真空コーターは、物理的気相成長(PVD)と呼ばれるプロセスによって、金属やセラミックなどの基材に薄い保護膜を形成するための特殊な機械です。このプロセスは真空チャンバー内で行われ、コーティング材料は熱エネルギーまたはプラズマを使用して気化またはイオン化され、制御された環境で基板上に蒸着されます。これにより、硬度、耐摩耗性、耐食性などの特性を向上させるナノスケールの層が形成される。真空コーターは、真空チャンバー、真空システム、電源、ガス入力システム、冷却システムなど、いくつかの重要なコンポーネントで構成されており、これらがすべて連携して、正確で効率的なコーティング成膜を実現します。
キーポイントの説明
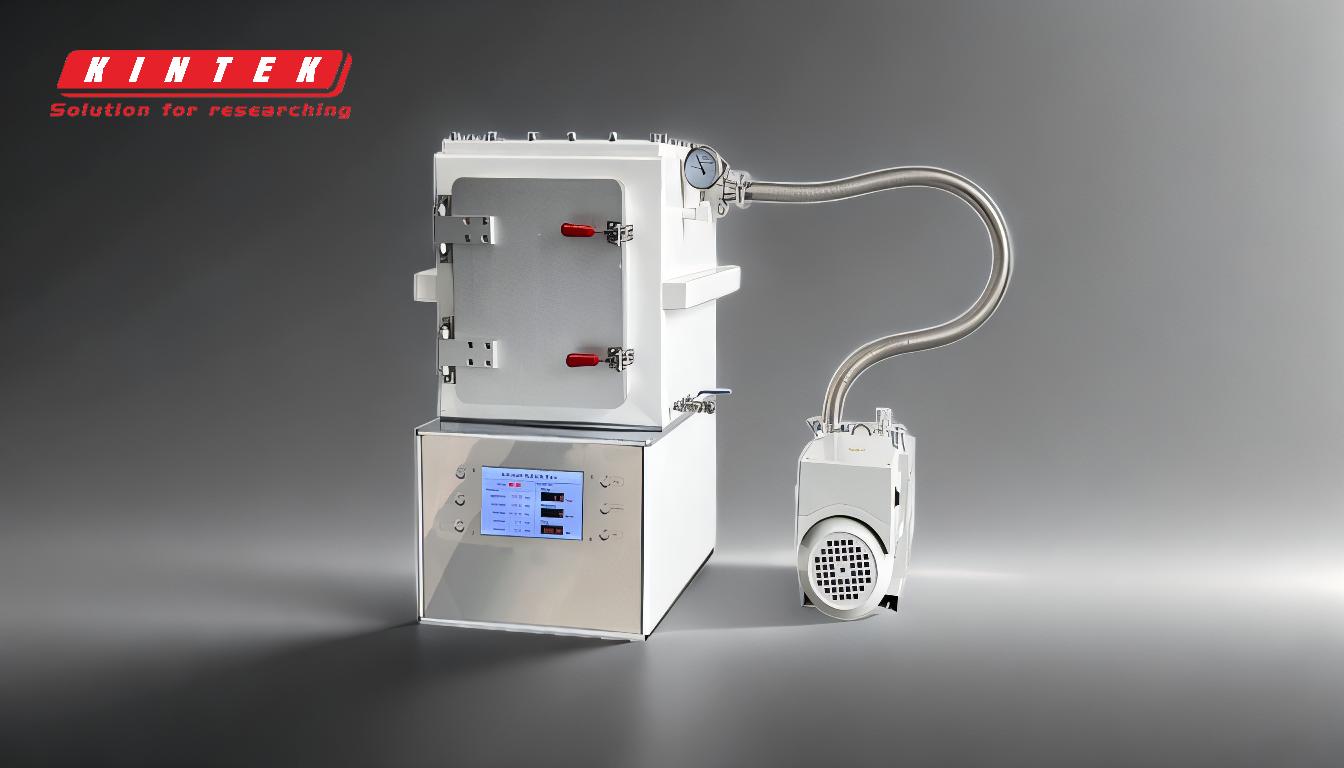
-
真空チャンバーとコーティング環境
- 真空チャンバーは真空コーターの中核であり、制御された大気圧以下の環境をコーティングプロセスに提供します。
- 真空は、汚染物質を除去し、コーティングの純度を保証するために不可欠です。また、基板上に蒸着される気化粒子を正確に制御することもできます。
- チャンバーは高温・高圧に対応するよう設計されており、コーティングプロセス中の安定性を確保します。
-
コーティング材料の気化
- コーティング材料(通常、金属またはセラミック)は、真空チャンバー内で気化またはイオン化されます。
- これは、熱エネルギー(例えば、抵抗加熱)またはプラズマを使用して達成され、材料を原子または分子粒子に分解する。
- 気化した材料は、真空環境を通して基板に運ばれます。
-
蒸着プロセス
- 気化したコーティング剤が基材上に凝縮し、薄く均一な層を形成する。
- このプロセスは、コーティングの望ましい厚みと特性を確保するために高度に制御され、多くの場合ナノスケールで行われる。
- 成膜は、用途に応じてスパッタリングや蒸着など、さまざまなPVD技術によって行われる。
-
基板の準備
- コーティングの前に、基材は汚染物質を除去し、コーティングの適切な接着を確保するために徹底的な洗浄を受けます。
- これには、研磨洗浄、化学処理、真空チャンバー内でのプラズマ洗浄などが含まれます。
- 適切な表面処理は、高品質で耐久性のあるコーティングを実現するために非常に重要です。
-
真空塗装機の主な構成要素
- 真空チャンバーとコーティング装置:基材とコーティング材を収容し、制御された環境を提供する。
- 真空取得システム:ポンプとシールで真空を作り、維持します。
- 真空測定システム:チャンバー内の圧力レベルをモニターします。
- 電源:気化、イオン化、プラズマ発生のためのエネルギーを供給する。
- プロセスガス入力システム:反応性ガスまたは不活性ガスを導入し、コーティング工程を強化する。
- 機械的伝達システム:必要に応じて基材やコーティング材を移動させる。
- 加熱と温度制御:最適なコーティング条件のための温度調整
- イオン蒸発とスパッタリングソース:気化したコーティング剤を生成する。
- 水冷システム:機械部品の過熱を防ぎます。
-
用途と利点
- 真空コーティングは、航空宇宙、自動車、電子機器、医療機器などの産業で広く使用されています。
- コーティングにより、硬度、耐摩耗性、耐食性、熱安定性などの特性が向上します。
- このプロセスは、廃棄物を最小限に抑え、有害な化学物質を使用しないため、環境に優しい。
-
プロセス制御と精度
- 真空コーターは、コーティングの厚み、組成、均一性を正確に制御することができます。
- 高度なモニタリングシステムにより、コーティングの一貫した品質と性能を保証します。
- ナノスケールの層を成膜できる真空コーティングは、高精度のアプリケーションに最適です。
これらの要素を組み合わせることで、真空コーターは現代産業の厳しい要求を満たす高性能コーティングを作り出します。このプロセスは、高度なエンジニアリングと材料科学の統合の証であり、重要な部品の耐久性と機能性を高めるソリューションを提供します。
総括表
主要コンポーネント | 機能 |
---|---|
真空チャンバー | コーティング成膜のために制御された大気圧以下の環境を提供します。 |
真空取得システム | ポンプとシールで真空を作り、維持する。 |
電源 | 気化、イオン化、プラズマ発生のためのエネルギーを供給する。 |
プロセスガス導入システム | 反応性ガスや不活性ガスを導入し、コーティングプロセスを強化します。 |
水冷システム | 機械部品の過熱を防ぎます。 |
イオン蒸発/スパッタリングソース | 蒸着用の気化したコーティング材料を生成します。 |
精密コーティングで材料を強化する準備はできていますか? 今すぐご連絡ください バキュームコーターについて詳しく知る