PVD(Physical Vapor Deposition)とCVD(Chemical Vapor Deposition)は、基板上に薄膜を成膜するために使用される2つの高度なコーティング技術ですが、そのプロセス、材料、用途は大きく異なります。PVDは固体材料を物理的に気化させ、真空中で比較的低い温度(250℃~450℃)で基板上に蒸着させる。対照的に、CVDは気体材料と基板との化学反応に依存し、高温(450℃~1050℃)で行われる。PVDは、その耐久性と環境への配慮から、宝飾品、金物、自動車部品などの装飾的・機能的用途に広く使用されている。一方、CVDは、半導体や高性能セラミックなど、緻密で均一なコーティングを必要とする用途に好まれている。どちらの方法にも独自の利点があり、その選択はアプリケーションの具体的な要件によって決まる。
キーポイントの説明
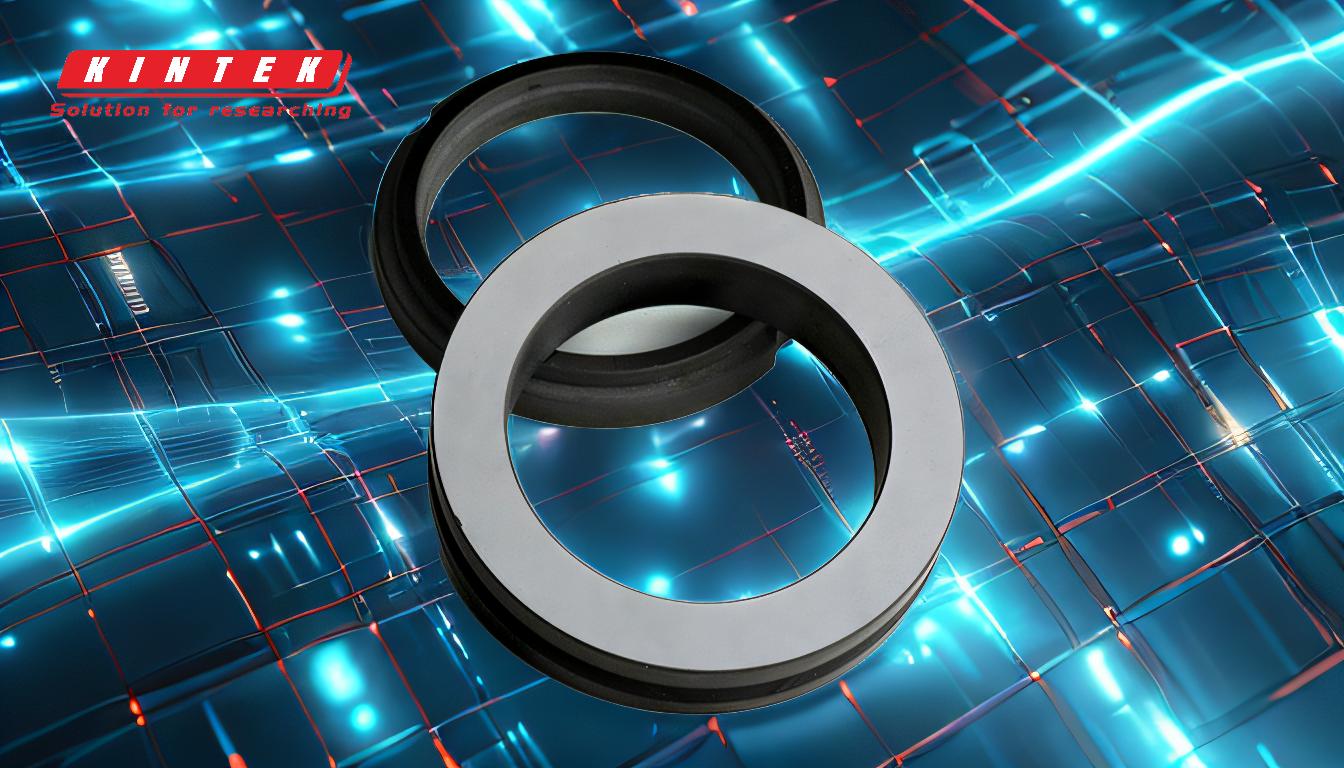
-
メカニズム:
- PVD:固体材料を物理的に気化させ、真空中で基板上に蒸着させる。このプロセスは主に物理的な力によって行われる。
- CVD:ガス状物質と基材との化学反応に頼る。ガス状の前駆物質が基材表面で反応し、皮膜を形成する。
-
使用温度:
- PVD:通常、250℃から450℃の低温で作動する。そのため、高温に耐えられない基板に適している。
- CVD:450℃から1050℃の高温を必要とするため、そのような条件に耐えられる基材に限定されることがある。
-
コーティングの性質:
- PVD:金属、合金、セラミックなどの固体材料を使用。このプロセスでは、さまざまな材料の成膜が可能。
- CVD:気体材料を利用し、通常はセラミックとポリマーに限定される。化学反応により、非常に均一で緻密な皮膜を形成することができる。
-
コーティング範囲:
- PVD:ライン・オブ・サイト蒸着プロセスにより、複雑な形状に優れたカバレッジを提供する。ただし、均一なカバレッジを確保するために、基板の回転や移動が必要になる場合がある。
- CVD:気相反応により基板表面全体に均一に発生するため、複雑な形状でも優れたコンフォーマルカバレッジを実現。
-
膜厚と平滑性:
- PVD:一般的に膜厚が薄く、滑らかな表面仕上げが可能。コーティングの密度は低いが、塗布速度は速い。
- CVD:より厚く、より緻密で、より均一な皮膜が得られる。このプロセスは時間がかかるが、優れた機械的・化学的特性を持つコーティングが得られる。
-
用途:
- PVD:宝飾品、ドアや窓の金具、自動車部品(ホイール、ピストンなど)、手術器具、ドリルビットなど、装飾的・機能的用途に広く使用されている。また、クロムめっきに代わる環境に優しいめっきであり、製品の寿命を最大10倍向上させる。
- CVD:半導体製造、高温セラミック、過酷な条件にさらされる工具や部品の保護コーティングなどの高性能用途に適している。
-
環境および経済性:
- PVD:有害物質を生成しないため、環境に優しいと考えられている。また、特に金物や装飾品業界では、大量生産に適したコスト効率も高い。
- CVD:高温と特殊な装置が必要なため運用コストが高くなる可能性があるが、優れたコーティング品質が得られるため、ハイテク産業では欠かせない。
まとめると、PVDとCVDのどちらを選択するかは、希望するコーティング特性、基材、運用上の制約など、アプリケーションの具体的な要件によって決まる。どちらの技術にも独自の利点があり、現代の製造および材料科学において不可欠なツールとなっている。
総括表
側面 | PVD(物理的気相成長) | CVD(化学蒸着) |
---|---|---|
動作メカニズム | 真空中での固体材料の物理的気化。 | ガス状物質と基板との化学反応。 |
使用温度 | 250°C ~ 450°C | 450°C~1050°C |
コーティング物質 | 固体材料(金属、合金、セラミックス) | 気体材料(セラミックス、ポリマー) |
適用範囲 | 複雑な形状に最適。基板の回転が必要な場合がある。 | 複雑な形状のコンフォーマルカバレッジに優れる。 |
フィルム厚さ | より薄く滑らかなフィルム;密度は低いが、塗布に時間がかかる。 | より厚く、より緻密で、より均一なフィルム。 |
用途 | 宝飾品、ハードウェア、自動車部品、手術器具、ドリルビット | 半導体、高温セラミック、極限環境用保護膜 |
環境への影響 | 環境に優しい;有害物質が発生しない | 運用コストが高い。 |
お客様のプロジェクトにPVDとCVDのどちらを使用するか決めるのにお困りですか? 最適なソリューションを見つけるために 最適なソリューションをお探しください!