鍛造は、局部的な圧縮力を利用して金属を成形する製造工程である。鍛造は、航空宇宙、自動車、建築など、高強度部品を必要とする産業で広く用いられている。鍛造の一種である熱間鍛造では、金属を再結晶温度以上に加熱して成形しやすくする。この方法は、優れた機械的特性、複雑な形状、高い耐久性を持つ部品を製造するのに特に有利である。熱間鍛造は、エンジン部品、工具、構造部品の製造など、強度、精度、材料効率が重要な用途に最適です。
キーポイントの説明
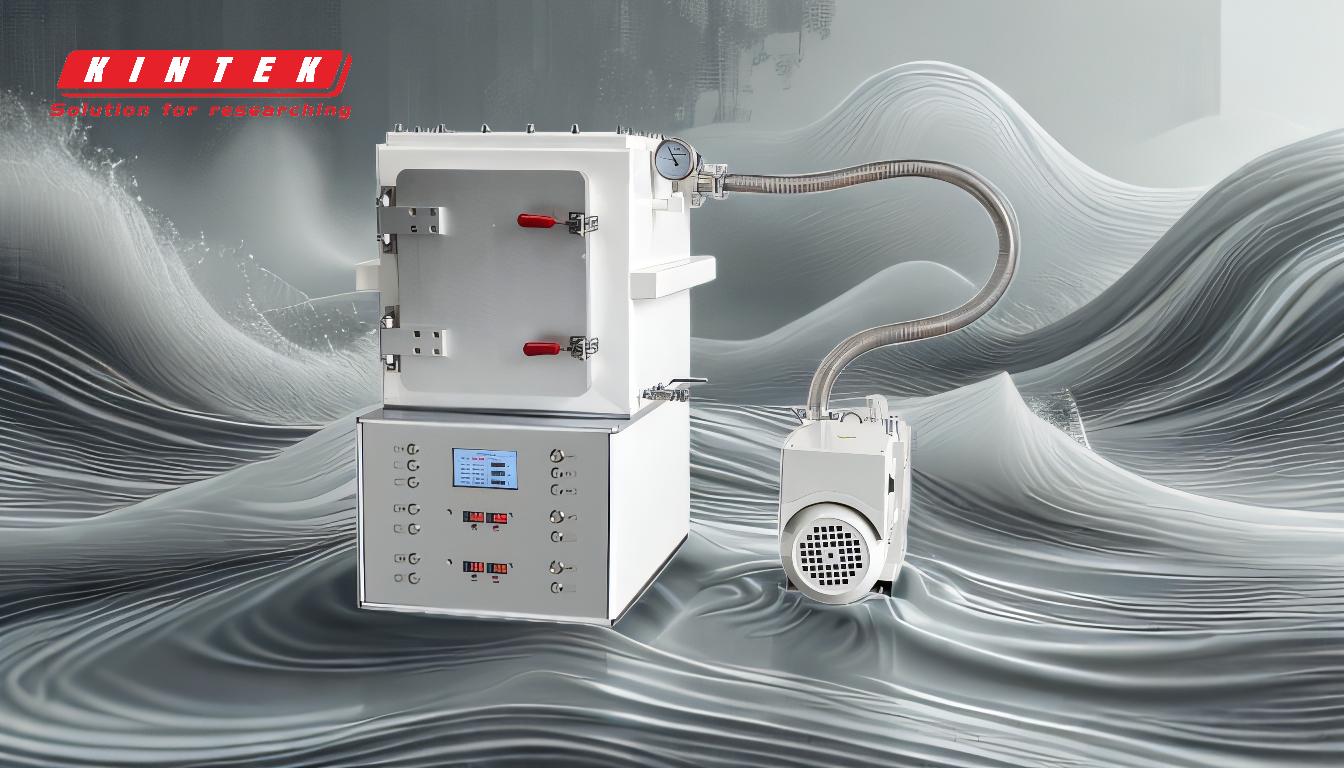
-
熱間鍛造の定義:
- 熱間鍛造は金属加工プロセスのひとつで、材料を再結晶点以上の温度(鋼の場合は通常950℃~1250℃)に加熱する。この加熱により、金属はより可鍛性になり、ひびが入ったり割れたりすることなく、高圧下で成形できるようになる。
- この工程では、金型とハンマーを使って、加熱された金属を希望の形状に変形させる。高温により変形に必要な力が減少し、金属の流動特性が向上する。
-
熱間鍛造の利点:
- 優れた強度:熱間鍛造は、金属の結晶粒組織を微細化することにより、引張強度や耐衝撃性などの機械的性質を向上させる。
- 複雑形状:このプロセスでは、他の製造方法では困難または不可能な、複雑で特注の形状を作成することができます。
- 材料効率:熱間鍛造は、追加の機械加工をほとんど必要としないニアネットシェイプの部品を製造できるため、材料の無駄を最小限に抑えることができます。
- 費用対効果:大規模生産の場合、熱間鍛造は人件費と材料費の削減により、他の方法よりも経済的であることが多い。
-
熱間鍛造を使用する場合:
- 高強度アプリケーション:熱間鍛造は、クランクシャフト、コネクティングロッド、ギアなど、極度の応力に耐えなければならない部品に最適です。
- 大型または複雑な部品:このプロセスは、タービンブレードや重機の構造部品など、大型部品や複雑な形状の部品の製造に適している。
- 高温環境:エンジン部品のような高温環境下で使用される部品は、熱間鍛造によって向上した熱安定性の恩恵を受ける。
- 大量生産:熱間鍛造は、大量生産に適したコスト効率に優れているため、自動車や航空宇宙などの産業で好まれています。
-
他の鍛造方法との比較:
- 冷間鍛造:熱間鍛造と異なり、冷間鍛造は室温または室温に近い温度で行われる。より高い精度と表面仕上げが得られるが、複雑な形状や高強度要求には不向きである。
- 温間鍛造:この方法は中間温度で行われ、熱間鍛造と冷間鍛造の利点のバランスを提供する。ただし、熱間鍛造と同レベルの材料の微細化は達成できない場合がある。
-
熱間鍛造に適した材料:
- 鉄鋼および合金:熱間鍛造は、高温・高圧に耐える炭素鋼、合金鋼、ステンレス鋼によく用いられる。
- 非鉄金属:アルミニウム、銅、チタンなどの金属も熱間鍛造が可能ですが、特殊な温度範囲と取り扱い技術が必要です。
-
熱間鍛造の用途:
- 自動車産業:熱間鍛造は、エンジン部品、トランスミッション部品、サスペンションシステムなどの重要部品の製造に使用される。
- 航空宇宙産業:ランディングギア、タービンディスク、構造部品などの高強度部品の製造に採用されている。
- 建設・重機:熱間鍛造部品は、その耐久性と耐荷重性により、クレーン、ブルドーザー、鉱山機械などの機器に不可欠です。
要約すると、熱間鍛造は、強度、材料効率、費用対効果の面で大きな利点を提供する、多用途で効率的な製造プロセスである。特に、高性能部品、複雑な形状、大規模生産を必要とする用途に適しています。熱間鍛造の利点と理想的な使用事例を理解することで、メーカーは生産工程にいつ熱間鍛造を取り入れるかについて、十分な情報を得た上で決定することができます。
まとめ表
アスペクト | 詳細 |
---|---|
定義 | 材料を再結晶点以上に加熱する金属加工プロセス。 |
温度範囲 | 950°C~1250°C(鋼の場合 |
利点 | 優れた強度、複雑な形状、材料効率、費用対効果 |
理想的な用途 | 高強度部品、大型/複雑な部品、高温環境。 |
材料 | スチール、合金、アルミニウム、銅、チタン |
産業 | 自動車、航空宇宙、建設、重機。 |
熱間鍛造で生産を強化する準備はできていますか? 今すぐご連絡ください までご連絡ください!