レーザー焼結、特に選択的レーザー焼結(SLS)は、ユニークな利点と欠点を提供する汎用性の高い付加製造技術である。従来の焼結法では困難な、非常に複雑で機能的な形状の製造が可能です。しかし、設備と材料の両面で多大なコストがかかり、熟練したオペレーターを必要とする。一方、粉末冶金のような代替法は、大規模生産には費用対効果が高いが、不均一な部品になる可能性がある。高速焼結は、密度と強度を向上させる有望な方法であるが、普遍的に支持されているわけではなく、潜在的な限界があることを示している。
キーポイントの説明
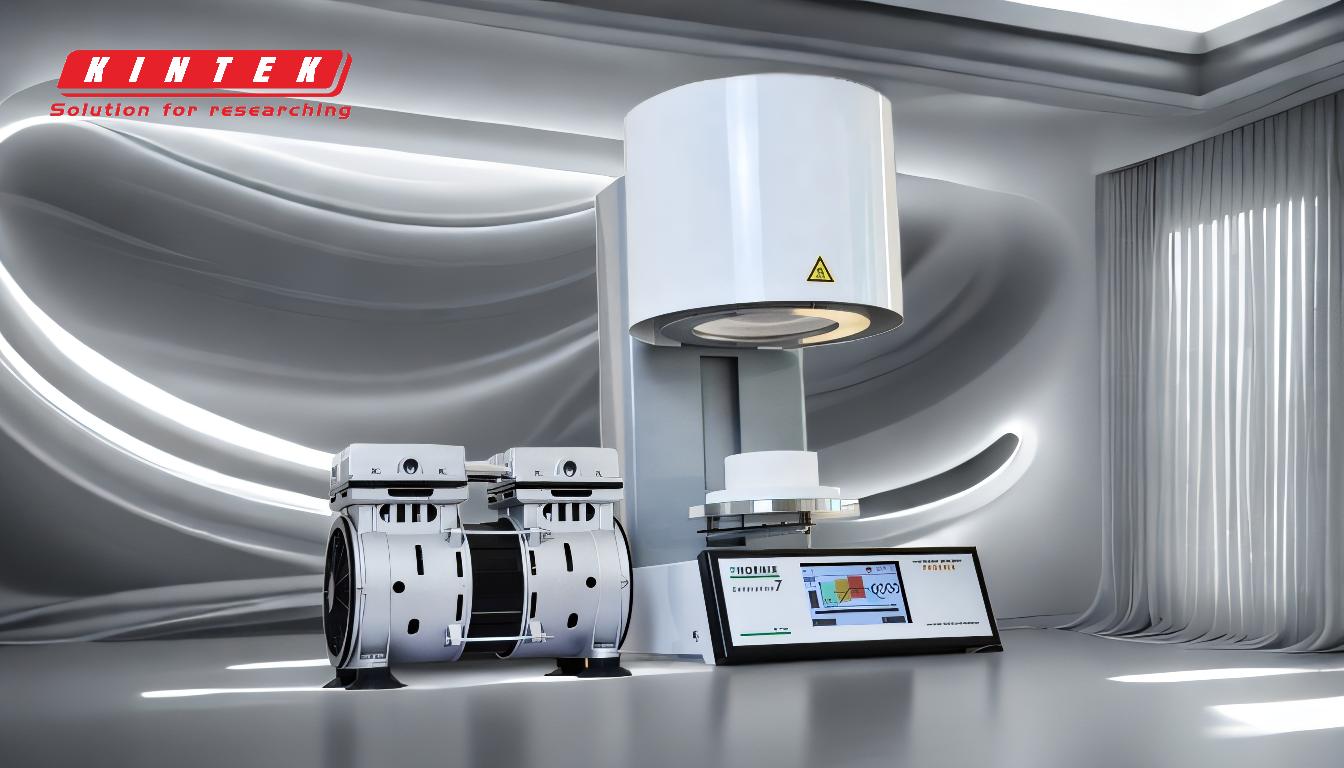
-
レーザー焼結の利点
- 複雑で機能的な形状 レーザー焼結、特にSLSは、従来の焼結法では困難または不可能な複雑で機能的な形状の作成に優れています。そのため、航空宇宙や医療機器など、高い精度と複雑さが要求される用途に最適です。
- 材料の多様性: SLSは、ポリマー、金属、セラミックなど、幅広い材料に対応できるため、さまざまな産業への応用が可能です。
- 最小限の後処理: SLSで製造された部品は、他の積層造形法に比べて後処理が少なくて済むことが多い。
-
レーザー焼結の短所
- 高コスト: SLS装置の初期投資額は大きく、25万ドルを超えることが多い。さらに、SLSに使用される材料は高価であるため、全体的なコストはさらに高くなります。
- 熟練オペレーターの要件: SLS は専門的なスキルとトレーニングを持つオペレーターを必要とするため、運用コストと複雑さが増す。
- 限られた拡張性: SLSはプロトタイピングや小規模生産には優れていますが、粉末冶金のような方法と比較すると、大規模製造の効率は劣ります。
-
粉末冶金との比較:
- 費用対効果: 粉末冶金は一般に、設備と材料の両面でより安価であるため、大規模生産に適している。
- 操作の容易さ: SLSと異なり、粉末冶金は熟練したオペレーターを必要としないため、人件費とトレーニングの必要性を削減できます。
- 均一性の問題: 粉末冶金の欠点として、粉末と金型間の摩擦により部品が不均一になる可能性があり、これが最終製品の品質と一貫性に影響を及ぼす可能性がある。
-
高速焼結:
- 密度と強度の向上: 高速焼結は、従来の焼結方法と比較して、密度と強度がわずかに高い部品を製造できることを示唆する研究もある。
- 限定的な支持 このような利点があるにもかかわらず、すべての材料メーカー、特にジルコニアを扱うメーカーが高速焼結を推奨しているわけではない。これは、材料の相溶性、プロセスの安定性、その他の技術的限界に関する懸念が原因である可能性がある。
-
装置および消耗品購入者のための考慮事項:
- アプリケーションの要件: SLS と他の焼結法のどちらを採用するかを決定する際、購入者は、複雑な形状の必要性、材料特性、生産量など、アプリケーション固有の要件を考慮する必要があります。
- 予算の制約: SLSに関連する高コストは、特に予算が限られている組織や、大規模な生産を必要とする組織にとっては、制限要因となる可能性がある。
- オペレーターの専門知識: 熟練したオペレーターの必要性は、初期設定と継続的な運用コストの両方に影響する可能性があるため、意思決定プロセスに織り込んでおく必要があります。
- 材料の適合性: 高速焼結を検討している場合は、材料の適合性を確 認し、その方法が目的の用途に適していることを確認す るためにサプライヤーと相談することが不可欠である。
要約すると、レーザー焼結、特にSLSは、設計の柔軟性と材料の多様性という点で大きな利点を提供するが、高いコストと操作の複雑さを伴う。粉末冶金のような代替法は、大規模生産ではコスト効率が高いが、コンポーネントの均一性で妥協する可能性がある。高速焼結は、材料特性を向上させる可能性を示しているが、普遍的に受け入れられているわけではなく、その限界について慎重に検討する必要があることを示している。購入者は、十分な情報に基 づいて決定を下すために、特定のニーズと制約に照 らしてこれらの要因を比較検討すべきである。
要約表
側面 | レーザー焼結 (SLS) | 粉末冶金 | 高速焼結 |
---|---|---|---|
複雑形状 | 複雑で機能的な形状の作成に優れている | 複雑な形状の作成には限界がある | 利用可能なデータが限られている |
材料の多様性 | ポリマー、金属、セラミックに対応 | 材料の選択肢が限られる | ジルコニアのような材料との互換性の問題の可能性 |
コスト | 高い初期投資(25万ドル以上)と高価な材料 | 大規模生産の方が費用対効果が高い | コストにはばらつきがある。 |
オペレーターのスキル | 熟練したオペレーターが必要 | 操作が簡単で、熟練労働者が少ない | 専門知識が必要 |
拡張性 | プロトタイピングと小規模生産に最適 | 大規模生産に最適 | 技術的な制約により、拡張性は限定的 |
後処理 | 必要な後処理は最小限 | より多くの後処理が必要な場合あり | 最小限の後処理 |
成分の均一性 | 高い精度と一貫性 | 不均一な構成部品の可能性 | 密度と強度は向上するが、裏付けは限定的 |
お客様の用途に適した焼結方法の選択にお困りですか? 当社の専門家に今すぐご連絡ください をご利用ください!