PECVD(Plasma-Enhanced Chemical Vapor Deposition)とスパッタリングは、どちらも薄膜形成技術であるが、そのメカニズム、材料、用途が大きく異なる。PECVDは、プラズマによって活性化される気相前駆体を使い、低温で薄膜を成膜するため、デリケートな基板やアモルファス膜の製造に適している。物理蒸着(PVD)の一種であるスパッタリングは、固体のターゲット材料にイオンをぶつけて原子を放出させ、基板上に堆積させる。この方法は、高度に均一で高密度の膜を作るのに理想的で、光学や電気用途によく使われる。PECVDとスパッタリングのどちらを選択するかは、成膜速度、温度感度、所望の膜特性などの要因によって決まる。
キーポイントの説明
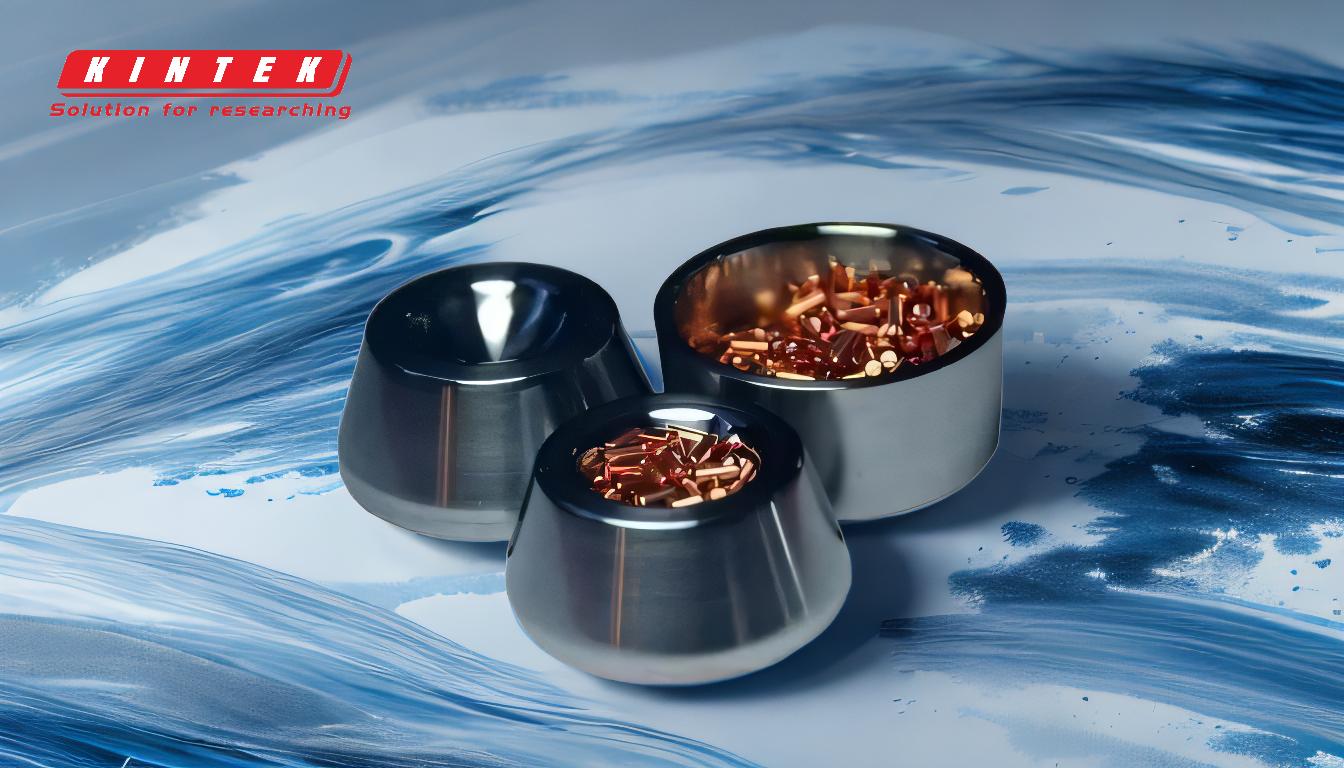
-
成膜のメカニズム:
- PECVD:プラズマによって解離・活性化される気相前駆体を利用する。プラズマは化学反応に必要なエネルギーを供給し、低温(室温~350℃)での成膜を可能にする。このプロセスは非選択的であるため、独特の非平衡相成分が形成され、通常アモルファス膜となる。
- スパッタリング:固体ターゲット材料に高エネルギーのイオンを照射して原子を放出させ、基板上に堆積させるPVD技術。この方法は化学反応に頼らず、むしろ材料の物理的な放出と堆積に依存する。
-
温度条件:
- PECVD:従来のCVD(600℃~800℃)に比べて大幅に低い温度で動作する。このため、PECVDは温度に敏感な基板に適しており、熱応力を低減することで、より強固な接合が可能になります。
- スパッタリング:素材や用途にもよるが、一般的に高温を必要とする。しかし、特定の用途ではより低い温度にも適応できる。
-
蒸着率:
- PECVD:従来のPVD技術に比べ、高い成膜速度(1~10 nm/s以上)を実現。これにより、PECVDは大規模生産においてより効率的で費用対効果が高くなります。
- スパッタリング:一般的にPECVDに比べ成膜レートは低いが、高均一で緻密な膜が得られ、正確な膜厚と品質が要求される用途には欠かせない。
-
膜特性:
- PECVD:ユニークな非平衡相成分を持つアモルファス膜を生成する。膜の密度は低いことが多いが、均一性に優れ、幅広い基板に適している。
- スパッタリング:非常に均一で緻密な結晶膜を形成する。この技術は、光学コーティングや電気接点など、高い精度と耐久性が要求される用途に最適です。
-
応用例:
- PECVD:半導体産業、太陽電池製造、温度に敏感な材料への保護膜蒸着によく使用される。低温で高い成膜速度が得られるため、さまざまな用途に使用できる。
- スパッタリング:光学コーティング、電気接点、薄膜トランジスタの製造に広く使用されている。また、膜特性の精密な制御が不可欠なソーラーパネルやOLEDの製造にも採用されている。
-
利点と限界:
-
PECVD:
- 利点 :高い成膜速度、低温動作、幅広い基板への適合、ユニークな膜特性を生み出す能力。
- 制限事項 :スパッタリング膜に比べ、膜の密度が低く、欠陥が発生しやすい。
-
スパッタリング:
- 利点 :非常に均一で緻密なフィルムが得られ、精密な用途に優れ、様々な材料に適応できる。
- 制限事項 :一般にPECVDに比べて成膜レートが低く、装置コストが高い。
-
PECVD:
まとめると、PECVDとスパッタリングは、成膜メカニズム、必要温度、得られる膜特性において異なる。PECVDは、アモルファス膜の低温・高速成膜を得意とし、スパッタリングは、緻密で均一な膜を精密な制御で形成するのに適している。これらの技術間の選択は、基板感度、所望の膜特性、生産効率など、用途の具体的な要件によって決まる。
総括表:
側面 | PECVD | スパッタリング |
---|---|---|
メカニズム | プラズマによって活性化された気相前駆体 | 固体ターゲットからの原子の物理的放出 |
温度 | 低い(室温~350) | 高いが、より低い温度にも適応可能 |
蒸着速度 | 高い(1~10nm/s以上) | 低いが、均一性の高いフィルムが得られる |
フィルム特性 | 非晶質、密度が低い、均一性良好 | 緻密、均一、しばしば結晶性 |
用途 | 半導体、太陽電池、保護膜 | 光学コーティング、電気接点、薄膜トランジスタ |
利点 | 高成膜速度、低温動作、汎用性 | 緻密で均一な成膜、精密な制御 |
制限事項 | 膜の密度が低く、欠陥が発生しやすい。 | 成膜速度の低下、装置コストの上昇 |
適切な薄膜形成技術の選択にお困りですか? 当社の専門家に今すぐご連絡ください オーダーメイドのソリューションを