薄膜製造は、正確な厚さ、組成、特性を達成するために、基材上に材料の層を堆積させる高度なプロセスである。このプロセスは物理的、化学的、溶液ベースの方法に大別され、それぞれに物理蒸着法(PVD)、化学蒸着法(CVD)、スピンコート法などの技術があります。これらの方法は、希望するフィルム特性、アプリケーション要件、材料特性に基づいて選択されます。プロセスは、基板の準備から始まり、薄膜の蒸着が続き、最後に薄膜の特性を高めるための蒸着後の処理が行われる。
キーポイントの説明
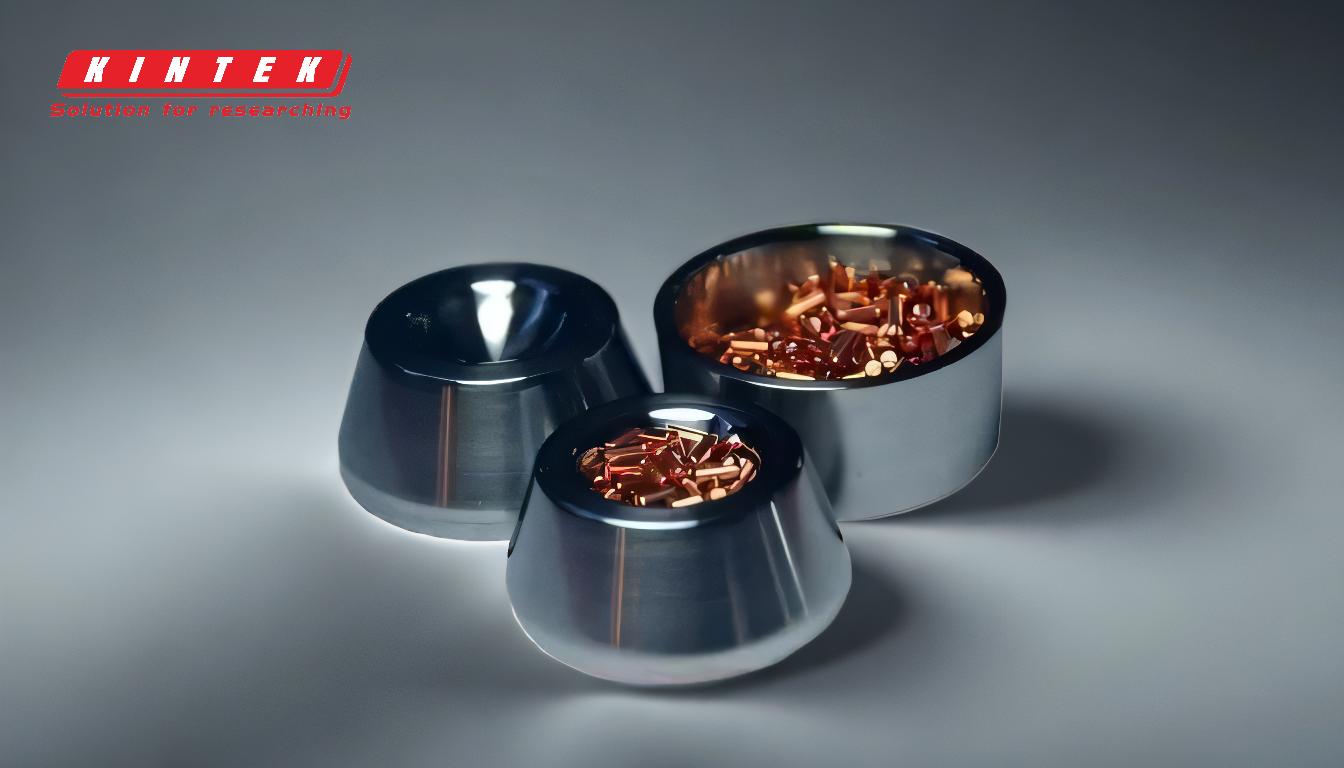
-
基材の準備
- クリーニング: 薄膜の密着性や品質に影響を与える可能性のある汚染物質を取り除くため、基板を徹底的に洗浄する必要がある。超音波洗浄、化学洗浄、プラズマ洗浄などの手法がある。
- 表面処理: 基板と薄膜の接着を向上させるために、エッチングや接着促進剤の塗布などの表面処理が必要な場合がある。
-
蒸着技術
-
物理蒸着 (PVD):
- 蒸発: 材料を真空中で気化するまで加熱し、基板上で凝縮させて薄膜を形成する。この方法は、融点が比較的低い材料に適している。
- スパッタリング: ターゲット材料にイオンをぶつけて原子を放出させ、基板上に堆積させる。この技術は汎用性が高く、さまざまな材料に使用できる。
-
化学蒸着法(CVD):
- 熱CVD: 基板を揮発性の前駆体にさらし、基板表面で反応または分解させて目的の薄膜を形成する。この方法は、高品質で均一な薄膜を成膜するために広く使われている。
- プラズマエンハンストCVD(PECVD): プラズマを使用して化学反応を促進し、熱CVDに比べて低温での成膜を可能にする。
-
溶液ベースの方法
- スピンコーティング: フィルム材料を含む溶液を基材に塗布し、高速で回転させて溶液を均一に広げ、溶媒を蒸発させて薄いフィルムを残す。
- ディップコーティング: 基板を溶液に浸し、溶媒が蒸発するにつれて薄膜が形成されるように、制御された速度で引き上げる。
- レイヤー・バイ・レイヤー(LbL)アセンブリ: 複雑な多層構造を作成するために、多くの場合ディップコーティングまたはスピンコーティングによって、異なる材料の層を交互に基板上に堆積させる。
-
物理蒸着 (PVD):
-
成膜後の処理
- アニール: 薄膜を特定の温度に加熱し、結晶性を高め、欠陥を減らし、機械的・電気的特性を向上させる。
- 表面改質: プラズマ処理や化学的官能基化などの技術を使用して、特定の用途向けに薄膜の表面特性を変えることができる。
- 特性評価: 薄膜は、様々な技術(X線回折、電子顕微鏡、分光法など)を用いて分析され、厚さ、組成、特性などの点で希望する仕様に適合していることが確認される。
-
応用と考察
- 半導体: 薄膜は、半導体デバイスの製造において非常に重要であり、厚さと組成の精密な制御が性能に不可欠である。
- 光学コーティング: 薄膜は、透明性や反射率などの光学特性が重要な反射防止コーティング、ミラー、フィルターの作成に使用される。
- フレキシブル・エレクトロニクス: ポリマーなどの薄膜は、フレキシブル太陽電池やOLEDなど、柔軟性と軽量性が求められるデバイスに使用されている。
- バリア層: 薄膜は、水分、酸素、紫外線などの環境要因から基板を保護するバリア層として機能する。
結論として、薄膜作製プロセスは複雑で高度に制御された手順であり、基板の準備から成膜後の処理まで、複数の工程を含む。成膜技術の選択は、材料、所望の膜特性、用途によって異なる。それぞれの方法には利点と限界があり、望ましい結果を得るためにはプロセスを慎重に最適化する必要がある。
要約表
ステップ | 詳細 |
---|---|
基板準備 | 洗浄(超音波、化学、プラズマ)および表面処理(エッチング、接着促進剤)。 |
成膜技術 | PVD(蒸着、スパッタリング)、CVD(熱、PECVD)、溶液ベース(スピンコーティング、ディップコーティング、LbL)。 |
ポストデポジション | アニーリング、表面改質、特性評価(XRD、顕微鏡、分光法)。 |
応用分野 | 半導体、光学コーティング、フレキシブルエレクトロニクス、バリア層 |
薄膜プロセスの最適化にご興味がおありですか? 当社の専門家に今すぐご連絡ください までご連絡ください!