CVD(Chemical Vapor Deposition)とPVD(Physical Vapor Deposition)は、基板上に薄膜を堆積させ、その機能性、耐久性、外的要因に対する耐性を向上させるために使用される高度なコーティング技術である。どちらの方法も基板の性能を向上させることを目的としていますが、そのプロセス、結合メカニズム、特定の材料への適合性において大きく異なります。CVDは高温での化学反応を伴い、強力な拡散結合を形成するが、温度に敏感な材料には適さない場合がある。一方、PVDは真空条件下で行われるため、より幅広い材料に対応できるが、結合力は比較的弱い。これらの違いを理解することは、基材や希望する結果に応じて適切な技術を選択する上で極めて重要である。
キーポイントの説明
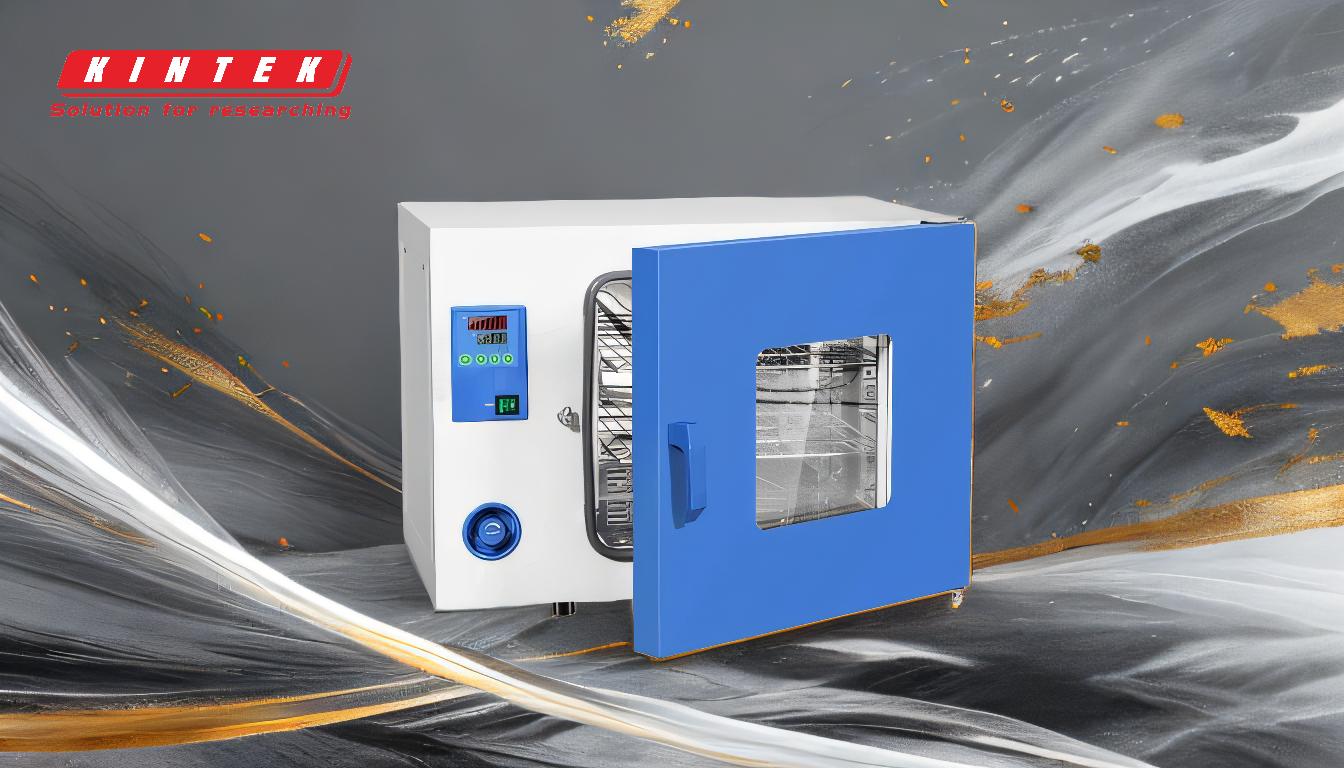
-
CVDとPVDの定義と目的:
- CVD(化学気相成長法):基材を揮発性の前駆物質にさらし、その前駆物質が反応または分解して基材上に薄膜を形成するプロセス。この方法は、基板の機能強化、新しい特性の導入、保護のために広く使用されている。
- PVD(物理蒸着):材料を固体ソースから物理的に気化させ、基板上に堆積させる技術。PVDはCVDと同様の目的で使用されるが、化学反応ではなく物理的プロセスに依存する。
-
CVDとPVDの主な違い:
-
プロセス・メカニズム:
- CVD:高温での化学反応を伴うため、非直視下での成膜が可能。その結果、均一な層構造と厚みの均一性が得られる。
- PVD:物理的な気化と蒸着に依存しており、視線方向のプロセスである。このため、CVDに比べて均一なコーティングが得られないことがある。
-
接着強度:
- CVD:コーティングと基材との間に拡散型の結合を形成し、一般的に強度と耐久性が向上する。
- PVD:機械的結合を形成するが、一般的にCVDによる拡散結合より弱い。
-
温度条件:
- CVD:高い処理温度を必要とするため、温度に敏感な基板では使用が制限されることがある。
- PVD:真空条件と低温で動作するため、熱に敏感な材料を含む幅広い材料に適しています。
-
プロセス・メカニズム:
-
用途と適性:
- CVD:半導体製造、保護膜、高温環境など、強靭で耐久性があり、均一な膜厚を必要とする用途に最適。
- PVD:プラスチック、光学部品、装飾仕上げのコーティングなど、低い処理温度が必要な用途に適している。
-
利点と限界:
-
CVDの利点:
- より強力な接着と耐久性のあるコーティング。
- 非直視型プロセスにより、均一な膜厚が得られます。
-
CVDの限界:
- 処理温度が高いため、温度に敏感な材料には使用できない。
-
PVDの利点:
- 加工温度が低いため、幅広い材料に使用可能。
- 汎用性が高く、複雑な形状に適している。
-
PVDの限界:
- CVDに比べ結合が弱い。
- ラインオブサイトプロセスでは、均一なコーティングが得られない場合がある。
-
CVDの利点:
-
CVDとPVDの選択:
- CVDとPVDのどちらを選択するかは、基材の材質、要求されるコーティング特性、加工上の制約など、アプリケーションの具体的な要件によって決まる。耐熱性基材への高強度、高耐久性コーティングには、CVDが好まれることが多い。温度に敏感な材料や低い処理温度を必要とする用途には、PVDが適しています。
これらの重要なポイントを理解することで、装置や消耗品の購入者は、どのコーティング技術がニーズに最も適しているかについて、十分な情報を得た上で決定することができ、最適な性能と費用対効果を確保することができます。
総括表
側面 | CVD(化学蒸着) | PVD(物理蒸着) |
---|---|---|
プロセスメカニズム | 高温での化学反応、非直視下蒸着 | 物理的気化と蒸着、ライン・オブ・サイト・プロセス |
接着強度 | 強い拡散型ボンド | 機械的結合(CVDより弱い) |
温度 | 高温処理:熱に敏感な素材には適さない | 低温:熱に敏感な素材に適しています。 |
用途 | 半導体製造、保護膜、高温環境 | プラスチック、光学部品、装飾仕上げ |
利点 | 強固な接着、均一な膜厚 | 低温、複雑な形状にも対応可能 |
制限事項 | 高温のため、熱に弱い素材には使用できない。 | 接着が弱く、均一なコーティングができない |
お客様の用途に適したコーティング技術の選択にお困りですか? 今すぐ専門家にご相談ください!