スパッタリングと蒸着は、基板上に薄膜を成膜するために使用される2つの主要な物理蒸着(PVD)技術である。スパッタリングでは、プラズマ環境下で高エネルギーのイオンをターゲット材料に照射し、原子を基板上に放出・堆積させる。この方法は、高純度、精密な制御、優れた密着性を提供する。対照的に、蒸発法は熱エネルギーを使って原料を蒸発させ、それが基板上に凝縮する。蒸発法はシンプルで蒸着速度が速い反面、スパッタリングのような均一性や材料の多様性に欠けることが多い。どちらの方法にも明確な利点と限界があり、エレクトロニクス、光学、コーティングなどの産業におけるさまざまな用途に適している。
キーポイントの説明
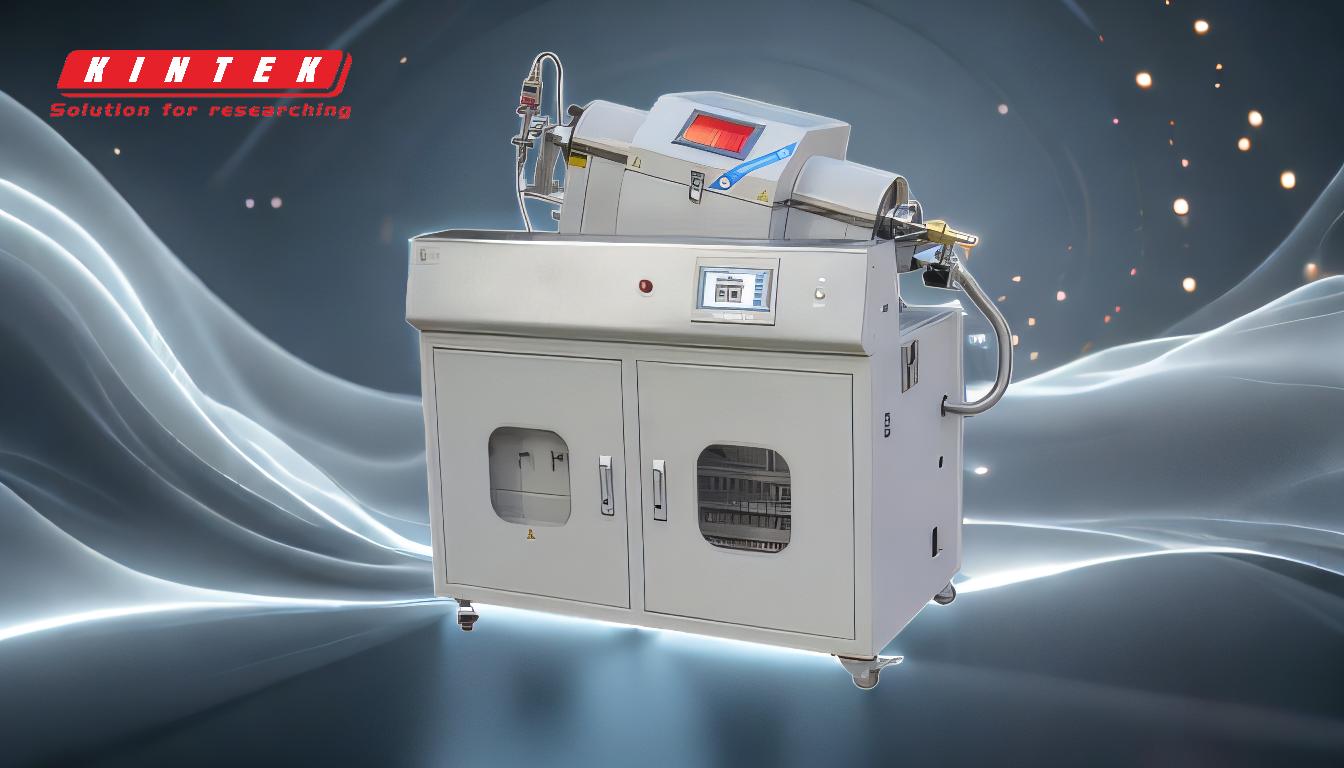
-
成膜のメカニズム:
- スパッタリング:高エネルギーイオンがターゲット材料に衝突して原子を放出し、その原子が基板上に堆積するプラズマ環境で起こる。このプロセスは高度に制御されており、原子レベルでの精密な薄膜蒸着が可能である。
- 蒸着:熱エネルギーを利用して原料を蒸発させ、基板上に凝縮させる。この方法はスパッタリングに比べ単純だが、精度は劣る。
-
成膜環境:
- スパッタリング:高温と運動エネルギーを特徴とし、「自然の第4の状態」とも呼ばれるプラズマ環境で行われます。その結果、より純粋で精密な薄膜が得られる。
- 蒸発:従来の加熱方法を利用するため、複雑ではないが、同レベルの純度と精度を達成する能力も低い。
-
材料の互換性と多様性:
- スパッタリング:材料適合性の面で汎用性が高く、金属、合金、化合物など幅広い材料を蒸着できる。また、変調により色の多様性を高めることができる。
- 蒸発:幅広い材料に適しているが、単純な用途に限定されることが多く、希望する色を実現するにはスプレー塗装などの追加工程が必要になるのが一般的である。
-
蒸着速度と均一性:
- スパッタリング:一般的に蒸着法は、純金属を除いて蒸着法よりも蒸着率が低い。しかし、膜の均一性が高く、粒径が小さいため、より均一で高品質な膜が得られる。
- 蒸発:マスクやプラネタリーシステムと併用することで、高い成膜速度と優れた均一性が得られる。しかし、これらの補助剤がないと均一性が悪くなることがある。
-
接着性とフィルムの質:
- スパッタリング:密着性に優れ、蒸着種のエネルギーが高く、優れた膜質と耐久性を実現。
- 蒸着:フィルムは密着性が低い傾向があり、吸収ガスなどの問題が発生しやすく、フィルムの品質に影響を与える可能性がある。
-
システムの複雑さとコスト:
- スパッタリング:プラズマ環境と精密な制御機構が必要なため、より複雑で高価。
- 蒸発:よりシンプルで安価なため、基本的な用途には利用しやすいが、高度で高精度な作業には不向き。
-
アプリケーション:
- スパッタリング:高精度、高純度、高耐久性が要求される用途に最適。
- 蒸発:精密さや膜質よりも、高い蒸着速度とコスト効率を優先する、よりシンプルな用途に適している。
これらの重要な違いを理解することで、装置や消耗品の購入者は、アプリケーションの特定の要件に基づいて情報に基づいた決定を下すことができ、最適な性能とコスト効率を確保することができます。
要約表
側面 | スパッタリング | 蒸着 |
---|---|---|
メカニズム | 高エネルギーイオンがプラズマ環境でターゲットに衝突。 | 熱エネルギーはソース材料を蒸発させる。 |
蒸着環境 | プラズマ環境(高純度、精密制御)。 | 従来の加熱(よりシンプル、精度が低い)。 |
材料の多様性 | 金属、合金、コンパウンドに適合。 | 限定的;より単純な用途に適する。 |
蒸着率 | 純金属以外は低い。 | 蒸着率が高い。 |
均一性 | フィルムの均一性が良く、粒径が小さい。 | マスクやプラネタリーシステムとの相性が良い。 |
接着性と品質 | 優れた接着性とフィルム品質。 | 粘着力が低く、吸収ガスの問題が発生しやすい。 |
システムの複雑さ | より複雑で高価。 | よりシンプルで費用対効果が高い。 |
用途 | エレクトロニクス、光学(高精度、高純度、耐久性)。 | よりシンプルなアプリケーション(高い成膜速度、費用対効果)。 |
お客様のアプリケーションに適したPVD技術の選択にお困りですか? 今すぐ専門家にお問い合わせください !