冷間静水圧プレスの基礎
冷間静水圧プレス (CIP) の定義と目的
冷間静水圧プレス (CIP) は、全方向から均一な圧力を加えて粉末を圧縮することによって材料を加工する方法です。このプロセスは、密閉された流体に加えられた圧力が全方向に均等に伝達されるというパスカルの法則に基づいています。
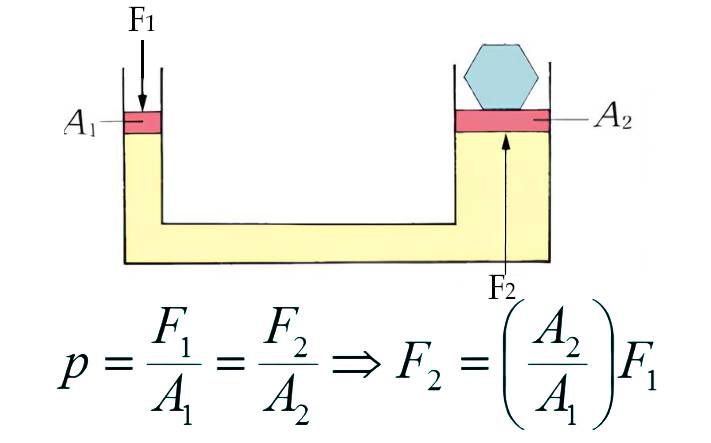
CIP では、粉末をエラストマー型に封入し、液体圧力を加えて圧縮します。その結果、非常に緻密な固体材料が得られます。 CIP は、プラスチック、グラファイト、セラミック、粉末冶金、スパッタリング ターゲットなどの幅広い材料に使用できます。
ウェットバッグとドライバッグ静水圧プレスの区別
冷間静水圧プレスには、ウェットバッグとドライバッグ静水圧プレスの 2 種類があります。
湿式バッグ静水圧プレスでは、粉末をゴム製のシースに封入し、粉末に圧力を均一に伝える液体に浸します。この方法は、少量生産、試作、研究開発に使用されます。
ドライバッグ静水圧プレスでは、エラストマー金型は静水圧プレスの不可欠な部分です。加えられる圧力は主に二軸であり、この方法は大量生産に適しています。
CIP における粉末の品質とツール設計の役割
粉末の品質と金型の設計は、冷間静水圧プレスの成功において重要な役割を果たします。
使用される粉末の品質は、最終製品の密度と強度に影響します。 CIP では、ワックス含有量が低いかまったく含まれていない粉末が一般的に使用されます。さらに、CIP で製造される部品の寸法公差は比較的大きいため、サイズと形状の制御は他のプレス方法ほど重要ではない場合があります。
CIP ではツーリングの設計も重要です。ウレタン、ゴム、ポリ塩化ビニルなどの素材から作られたエラストマー型が使用されます。金型の材料と設計の選択は、最終製品の精度と精度に影響を与えます。
静水圧プレスの概念とメリット
冷間静水圧プレスを含む等方圧プレスは、材料加工においていくつかの利点をもたらします。
大きな利点の 1 つは、一軸プレスと比較して均一な圧縮と高い成形能力を達成できることです。静水圧プレスは多方向から圧力を加えることで、より密度の高い高品質の部品を生成します。
静水圧プレスは、他の方法では圧縮できない複雑な形状の成形にも適しています。エラストマー金型を使用すると、材料を成形する際の柔軟性と多用途性が可能になります。
要約すると、冷間静水圧プレスは粉末を成形および圧縮するための貴重な方法です。均一性、形状能力、多用途性の点で独自の利点をもたらします。 CIP の基本とその応用を理解することで、企業はこのプロセスを活用して、さまざまな業界向けの高品質のコンポーネントを製造できます。
冷間静水圧プレスの種類
CIPのウェットバッグ技術
冷間静水圧プレス (CIP) は、機械加工または焼結の前に粉末材料を固体の均質な塊に圧縮するために使用される一般的な方法です。ウェットバッグ技術は CIP のサブタイプで、原料粉末を水またはその他の液体に浸した柔軟な型に充填します。次に、等方圧を適用して粉末を所望の形状に圧縮します。このプロセスにより、複雑な部品の製造が可能になり、最大 1 トンの重さのタングステンインゴットのプレスにも使用できます。
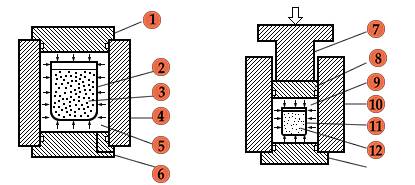
ドライバッグプレスとその応用
CIP の別のサブタイプは、単純な形状に使用されるドライバッグ プレスです。このプロセスでは、粉末が充填された金型が密閉され、金型と圧力容器の間で圧縮が発生します。ドライバッグプレスは、比較的単純な形状の大量生産に適しており、自動化して効率を高めることができます。

CIPと一軸プレスによる複雑形状製造の比較
冷間静水圧プレス (CIP) と一軸金型プレスを比較すると、CIP の方がより複雑な形状の製造が可能であることが明らかです。一方、一軸プレスは、円柱や四角形など、寸法が決まった単純な形状のプレスに適しています。 CIP は形状とサイズの柔軟性が高く、より長いアスペクト比の生成と粉末の圧縮の改善が可能になります。さらに、CIP は一軸プレスのようなワックス結合剤を必要としないため、脱ワックス操作が不要になります。
一軸金型プレスと比較したCIPの利点
冷間静水圧プレス (CIP) には、単軸金型プレスと比べていくつかの利点があります。まず、CIP では単純な形状に限定される一軸金型プレスと比較して、より複雑な形状の製造が可能です。第二に、CIP は、より均一な製品特性、より高い均質性、および完成品寸法のより正確な制御を提供します。また、アスペクト比を長くし、粉末の密度を向上させ、さまざまな特性や形状の材料を処理できるようになります。さらに、CIP はサイクル時間を短縮し、生産性を向上させます。
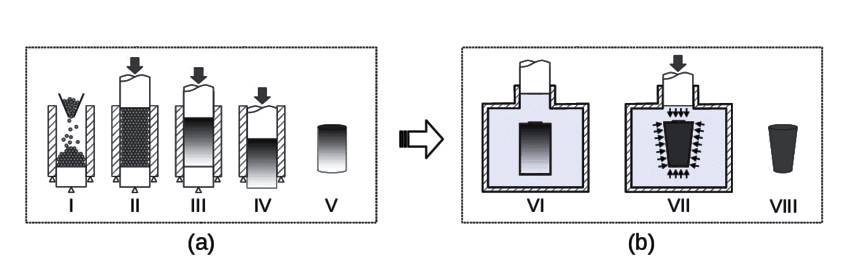
CIP と他の技術の比較
CIPと射出成形の比較
一軸ダイプレスの能力を超えた複雑な形状の部品が必要で、大量生産のスループットが必要な場合は、CIP (冷間静水圧プレス) と射出成形という 2 つの主要なオプションが使用されます。 CIP は、アルミナ セラミックを製造するための文献で報告された最初のハイテク方法です。 CIPは一軸金型プレスに比べ、より複雑な形状が可能であり、プレス圧力勾配が大幅に低減されるため、歪みやクラックが発生しにくくなります。ただし、CIP は工業的には射出成形ほど一般的ではなく、一般に非常に複雑な形状が必要で射出成形が現実的ではない場合にのみ使用されます。
アルミナセラミックスの製造におけるCIPの役割
CIPはアルミナセラミックスの製造において重要な役割を果たします。これにより、一軸ダイプレスなどの他の技術の能力を超えた複雑な形状の部品の製造が可能になります。アルミナ セラミックの CIP 原料には、単純に粉砕したバイエル アルミナ、粉砕および噴霧乾燥したバイエル アルミナ、またはハイテク噴霧乾燥した SolGel ナノ粉末を使用できます。アルミナ セラミックに対する CIP の主な利点としては、より複雑な形状を製造できること、プレス圧力勾配の低減、少量生産で複雑な部品の金型コストが低いこと、サイズ制限がないこと、加工サイクル時間が短いことが挙げられます。
スパークプラグ絶縁体の製造におけるCIPの使用
スパークプラグ絶縁体は、CIP を使用して製造されるセラミック部品の中で世界最大の生産量を誇ります。年間約 30 億個のスパーク プラグ絶縁体が CIP 処理されます。スパーク プラグ絶縁体の製造における CIP の使用は、大量生産と複雑な形状に対応できる能力を示しています。 CIP はスパーク プラグ業界の主力であり、複雑な形状や大量生産に最適な比較的低コストのプロセスです。
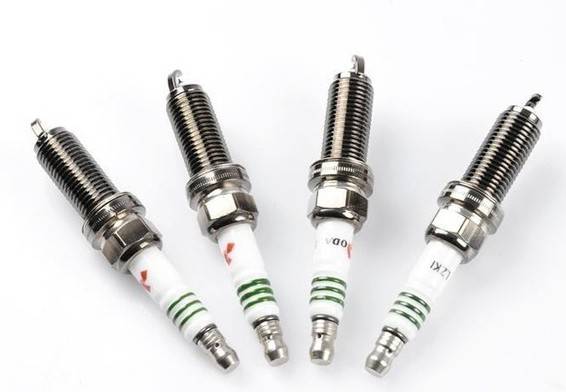
CIP原料の種類
CIPによるアルミナセラミックスの製造では、さまざまな種類の原料を使用できます。一般的に使用される原料には、単純に粉砕されたバイエル アルミナ、粉砕および噴霧乾燥されたバイエル アルミナ、およびまれにハイテク噴霧乾燥された SolGel ナノ粉末が含まれます。原料の選択は、製造されるセラミック部品の特定の要件によって異なります。 CIP 原料には優れた流動性が必要ですが、これは通常、噴霧乾燥または充填時の金型の振動によって達成されます。
CIP の利点:
- 一軸金型プレスに比べ、より複雑な形状が可能
- プレスの圧力勾配が大幅に軽減され、歪みや割れが発生しにくくなります。
- 金型コストが低く、少量生産の複雑な部品に最適
- サイズ制限なし、非常に大きなコンポーネントに適しています
- 処理サイクル時間が短く、乾燥やバインダーのバーンアウトが不要
CIP の欠点:
- 金型圧縮と比較して寸法制御が制限される
- 形状の複雑さは一軸金型プレスより優れていますが、粉末射出成形 (PIM) には劣ります。
- CIP 用の粉末には優れた流動性が必要であり、多くの場合スプレー乾燥によって実現されます。
- 限られた船舶の能力と容量
- 金型圧縮と比較して生産率が低い比較的手動のプロセス
CIP は、高性能金属コンポーネントの製造にいくつかの利点をもたらすソリッドステート プロセスです。これにより、均一な微細構造、形状の複雑さ、低い工具コスト、プロセスの拡張性、および材料の無駄を最小限に抑えてニアネットシェイプの部品を製造できる可能性が得られます。ただし、特定の種類の粉末の処理に限定されること、容器の能力と容量が限定されること、硬いツールを使用するプロセスと比較してより多くの後処理が必要になることなどの制限もあります。これらの制限にもかかわらず、CIP は依然として先進セラミックスの大量生産や複雑な形状の部品の生産にとって貴重な技術です。
冷間静水圧プレスのプロセス
CIPにおける均一プレスの工程
冷間静水圧プレス (CIP) は、エラストマー金型に封入された粉末を圧縮することによって材料を加工する方法です。次に、金型に均一に液体圧力がかかり、粉末が非常に緻密な固体に圧縮されます。このプロセスにより、圧力が全方向に均一に加えられるため、均質な最終製品が得られます。 CIP は、プラスチック、グラファイト、セラミック、粉末冶金などのさまざまな材料に使用できます。
CIP用のソフトバッグやモールドの使用
CIPでは、粉末を封入するためにエラストマーモールドまたはソフトバッグが使用されます。この金型は変形抵抗が低いため、圧力がかかると容易に圧縮されます。柔らかいバッグまたは金型を使用すると、圧力が粉末全体に均一に分散され、均一でコンパクトな最終製品が得られます。
ポストCIPの概念
CIP処理後、成形体にはポストCIP処理が施される。この処理には、望ましい最終強度と特性を達成するためのさらなる処理または焼結が含まれます。 CIP 後の処理は、処理される特定の材料によって異なる場合があります。
CIPにおけるオイルチャンバーの役割
CIPでは、圧力媒体としてオイルチャンバーが使用されます。オイルチャンバーはエラストマーモールドを囲み、液体圧力の適用を可能にします。オイル チャンバーは、加えられた圧力を金型に均一に伝達し、粉末を均一に圧縮するために重要な役割を果たします。
CIP の加圧および減圧サイクル
CIP プロセスには、加圧および減圧サイクルが含まれます。加圧サイクル中、液体圧力がエラストマー型に加えられ、粉末が圧縮されます。圧力は一定時間保持され、粉末が固化します。その後、減圧サイクルが開始され、圧力が解放され、成形体が回収できるようになります。
CIPの自動化と大規模導入
CIP は自動化でき、工業生産向けに大規模に実装できます。自動化により、加圧および減圧サイクルを正確に制御でき、一貫した高品質の結果が保証されます。 CIP の大規模導入により、大量の材料を効率的に処理できるため、さまざまな産業に適しています。
全体として、冷間静水圧プレスは材料を加工するための貴重な方法であり、均一な圧縮と高品質の最終製品を提供します。エラストマー金型、オイル チャンバー、加圧サイクルを使用することで、一貫した結果が保証され、大規模生産が可能になります。プラスチック、セラミック、粉末冶金のいずれの場合でも、CIP は材料処理のための信頼性が高く効率的なソリューションを提供します。
アルミナセラミックスのCIPのメリットとデメリット
一軸金型プレスや他のセラミック成形法と比較した CIP の利点
一軸金型プレスの能力を超えた複雑な形状の部品が必要で、大量生産のスループットが必要な場合、CIP (冷間静水圧プレス) と射出成形の 2 つの主なオプションが使用されます。 CIP は、アルミナ セラミックを製造するための文献で報告された最初のハイテク方法です。複雑な形状の先端セラミックや非常に大きなセラミック部品の大量生産によく使用されます。
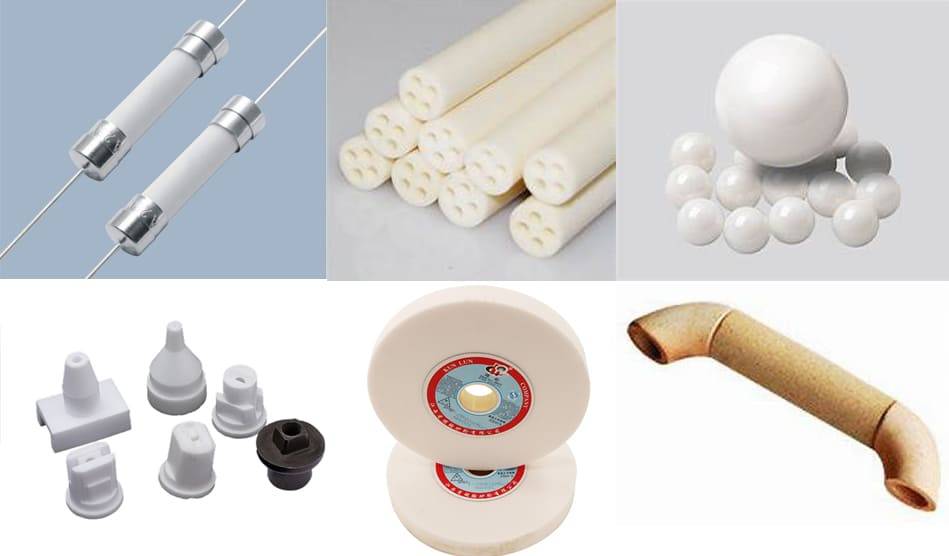
アルミナセラミックに対する CIP の主な利点のいくつかは次のとおりです。
より複雑な形状が可能: CIP では、一軸ダイプレスの形状能力を超える複雑な形状のコンポーネントの製造が可能になります。
プレスの圧力勾配を大幅に低減: CIPは三次元全方位から均一なプレスを施すことで歪みやクラックの発生を抑制します。
低い金型コスト: CIP は、必要な金型コストが低いため、少量生産の複雑な部品に最適です。
サイズ制限なし: CIP には、プレスチャンバーの制限を除き、サイズ制限はありません。したがって、非常に大きなコンポーネント、特に複雑な形状のコンポーネントに最適です。 1 トンを超える重量のコンポーネントは CIP 処理されています。
短い処理サイクル時間: CIP では乾燥やバインダーの燃え尽きが必要ないため、処理サイクル時間が短縮されます。
セラミックスの CIP の限界と課題
CIP にはその利点があるにもかかわらず、セラミックスに対していくつかの制限と課題もあります。
寸法制御の制限: CIP では、非常に薄く均一な厚さのエラストマー モールドまたはシースが必要となるため、高精度を達成することが困難です。
形状の複雑さは PIM より劣る: CIP は一軸金型プレスと比較して形状の複雑さは優れていますが、形状の複雑さの点では依然として粉末射出成形 (PIM) には劣ります。
粉末の流動性要件: CIP で使用される粉末には優れた流動性が必要です。これは通常、噴霧乾燥や充填中の金型の振動を意味します。
比較的手動: CIP は比較的手動のプロセスであり、慎重な取り扱いと制御が必要です。
特定の粉体の処理に限定される: CIPは流動性に優れた粉体の処理に限定されるため、使用できる材料の範囲が制限される場合があります。
限られた容器の能力と容量: CIP はプレス チャンバーの能力と容量によって制限され、それによって製造できるコンポーネントのサイズが制限される場合があります。
これらの制限にもかかわらず、CIP は依然として、複雑な形状または大量生産の先端セラミックの大量生産に一般的に使用される方法です。特にアルミナ業界で広く普及しており、スパークプラグ業界の主力であり、形状の複雑さや大量生産に最適な比較的低コストのプロセスです。スパーク プラグ絶縁体に加えて、一般的に CIP されるその他の部品には、特殊摩耗部品 (ポンプや繊維産業で使用される部品など) や電気絶縁体などがあります。
全体として、CIP はアルミナ セラミックの製造に独自の利点を提供し、圧力勾配を低減し、加工サイクル時間を短縮して複雑な形状の部品を製造できるようにします。ただし、特定の用途に適切なセラミック成形方法を決定する際には、制限された寸法制御や粉末流動性要件などの制限と課題を考慮することが重要です。
冷間静水圧プレスの応用
先端セラミックス製造における CIP の一般的な使用法
冷間静水圧プレス (CIP) は、金属およびセラミック部品の製造に使用される粉末ベースのニアネットシェイプ技術です。 CIP はセラミックの加工に一般的に使用されてきましたが、最近の加工能力と粉末冶金の発展により、高性能金属部品の製造にも CIP が使用されることが増えています。
固体処理、均一な微細構造、形状の複雑さ、低い工具コスト、プロセスの拡張性などの利点により、CIP は金属の実行可能な処理ルートとなっています。さらに、材料の無駄を最小限に抑えてニアネットシェイプの部品を製造できる可能性により、このプロセスは航空宇宙や自動車などのニッチな用途でより広く受け入れられるようになりました。
冷間静水圧プレスの一般的な用途には、セラミック粉末、グラファイト、耐火材料、電気絶縁体の固化、および高度なセラミックの圧縮が含まれます。窒化ケイ素、炭化ケイ素、窒化ホウ素、炭化ホウ素、ホウ化チタン、スピネルなどの材料が一般的に使用されます。この技術は、スパッタリング ターゲットの圧縮、エンジンのシリンダー摩耗を軽減するために使用されるバルブ部品のコーティング、通信、エレクトロニクス、航空宇宙、自動車産業などの新しい用途にも拡大しています。
スパークプラグ業界とアルミナ業界におけるCIPの役割
CIP はスパークプラグ業界とアルミナ業界で重要な役割を果たしています。スパークプラグ業界では、CIP は複雑な形状の先進セラミックや非常に大きなセラミック部品の大量生産に一般的に使用されています。スパークプラグの絶縁体だけでなく、ポンプや繊維産業の特殊摩耗部品、電気絶縁体にも使用されています。
アルミナ業界では、CIP がスパーク プラグ業界の主力であると考えられています。これは比較的低コストのプロセスであり、複雑な形状や大規模な生産に最適です。スパークプラグを効率よく製造するためには欠かせない技術です。
全体として、冷間静水圧プレスは、さまざまな業界で高性能部品を製造するための実績のあるプロセスです。セラミックの高密度を達成できる能力と、セラミックと金属の両方の加工における多用途性により、この技術はメーカーにとって貴重な技術となっています。
他の圧縮技術との比較
冷間静水圧プレスと熱間静水圧プレス: 比較の概要
材料加工の分野では、冷間等方圧プレス (CIP) と熱間等方圧プレス (HIP) という 2 つの強力な技術が際立っています。どちらの方法も材料特性を向上させるという共通の目標を持っていますが、異なる条件下でそれを行うため、それぞれに独自の利点があります。ここでは、冷間等方圧プレスと熱間等方圧プレスの比較概要を示します。
冷間等方圧プレス (CIP):冷間等方圧プレスは、冷間等方圧圧縮とも呼ばれ、材料にすべての面から均一な圧力をかけることを伴います。これは、材料を高圧の流体媒体に浸し、油圧を加えることで実現されます。 CIP は、粉末材料の成形と強化、複雑な形状の作成、および高いグリーン密度の達成に特に効果的です。
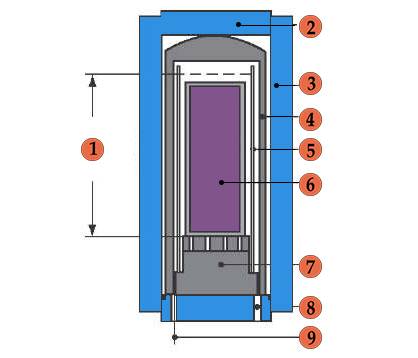
熱間静水圧プレス (HIP):熱間静水圧プレス (HIP) は、高温と高圧を使用して金属またはセラミック製品に全方向に均等な圧力を加え、部品を焼結して緻密化するプロセス技術です。世界の熱処理業界を代表する北米熱処理協会は 2021 年に、熱間静水圧プレス、水素燃焼技術、積層造形技術を 3 つの最も有望な技術およびプロセスとしてランク付けしました。
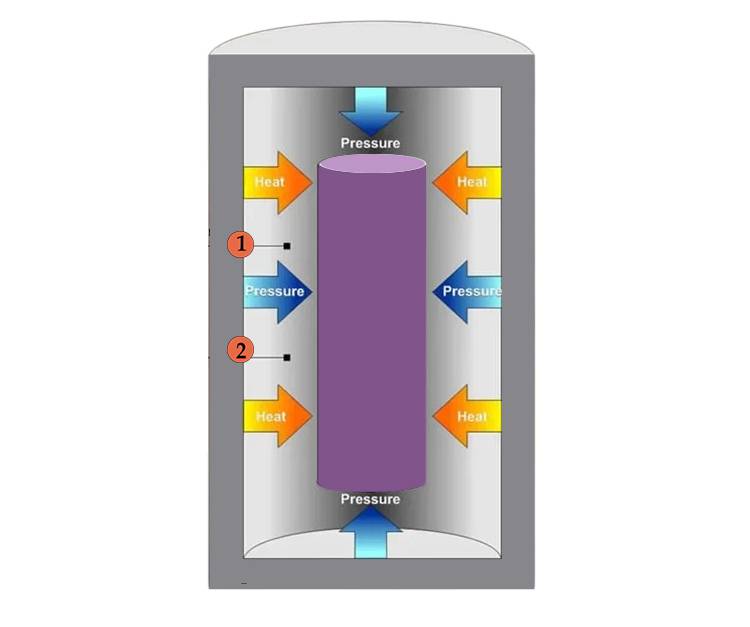
熱間静水圧プレス装置は、高圧容器、加熱炉、コンプレッサー、真空ポンプ、貯蔵タンク、冷却システム、コンピュータ制御システムで構成されており、高圧容器が装置全体のキーデバイスとなります。
この観点から、進歩する技術に対応し、金属やセラミック基板だけでなくポリマーベースの基板の技術要件を満たす代替方法の探索により、研究者は新しい技術や方法に取り組むようになりました。指摘されている「セラミック粉末エアロゾルデポジション法」は、追加の高温熱処理または焼結ステップを必要とするだけでなく、大面積への均一かつ連続的な適用性も必要とします。半導体材料技術の研究者にとって年々注目を集めるトレンドとなっている。これらすべての利点の結果、エアロゾルデポジション法は、その技術的詳細と適用可能性の両方の点で検討する価値があると考えられており、この分野でまだ開発の余地がある未使用の技術であるため、ニーズを満たす可能性があります新世代の半導体技術で。
高密度に圧縮されたアルミニウムと鉄を除いて、静水圧プレスを使用することには明確な利点があります。高密度では、金型と静水圧圧縮の両方で、鉄とアルミニウムの粉末と同様の生密度が得られます。ただし、一定のせん断応力を持つアルミニウムなどの材料の場合、半径方向の圧力は軸方向の圧力とほぼ等しくなり、静水圧分布に近づきます。ただし、降伏応力がせん断面の法線応力の関数である銅のような材料の場合、半径方向の圧力は軸方向の圧力よりも低いままです。冷間プレスされた成形体内の圧力分布は静水圧になる可能性がありますが、おそらく、密度分布が同様に均一である場合に限り、圧力と密度の関係は静水圧成形の場合と同じになるはずです。
要約すると、冷間等方圧プレスと熱間等方圧プレスは材料加工に対する異なるアプローチであり、それぞれに独自の利点があります。どちらを選択するかは、プロジェクトの具体的な目標と、関連する材料の特性によって異なります。
無料相談はお問い合わせください
KINTEK LAB SOLUTION の製品とサービスは、世界中のお客様に認められています。弊社スタッフがどんなご質問にも喜んで対応させていただきます。無料相談にお問い合わせいただき、製品スペシャリストにご相談いただき、アプリケーションのニーズに最適なソリューションを見つけてください。