抵抗炉と誘導炉はどちらも材料の加熱に使用されますが、根本的に異なる原理で動作します。抵抗炉は電気抵抗を利用して熱を発生させ、その熱は伝導、対流、または放射によって材料に伝達されます。一方、誘導炉は電磁誘導を利用して材料自体の内部で直接熱を発生させます。この重要な違いは、効率、加熱速度、制御、およびアプリケーションの変化につながります。一般に、抵抗炉は定常状態の加熱においてよりシンプルでコスト効率が高く、誘導炉はより高速な加熱、優れたエネルギー効率、正確な温度制御を提供するため、急速または局所的な加熱が必要な用途に最適です。
重要なポイントの説明:
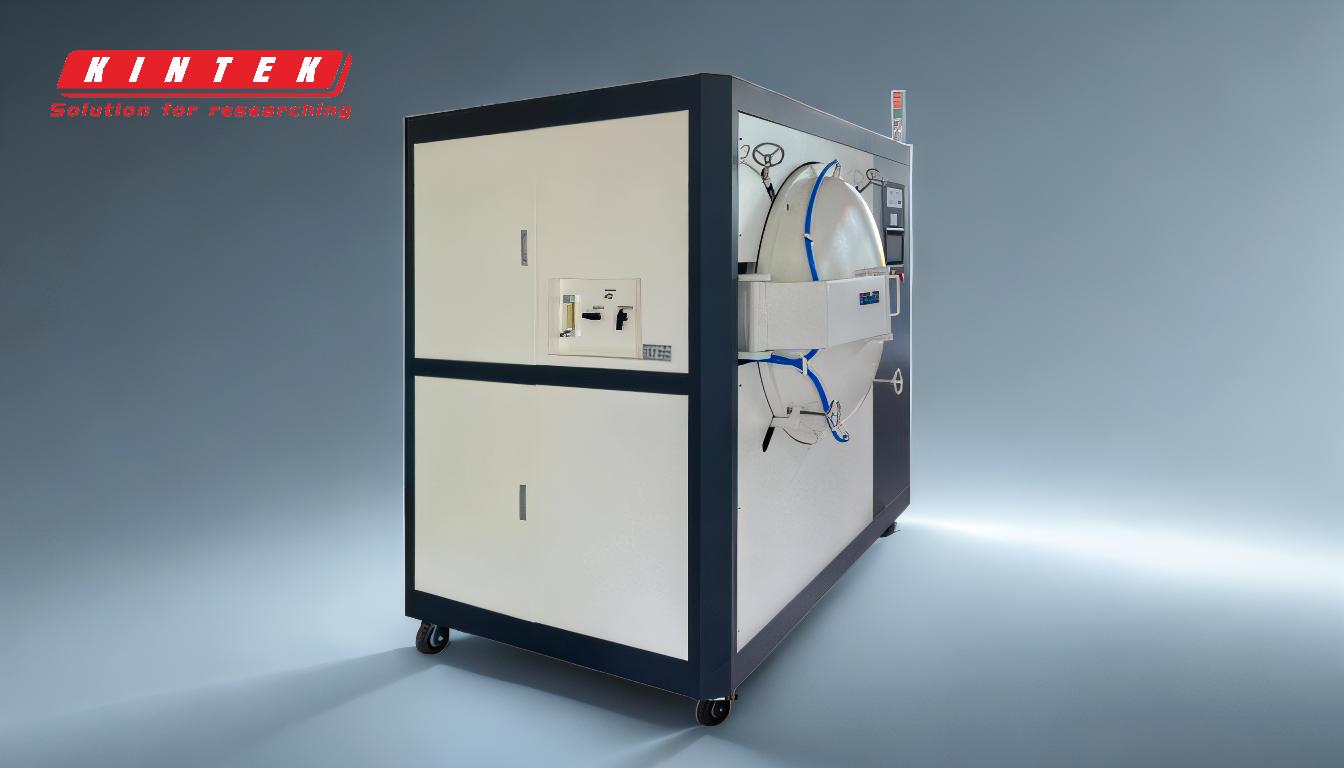
-
加熱機構:
- 抵抗炉 :コイルや電熱線などの抵抗体に電流を流すことで熱が発生します。次に、熱は伝導、対流、または放射によって材料に伝達されます。この方法は、材料が外部源によって加熱されるため、間接的です。
- 誘導炉 :電磁誘導を利用して素材内で直接熱を発生させます。交流電流がコイルを通過すると、材料内に渦電流を誘導する磁場が発生し、材料が加熱されます。この方法は直接的で非常に効率的です。
-
エネルギー効率:
- 抵抗炉: 熱が外部で発生し、材料に伝達されるため、エネルギー損失が発生するため、誘導炉と比較してエネルギー効率が低くなります。
- 誘導炉: 熱が材料内で直接生成されるため、エネルギー効率が高く、エネルギー損失を最小限に抑えます。これは、高温用途で特に有益です。
-
加熱速度と制御:
- 抵抗炉: 加熱速度が遅くなり、温度制御の精度が低くなります。定常状態の加熱が必要な用途に適しています。
- 誘導炉: より速い加熱速度と正確な温度制御により、急速または局所的な加熱が必要なプロセスに最適です。の使用 IGBT誘導炉 テクノロジーにより、制御と効率がさらに向上します。
-
アプリケーション:
- 抵抗炉 :広い面積にわたって均一な加熱が必要な、アニーリング、焼き戻し、乾燥などの用途で一般的に使用されます。
- 誘導炉: 溶解、鍛造、表面硬化など、急速、局所的、または高温の加熱が必要な用途に使用されます。
-
コストと複雑さ:
- 抵抗炉: 基本的な加熱用途では、一般に設計がシンプルで、コスト効率が高くなります。メンテナンスは簡単です。
- 誘導炉 :誘導コイルや電源などの高度なコンポーネントが必要なため、より複雑で高価になります。ただし、初期コストが高くても、多くの場合、エネルギーの節約とパフォーマンスの向上によって相殺されます。
-
材質の適合性:
- 抵抗炉 :金属、セラミックス、ガラスなど幅広い材質に対応可能です。ただし、急速または局所的な加熱が必要な材料には適さない場合があります。
- 誘導炉 :主に金属などの導電性材料に使用されます。非導電性材料は誘導を使用して加熱できません。
-
環境への影響:
- 抵抗炉: エネルギー消費量と熱損失が増えると、環境フットプリントが大きくなる可能性があります。
- 誘導炉: エネルギー消費量の削減と熱損失の削減により、より環境に優しいオプションになります。
これらの主な違いを理解することで、購入者は特定の加熱要件、材料の種類、運用目標に基づいて情報に基づいた意思決定を行うことができます。
概要表:
側面 | 抵抗炉 | 誘導炉 |
---|---|---|
加熱機構 | 電気抵抗(伝導、対流、または放射)による間接加熱。 | 電磁誘導による材料内部の直接加熱。 |
エネルギー効率 | 外部からの発熱と伝達損失により効率が低下します。 | 熱が材料内で直接生成されるため、より効率的です。 |
加熱速度・制御 | 加熱が遅くなり、制御の精度が低下します。定常状態の加熱に最適です。 | より速い加熱、正確な制御。急速または局所的な加熱に最適です。 |
アプリケーション | アニーリング、焼き戻し、乾燥(広範囲にわたる均一な加熱)。 | 溶解、鍛造、表面硬化(急速または局所加熱)。 |
コストと複雑さ | シンプルな設計で、基本的な暖房の費用対効果が高くなります。簡単なメンテナンス。 | より複雑で初期コストが高くなります。エネルギーの節約とパフォーマンスの向上によって相殺されます。 |
材質の適合性 | 広範囲(金属、セラミックス、ガラス)。急速/局所的な加熱には理想的ではありません。 | 主に導電性材料(金属)。非導電性材料は加熱できません。 |
環境への影響 | エネルギー消費量と熱損失が増加します。より大きな環境フットプリント。 | エネルギー消費量の削減、熱損失の削減。より環境に優しい。 |
用途に適した炉の選択にサポートが必要ですか? 今すぐ専門家にお問い合わせください 個別のアドバイスが必要です!