ろう付けは、適切な技術、材料、条件が適用されれば、2 つの異なる金属を接合するために使用できる多用途の接合プロセスです。溶接とは異なり、ろう付けでは母材金属を溶かさず、代わりに融点の低い溶加材を使用して、強力で耐久性のある接合を作成します。この方法は、熱歪みや冶金学的不適合のリスクを最小限に抑えるため、異種金属を接合する場合に特に役立ちます。異なる金属のろう付けが成功するかどうかは、母材の金属の適合性、充填材の選択、表面処理、ろう付け環境などの要因によって決まります。適切な計画と実行により、ろう付けにより、銅と鋼、アルミニウムとステンレス鋼、さらには珍しい組み合わせなどの金属間に高品質の接合を生成できます。
重要なポイントの説明:
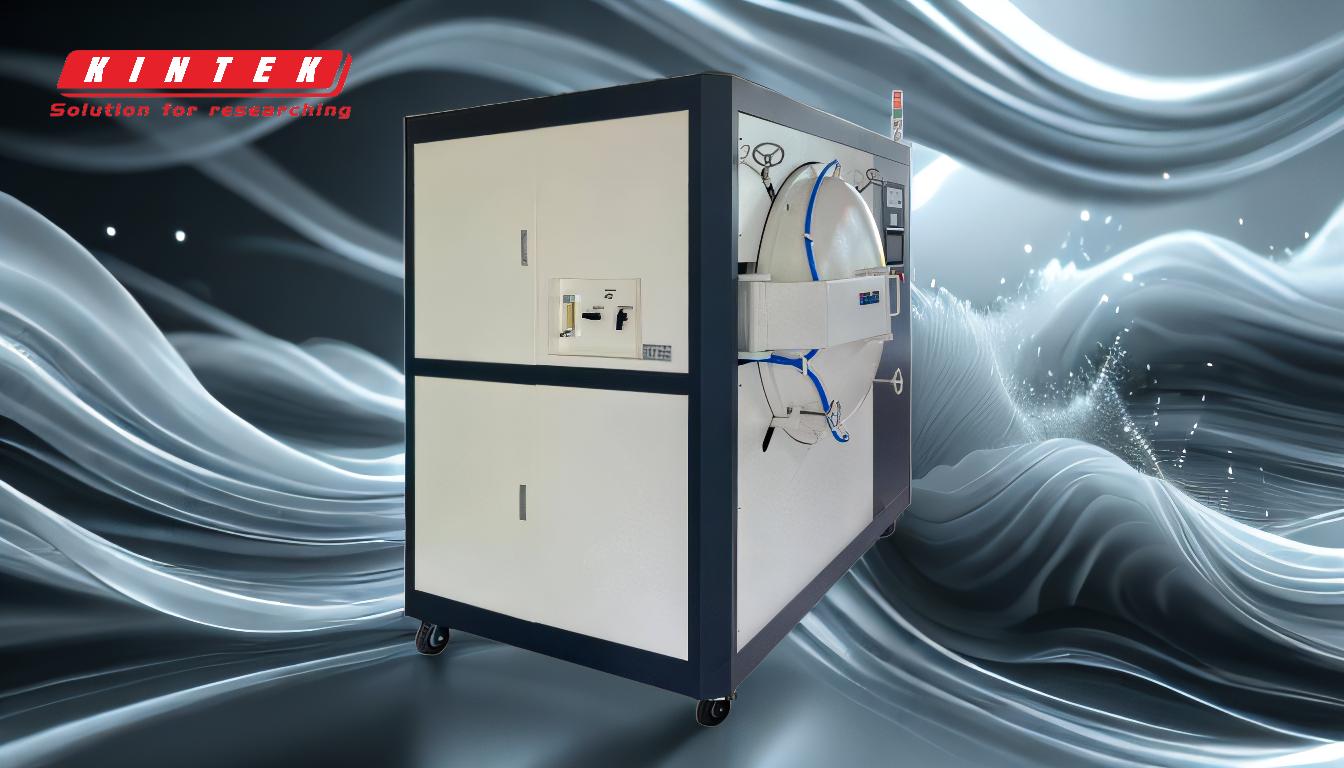
-
ろう付けとは何ですか?またその仕組みは何ですか?
- ろう付けは、金属フィラーをその融点以上に加熱し、毛細管現象によって 2 つ以上の密着した部品間に分散させる金属接合プロセスです。溶加材が接合部に流れ込んで凝固し、母材金属を溶かすことなく強力な接合を形成します。
- このプロセスは、熱応力や冶金学的不適合性などの溶接の問題を回避できるため、異種金属の接合に最適です。
-
異種金属の適合性
- ろう付けでは、融点、熱膨張率、冶金学的特性が異なる金属を接合できます。たとえば、銅と鋼、またはアルミニウムとステンレス鋼はうまくろう付けできます。
- 重要なのは、両方の母材と互換性があり、脆化や腐食を引き起こすことなく強力な結合を形成できる溶加材を選択することです。
-
適切な溶加材の選択
- 溶加材はベース金属よりも融点が低く、表面を効果的に濡らす必要があります。一般的な溶加材には、銀ベースの合金、銅ベースの合金、アルミニウムベースの合金などがあります。
- たとえば、銀ベースのフィラーはステンレス鋼と銅の接合によく使用されますが、アルミニウム - シリコン合金はアルミニウム部品のろう付けに適しています。
-
表面処理
- ろう付けを成功させるには、適切な表面処理が重要です。フィラーメタルの良好な濡れと接着を確保するには、表面は清潔で、酸化物、油、汚染物質が存在しない必要があります。
- 表面を準備するには、機械的洗浄、化学的洗浄、フラックス塗布などの技術が一般的に使用されます。
-
ろう付け環境とろう付け技術
- ろう付け環境は、酸化や汚染を防ぐために管理する必要があります。これは、フラックス、不活性ガス、または真空ろう付けを使用することで実現できます。
- 一般的なろう付け技術には、トーチろう付け、炉ろう付け、高周波ろう付けがあり、それぞれ特定の用途や材料に適しています。
-
異種金属ろう付けのメリット
- ろう付けにより接合部の熱歪みが最小限に抑えられるため、精密部品に適しています。
- これにより、溶接が困難または不可能な複雑な形状や異種材料の接合が可能になります。
- このプロセスは他の接合方法と比べて比較的速く、費用対効果が高くなります。
-
課題と考慮事項
- 課題の 1 つは、接合部を弱める可能性のあるフィラー メタルがいずれの母材とも悪影響を及ぼさないようにすることです。
- 冷却中の応力亀裂を避けるために、金属間の熱膨張の違いを考慮する必要があります。
- 適切な毛細管作用と強度を確保するには、適切なジョイント設計が不可欠です。
-
異種金属ろう付けの用途
- ろう付けは、自動車、航空宇宙、エレクトロニクス、HVAC などの業界で、異なる金属で作られたコンポーネントを接合するために広く使用されています。
- 例としては、冷凍システムにおける銅パイプとスチール継手の接合や、電子機器におけるアルミニウム ヒートシンクとステンレス鋼ハウジングの接合などが挙げられます。
これらの重要なポイントを理解することで、機器や消耗品の購入者は、特定の用途における異種金属のろう付けの実現可能性と要件について情報に基づいた決定を下すことができます。
概要表:
重要な側面 | 詳細 |
---|---|
プロセス | 溶加材を使用し、母材を溶かさずに金属を接合します。 |
互換性 | 融点、熱膨張、特性が異なる金属に最適です。 |
フィラーメタル | 接合される金属に応じて、銀、銅、またはアルミニウムベースの合金。 |
表面処理 | 酸化物、油、汚染物質を洗浄して除去し、接着力を向上させます。 |
ろう付け技術 | 特定のニーズに合わせてトーチろう付け、炉ろう付け、高周波ろう付けを行います。 |
利点 | 熱歪みが最小限に抑えられ、コスト効率が高く、複雑な形状に適しています。 |
アプリケーション | 自動車、航空宇宙、エレクトロニクス、HVAC 産業。 |
異種金属のろう付けについてサポートが必要ですか? 今すぐ専門家にお問い合わせください カスタマイズされたソリューションを実現します。