PVD (物理蒸着) と PECVD (プラズマ化学蒸着) は、半導体製造、光学、コーティングなどのさまざまな業界で使用される 2 つの異なる薄膜蒸着技術です。 PVD は材料を堆積するためにスパッタリングや蒸着などの物理プロセスに依存しますが、PECVD はプラズマを使用して従来の CVD と比較して低温での化学反応を強化します。主な違いは、堆積メカニズム、温度要件、堆積材料の状態 (PVD では固体、PECVD では気体) にあります。 PVD は一般に安全で有毒化学物質を回避しますが、PECVD には低温堆積やエネルギー効率などの利点があります。
重要なポイントの説明:
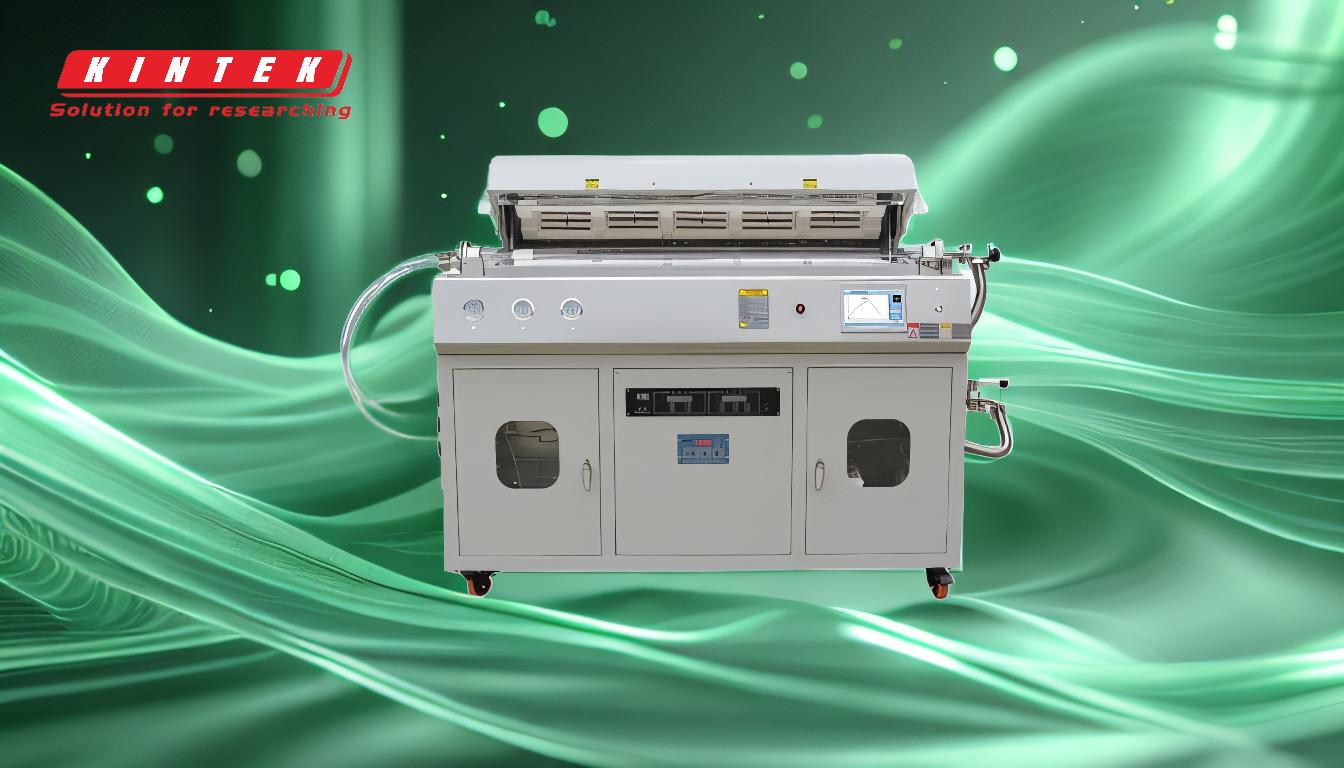
-
成膜の仕組み:
- PVD: PVD では、堆積される材料は固体状態から始まります。その後、スパッタリングや熱蒸発などの物理的プロセスを通じて蒸気に変換されます。蒸気は基板上で凝縮して薄膜を形成します。一般的な PVD 法には、スパッタリング、真空蒸着、電子ビーム蒸着などがあります。たとえば、スパッタリングでは、高電圧プラズマを使用してターゲット材料から原子を除去し、その原子を基板上に堆積させます。
- PECVD: PECVD には、プラズマによって促進される気相での化学反応が含まれます。プラズマは化学反応に必要な活性化エネルギーを提供し、従来の CVD と比較してより低い温度での堆積を可能にします。このため、PECVD は温度に敏感な基板に適しています。
-
物質の状態:
- PVD: PVD で堆積された材料は、最初は固体状態です。たとえば、熱蒸着では、材料が蒸発して基板上に凝縮するまで加熱されます。
- PECVD: PECVD では、材料はガス状で導入されます。プラズマは化学反応を促進し、その結果基板上に固体膜が堆積されます。
-
温度要件:
- PVD: PVD プロセスでは通常、基板自体を加熱する必要がないため、高温に敏感な材料には有利です。
- PECVD: PECVD は、その低温堆積能力で知られています。プラズマの高エネルギー電子は必要な活性化エネルギーを提供し、従来の CVD に必要な温度よりもはるかに低い温度での堆積を可能にします。
-
安全性と環境への影響:
- PVD: PVD プロセスは有毒な化学物質を含まないため、一般に安全です。化学反応がないため、有害な副産物が発生するリスクが軽減されます。
- PECVD: PECVD は効率的で低温処理が可能ですが、反応性ガスの使用が含まれる場合があり、安全性と環境上の懸念が生じる可能性があります。
-
用途とメリット:
- PVD: PVD は、高純度および密着性が必要な用途で金属および合金を蒸着するために広く使用されています。簡単さと安全性でも好評です。
- PECVD: PECVD は、窒化シリコンや二酸化シリコンなどの誘電体膜を低温で堆積するのに有利です。これは、温度に敏感な基板上に薄膜を作成するために半導体産業で特に役立ちます。
-
プロセスの複雑さ:
- PVD: PVD プロセスは比較的単純で、必要な手順が少なく、装置もシンプルです。たとえば、真空蒸着では、材料が蒸発して基板上に凝縮するまで真空チャンバー内で材料を加熱します。
- PECVD: PECVD プロセスは、プラズマの生成と制御が必要なため、より複雑になります。均一な堆積を保証し、基板への損傷を避けるために、プラズマは注意深く管理する必要があります。
要約すると、PVD と PECVD は、堆積メカニズム、材料の状態、温度要件、安全性の考慮事項が根本的に異なります。 PVD は物理プロセスと固体材料の堆積を特徴とし、PECVD はガス状材料の低温堆積にプラズマ増強化学反応を利用します。各方法には独自の利点があり、アプリケーションの特定の要件に基づいて選択されます。
概要表:
側面 | PVD | PECVD |
---|---|---|
成膜の仕組み | 物理プロセス (スパッタリング、蒸着など) | プラズマ増強化学反応 |
物質の状態 | 固体として開始し、蒸気として堆積 | ガスとして導入され、固体膜として堆積 |
温度 | 基板加熱が不要 | プラズマによる低温成膜が可能 |
安全性 | より安全で有害な化学物質を回避 | 反応性ガスが含まれる可能性があり、安全上の懸念が生じる |
アプリケーション | 金属、合金、高純度コーティング | 誘電体膜、半導体産業 |
プロセスの複雑さ | よりシンプルに、より少ない手順で | より複雑で、プラズマの生成と制御が必要 |
アプリケーションに PVD と PECVD のどちらを選択するかについてサポートが必要ですか? 今すぐ専門家にお問い合わせください カスタマイズされたアドバイスを提供します!