熱蒸着とスパッタリングは、基板上に薄膜を形成するために広く使われている2つの物理蒸着(PVD)技術である。熱蒸発法では、高真空チャンバー内で固体材料を蒸発するまで加熱し、蒸気流を形成して基板上に堆積させます。この方法はシンプルで、融点の低い材料に効果的であるため、OLEDや薄膜トランジスタのような用途に最適である。一方、スパッタリングは、ターゲット材料に高エネルギーの粒子をぶつけて原子やクラスターを放出させ、基板上に堆積させる。この技術は汎用性が高く、金属、セラミック、プラスチックなど幅広い材料に適している。どちらの手法も、精密で高品質な薄膜コーティングを必要とする産業には欠かせない。
キーポイントの説明
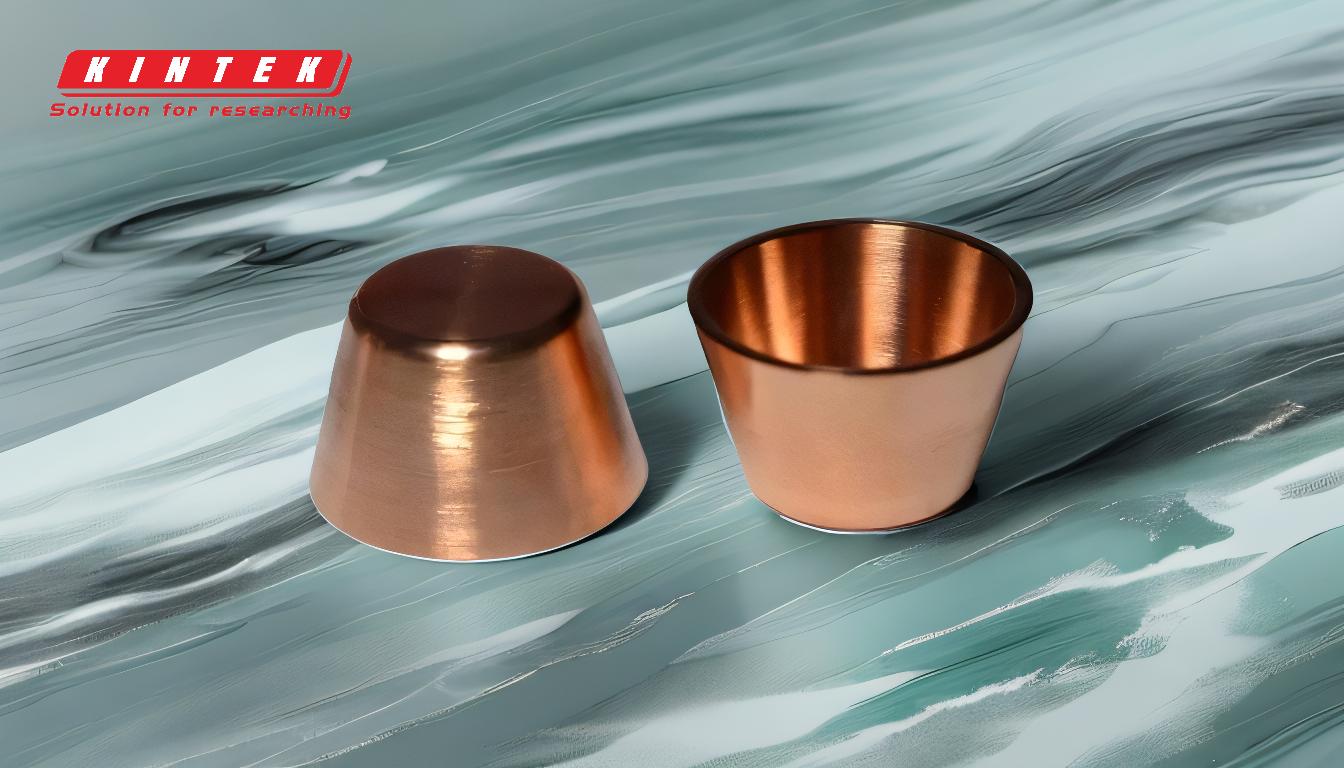
-
熱蒸発プロセス:
- 熱蒸発は、高真空チャンバー内で固体材料を蒸発するまで加熱し、蒸気流を発生させることで機能する。
- 気化した材料は真空中を移動し、基板上に堆積して薄膜を形成する。
- 加熱は、材料の特性に応じて、電気抵抗加熱器または電子ビーム蒸発器を使用して行うことができる。
- この方法は、融点の低い材料に特に有効で、OLEDや薄膜トランジスタなどの用途で一般的に使用されています。
-
熱蒸発法の利点:
- 高い蒸着率:熱蒸発は強固な蒸気流を生成するため、他の方法と比較してより速い成膜が可能です。
- 簡便性:真空チャンバーと加熱源を必要とするだけである。
- 材料適合性:分解せずに気化しやすい材料に適している。
-
スパッタリングプロセス:
- スパッタリングでは、ターゲット材料に高エネルギーの粒子(通常はイオン)を衝突させ、原子やクラスターを放出させる。
- 放出された粒子は真空中を移動し、基板上に堆積して薄膜を形成する。
- この方法は汎用性が高く、金属、セラミック、プラスチックなど幅広い材料に使用できます。
-
スパッタリングの利点:
- 素材の多様性:スパッタリングは、高融点を含む様々な材料を成膜することができます。
- 均一なコーティング:このプロセスにより、非常に均一で高密度な成膜が可能になる。
- 制御と精度:スパッタリングは、膜厚と組成の優れた制御が可能であるため、複雑な多層構造に適している。
-
熱蒸着とスパッタリングの比較:
- 成膜メカニズム:熱蒸発は熱エネルギーを利用して材料を蒸発させるのに対し、スパッタリングは高エネルギー粒子による運動エネルギーを利用する。
- 材料の互換性:熱蒸発は融点の低い材料に適しているが、スパッタリングはより幅広い材料に対応できる。
- 蒸着速度:熱蒸発法は一般的に蒸着速度が速く、特定の用途に適している。
- フィルム品質:スパッタリングは一般的に、特に複雑な構造や多層構造において、より優れた密着性と均一性を持つ膜を生成する。
-
応用例:
- 熱蒸発:OLED、薄膜トランジスタ、その他の電子デバイスの製造によく使用される。
- スパッタリング:汎用性と精度の高さから、半導体産業、光学コーティング、装飾仕上げなどに広く利用されている。
まとめると、熱蒸着とスパッタリングはどちらも薄膜形成に不可欠な技術であり、それぞれに利点と理想的な用途がある。熱蒸発法は、特定の材料に対してはより単純で高速であるが、スパッタリングはより多様性と制御性が高く、より幅広い材料と複雑な膜構造に適している。
総括表:
側面 | 熱蒸発 | スパッタリング |
---|---|---|
蒸着メカニズム | 熱エネルギーが材料を蒸発させる | 高エネルギー粒子が材料原子を放出 |
材料適合性 | 低融点材料に最適 | 幅広い材料に最適 |
蒸着率 | 高い蒸着率 | 熱蒸着に比べて遅い |
フィルム品質 | シンプルな用途に最適 | 優れた接着性と均一性 |
用途 | 有機EL、薄膜トランジスタ | 半導体、光学コーティング |
お客様のプロジェクトに適したPVD技術の選択にお困りですか? 今すぐ専門家にお問い合わせください !