、プレートなど、変形しやすい材料を含む幅広い材料に適しています。
-
真空焼入れにおける冷却方法:
- 真空オイル冷却:冷却媒体としてオイルを使用し、冷却速度が速く、組織が良好で表面酸化のないワークピースを製造します。
- 真空ガス焼入れ:冷却に高純度不活性ガス(Ar/He)または非反応性ガス(N2)を利用。この方法により、ワークの表面は平滑になり、焼入れ後の洗浄が不要になります。
-
用途と適性:
- 真空焼入れは、航空宇宙、工具製造、自動車など、高い精度と耐久性が要求される産業に最適です。
- 特に縦型真空ガス焼入れ炉は、大型ワークや複雑なワークに適しており、変形を最小限に抑え、処理後の輝度を維持します。
-
他の熱処理方法との比較:
- 従来の熱処理方法とは異なり、真空焼入れは表面汚染や酸化のリスクを排除します。
- 制御された環境でガス分圧を正確に管理できるため、浸炭や浸炭窒化のような高度な処理を低圧・高温で行うことができ、サイクルタイムが短縮されます。
-
真空熱処理の役割:
- 真空焼入れを含む真空熱処理は、優れた表面保護と機械的特性を保証します。
- このプロセスは、一貫した真空レベルを維持する真空ポンプシステムによって強化され、処理されたワークピースの品質と一貫性をさらに向上させます。
より広範なプロセスの詳細については、以下を参照してください。 真空熱処理 .
総括表:
アスペクト | 詳細 |
---|---|
定義 | 真空中で金属加工品を硬化させる熱処理。 |
主な利点 | 表面が明るく、変形が少ない。 |
冷却方法 | オイルまたは不活性ガスによる急速冷却。 |
用途 | 航空宇宙、工具製造、自動車 |
比較 | 従来の方法に比べ、酸化や汚染を排除。 |
真空焼き入れがいかに金属加工を向上させるかをご覧ください。 お問い合わせ までご連絡ください!