物理的気相成長法(PVD)と化学的気相成長法(CVD)は、基材に薄膜コーティングを施すために広く用いられている2つの技術である。どちらの手法も表面特性を向上させることを目的としていますが、そのメカニズム、操作条件、結果として得られるコーティング特性は大きく異なります。PVDは、通常真空条件下で、固体ソースから基材への材料の物理的移動を伴うが、CVDは、気体前駆体と基材との化学反応に依存してコーティングを形成する。これらの違いは、コーティングの厚さ、均一性、必要な温度、材料の適合性などの要因に影響します。
キーポイントの説明
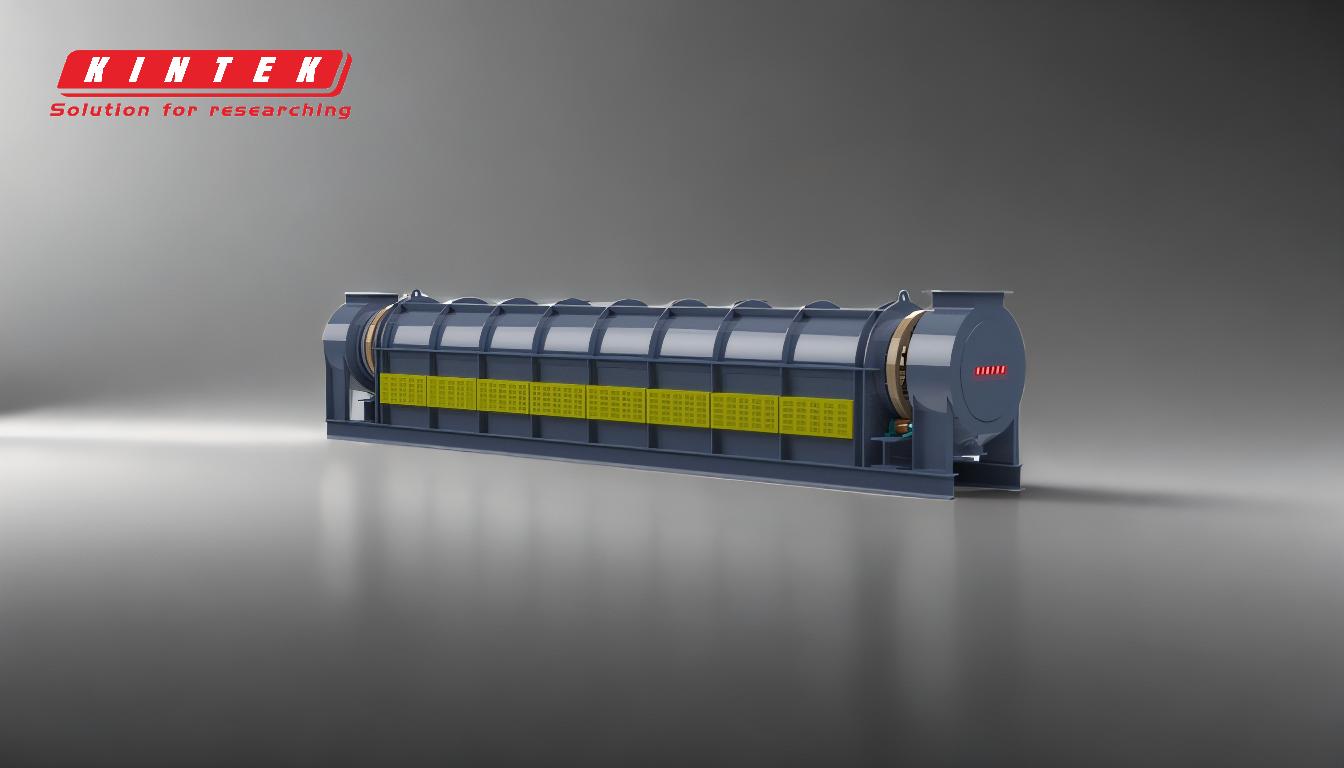
-
成膜メカニズム:
- PVD:PVDは、材料が固体ターゲットから物理的に気化され、基板上に蒸着されるライン・オブ・サイトプロセスです。このプロセスでは、ターゲット材料と基板間の化学反応は起こらない。その代わり、原子や分子がターゲットから放出され、基板表面で凝縮する。
- CVD:CVDでは、気体状の前駆物質と基板が化学反応を起こす。ガスは基材表面で反応し、固体のコーティングを形成する。このプロセスは多方向性であるため、コーティングは複雑な形状や隠れた部分をカバーすることができます。
-
使用温度:
- PVD:PVDは通常、250℃から500℃の低温で作動する。そのため、高温に耐えられない基板に適している。
- CVD:CVDでは、多くの場合450℃から1050℃の高温が必要である。高温は、コーティングを形成する化学反応を促進するために必要である。しかし、そのため、温度に敏感な素材への使用は制限される。
-
コーティングの厚みと均一性:
- PVD:PVDコーティングは一般的に薄く(3~5μm)、プロセスの視線性のため均一性に欠ける。しかし、塗布速度が速く、超硬質膜を得ることができる。
- CVD:CVDコーティングは、化学反応によって複雑な形状をよりよく覆うことができるため、より厚く(10~20μm)、より均一です。プロセスは遅いが、より緻密なコーティングができる。
-
素材適合性:
- PVD:PVDは、金属、合金、セラミックなど、さまざまな材料を成膜することができます。この汎用性により、さまざまな用途に適しています。
- CVD:CVDは通常、化学反応の性質上、セラミックとポリマーに限定される。材料適合性という点では汎用性が低い。
-
応力と表面特性:
- PVD:PVDコーティングは圧縮応力を示すことが多く、コーティングの耐久性と密着性を高めることができます。また、より滑らかな表面も得られます。
- CVD:CVDコーティングは加工温度が高いため引張応力が発生し、微細なクラックが発生する可能性がある。コーティングの密度は高くなるが、平滑性を得るために後加工が必要になる場合がある。
-
用途:
- PVD:PVDは、切削工具、装飾仕上げ、耐摩耗性表面など、薄くて硬いコーティングを必要とする用途で一般的に使用されています。
- CVD:CVDは、半導体製造、保護膜、高温部品など、厚く均一なコーティングが必要な用途に適しています。
これらの重要な違いを理解することで、購入者やエンジニアは、材料適合性、コーティング膜厚、使用条件などの具体的な要件に基づいて、適切な成膜技術を選択することができます。
要約表
側面 | PVD | CVD |
---|---|---|
成膜メカニズム | 固体ソースからの材料の物理的移動(ライン・オブ・サイト)。 | ガス状前駆体と基板との化学反応。 |
使用温度 | 250°C~500°C(低温)。 | 450℃~1050℃(高温)。 |
コーティング厚さ | 薄い(3~5μm)、均一性が低い。 | より厚い(10~20μm)、より均一。 |
材料適合性 | 金属、合金、セラミック(汎用性あり)。 | セラミックスとポリマー(汎用性は限定的)。 |
応力と表面 | 圧縮応力、より滑らかな表面。 | 引張応力、より緻密なコーティング、後処理が必要な場合がある。 |
用途 | 切削工具、装飾仕上げ、耐摩耗性表面 | 半導体製造、保護膜、高温部品 |
PVDとCVDの選択でお困りですか? 専門家にご相談ください にご相談ください!