蒸発とスパッタリングは、どちらも基板上に薄膜を形成するために用いられる物理的気相成長(PVD)技術であるが、そのメカニズム、操作条件、用途において根本的に異なる。蒸着は材料が気化するまで加熱するのに対し、スパッタリングは高エネルギーイオンを使ってターゲット材料から原子を叩き落とす。これらの違いにより、成膜速度、膜質、拡張性、特定用途への適合性にばらつきが生じる。以下では、これらの違いについて詳しく説明する。
要点の説明
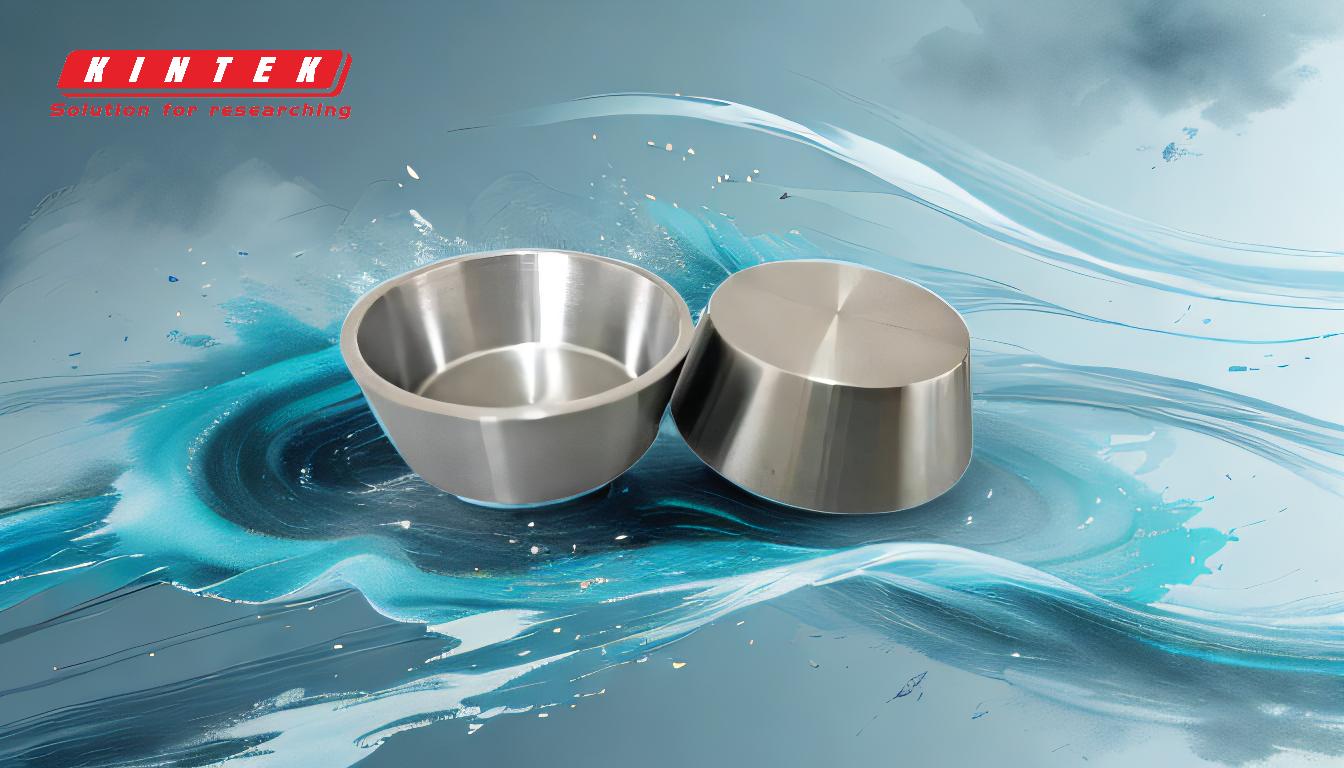
-
材料蒸発のメカニズム:
-
蒸発:
- 熱エネルギー(抵抗加熱や電子ビームなど)を使用して、ソース材料を気化温度に達するまで加熱する。
- 強固な蒸気ストリームを生成し、より高い蒸着速度を可能にする。
- 高真空環境で動作し、気相衝突を最小限に抑えます。
-
スパッタリング:
- プラズマ環境下で高エネルギーイオン(通常はアルゴン)をターゲット材料に照射する。
- ターゲット材料から単原子または小さなクラスターを放出する。
- 高いガス圧(5~15 mTorr)で作動し、スパッタ粒子は基板に到達する前に気相衝突を受ける。
-
蒸発:
-
蒸着速度と効率:
-
蒸着:
- 一般的に、スパッタリングと比較して成膜速度が高く、特に高温材料に適している。
- 蒸気流が強固なため、運転時間が短い。
-
スパッタリング:
- 純金属を除き、一般に成膜速度が低い。
- プロセスは遅いが、拡張性と自動化の可能性が高い。
-
蒸着:
-
フィルムの品質と特性
-
蒸発:
- 粒径が大きく、均質性の低い膜ができる。
- 蒸着種のエネルギーが低いため、基板への密着性が低い。
- 高真空中で動作するため、膜中の吸収ガスが少ない。
-
スパッタリング:
- 粒径が小さく、均質性の高い膜が得られる。
- スパッタ粒子のエネルギーが高いため、密着性が高い。
- より高いガス圧で作動するため、膜中の吸収ガスがより多い。
-
蒸発:
-
運転条件
-
蒸発:
- 気相衝突を最小限に抑えるため、高真空環境が必要。
- 基板が直接蒸気の流れにさらされている必要がある。
-
スパッタリング:
- より低い真空レベル(より高いガス圧)で作動する。
- 気相衝突による成膜の方向性が少なく、複雑な形状の成膜が可能。
-
蒸発:
-
材料の多様性
-
蒸発:
- 分解せずに高温に耐える材料に適する。
- 複数の材料を共蒸発させて合金を作ることができる。
-
スパッタリング:
- 融点の高い材料や加熱により分解する材料など、より幅広い材料を成膜できる。
- コーターの構成により連続成膜が可能。
-
蒸発:
-
アプリケーション
-
蒸着:
- 光学コーティングや一部の半導体用途など、高い蒸着速度とシンプルな形状を必要とする用途に最適。
-
スパッタリング:
- マイクロエレクトロニクス、装飾コーティング、耐摩耗性コーティングなど、高い膜質、密着性、複雑な形状の被覆を必要とする用途に適している。
-
蒸着:
-
拡張性と自動化:
-
蒸着:
- 高真空条件と視線蒸着が必要なため、拡張性が低い。
-
スパッタリング:
- 拡張性が高く、大量生産の自動化が可能なため、工業用途に適している。
-
蒸着:
まとめると、蒸着とスパッタリングはどちらも効果的なPVD技術であるが、そのメカニズム、操作条件、得られる膜特性から、それぞれ異なる用途に適している。蒸着は高い成膜速度と簡便性に優れ、スパッタリングは膜質、密着性、拡張性に優れている。これらの違いを理解することは、特定の薄膜蒸着ニーズに適した技術を選択する上で極めて重要である。
要約表
側面 | 蒸着 | スパッタリング |
---|---|---|
メカニズム | 熱エネルギーが物質を加熱して気化させる。 | 高エネルギーのイオンがターゲット材料から原子を叩き落とす。 |
蒸着速度 | 特に高温材料では高い。 | 純金属以外は低い。 |
フィルム品質 | 粒径が大きく、均質性が低く、密着性が低い。 | 粒径が小さいほど均質性が高く、密着性が向上する。 |
操作条件 | 高真空、見通し蒸着。 | 低真空、指向性の低い蒸着。 |
材料の多様性 | 耐高温素材に限定。 | 高融点材料を含む広い範囲。 |
用途 | 光学コーティング、シンプルな形状 | マイクロエレクトロニクス、複雑な形状、耐摩耗性コーティング。 |
拡張性 | 高真空と見通しが必要なため、拡張性は低い。 | 工業用には高い拡張性と自動化が可能。 |
お客様の用途に適したPVD技術の選択にお困りですか? 今すぐ専門家にお問い合わせください !