化学気相成長法(CVD)は、高純度、均一性、拡張性、汎用性など多くの利点を持ち、電気回路や複雑な表面コーティングなどの用途に適しているため、広く使用されている薄膜蒸着技術である。しかし、装置や前駆体ガスのコストが高い、動作温度が高い、大型材料や複雑な材料のコーティングに課題がある、といった限界もある。以下では、CVDの長所と短所を詳しくご紹介します。
要点の説明
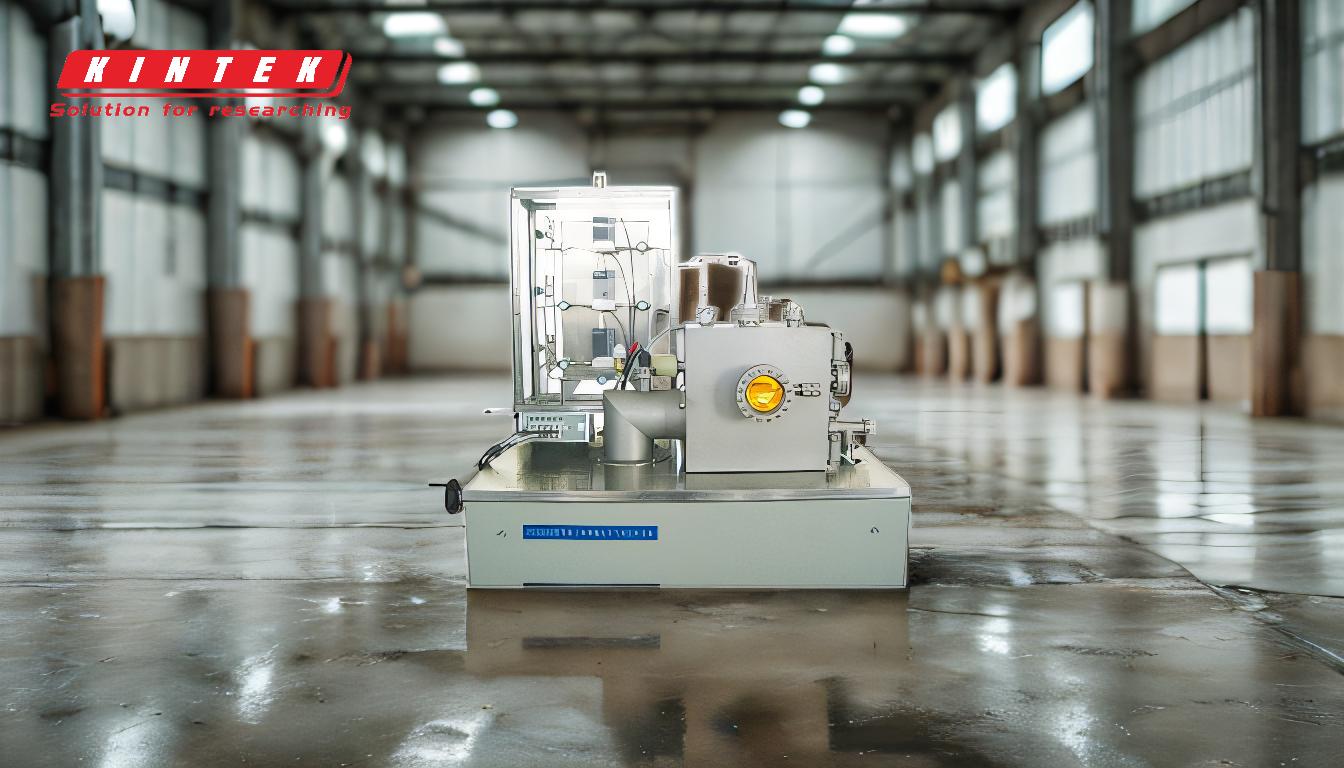
化学気相成長法(CVD)の利点:
-
高純度・高密度の薄膜:
- CVDは、半導体や光学コーティングなど、精密な材料特性を必要とする用途に不可欠な、極めて高純度・高密度の薄膜を作ります。
- このプロセスは化学反応に依存しており、コンタミネーションを最小限に抑え、高品質の結果を保証します。
-
均一性と制御:
- CVDでは、蒸着膜の膜厚、組成、微細構造を精密に制御できるため、特定の用途に合わせて特性を調整することが可能です。
- 膜は層内でも基板表面全体でも均一であるため、大面積のコーティングに理想的である。
-
材料と基板における多様性:
- CVDは、金属、半導体、セラミック、ポリマーなど、さまざまな材料を成膜できる。
- 金属、ガラス、プラスチックなど、さまざまな基板材料と互換性があるため、さまざまな産業への適応性が高い。
-
スケーラビリティと高い成膜速度:
- CVDはスケーラブルで、小規模な研究にも大規模な工業生産にも適している。
- 成膜速度が速いため、大面積の薄膜を短時間で効率よく作ることができる。
-
複雑な表面を包み込む特性:
- CVDは、非直線性であるため、不規則な表面や複雑な形状の表面を均一にコーティングすることができ、精密部品や複雑なデザインに最適です。
-
耐久性のある高性能コーティング:
- CVDで製造されるコーティングは耐久性に優れ、高ストレス環境、極端な温度、温度変化に耐えることができる。
- CVDで使用されるガスは、耐食性や耐摩耗性など、特定の特性に合わせて最適化することができます。
-
シンプルで操作しやすい装置:
- CVD装置は操作やメンテナンスが比較的簡単で、操作の複雑さやダウンタイムを減らすことができる。
化学気相成長法(CVD)の欠点:
-
装置と前駆体ガスのコストが高い:
- CVD装置の初期投資が高く、プロセスで使用される前駆体ガスも高価なため、全体的なコストが高くなる。
-
高い動作温度:
- CVDは一般的に高温を必要とするため、温度に敏感な材料や基板では使用が制限されることがある。
- また、高温はコーティングや基板に残留応力をもたらす可能性があり、蒸着パラメーターの慎重な管理が必要となる。
-
限られた現場での適用:
- CVDは通常、現場ではなく専門のコーティングセンターで行われるため、用途によっては不便な場合がある。
- すべての部品は、コーティングのために個々の部品に分解しなければならず、プロセスが複雑になる。
-
真空チャンバーによるサイズの制約:
- 真空チャンバーのサイズにより、より大きな表面へのコーティングが制限されるため、大規模なアプリケーションへの使用が制限される。
-
オール・オア・ナッシング・コーティング・プロセス:
- CVDはオール・オア・ナッシングのプロセスであるため、部分的なコーティングや選択的な被覆を行うことは困難である。
-
前駆体ガスによる潜在的危険性:
- CVDで使用される前駆体ガスの中には危険なものもあり、厳格な安全対策と取り扱いプロトコルが必要となる。
-
完全な被覆を達成する上での課題:
- CVDは複雑な表面をコーティングすることができるが、特に複雑な形状の場合、完全で均一な被覆を達成することは困難である。
結論
CVDは、高純度、均一性、スケーラビリティなどの利点を備えた、汎用性の高い効果的な薄膜蒸着法である。複雑な表面をコーティングし、耐久性のある高性能な膜を作ることができるため、エレクトロニクス、光学、航空宇宙などの業界では欠かせないものとなっている。しかし、コストが高いこと、動作温度が高いこと、大きな材料や温度に敏感な材料のコーティングには限界があることは、顕著な欠点である。これらの長所と短所を理解することは、特定の用途に適切な成膜技術としてCVDを選択するために不可欠である。
総括表
側面 | メリット | デメリット |
---|---|---|
純度と密度 | 膜の純度と密度が高く、半導体や光学コーティングに最適。 | 装置と前駆体ガスのコストが高い。 |
均一性と制御 | 厚さ、組成、微細構造の精密制御。 | 動作温度が高く、温度に敏感な材料での使用が制限される。 |
汎用性 | 様々な基材に対応し、幅広い材料を成膜。 | 現場での適用には限界があり、専門のコーティングセンターが必要。 |
拡張性 | 小規模研究にも大規模生産にも対応可能。 | 真空チャンバーによるサイズの制約があるため、大規模な応用には限界がある。 |
複雑な表面 | 不規則または複雑な形状の表面を均一にコーティング。 | オール・オア・ナッシングのコーティングプロセス。 |
耐久性 | 過酷な環境下で使用される、耐久性に優れた高性能コーティング剤。 | 前駆体ガスによる危険性があり、厳格な安全対策が必要。 |
使いやすさ | シンプルで操作しやすい装置。 | 複雑な形状を完全にカバーするための課題。 |
CVDがお客様のアプリケーションをどのように強化できるか、検討する準備はできていますか? 今すぐご連絡ください までご連絡ください!