表面硬化は、より柔らかく延性のあるコアを維持しながら、金属の外面の硬度を高めるために使用されるプロセスです。この技術は、コンポーネントの耐摩耗性、疲労強度、全体的な耐久性を向上させるために不可欠です。表面硬化には、熱処理、化学処理、機械的処理など、さまざまな方法や製品が使用されます。どの方法を選択するかは、材料、用途、および必要な特性によって異なります。
重要なポイントの説明:
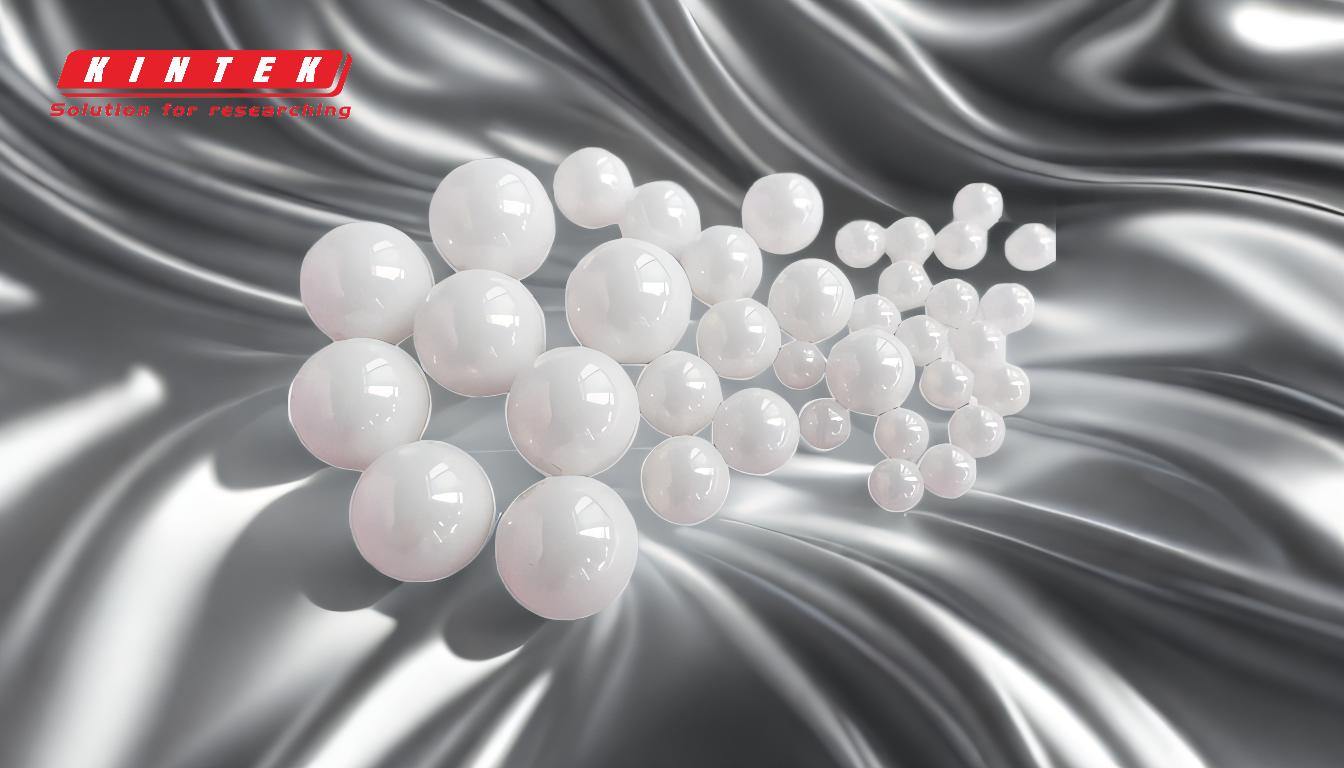
-
熱処理方法:
- 高周波焼き入れ :電磁誘導により金属表面を加熱し、急速急冷する方法です。高い表面硬度が要求されるギアやシャフトなどによく使用されます。
- 火炎硬化 :金属表面を酸素アセチレン炎で加熱し、急冷する方法です。大型部品や不規則な形状の部品に適しています。
- レーザー硬化: 集束レーザー ビームを使用して表面を加熱し、その後バルク材料への急速な熱放散により自己消火します。この方法では、精度が高く、歪みが最小限に抑えられます。
-
化学処理方法:
- 浸炭: このプロセスでは、炭素が豊富な環境で低炭素鋼を加熱することにより、低炭素鋼の表層に炭素を導入します。炭素が表面に拡散し、焼入れ後の硬度が増加します。
- 窒化処理: この方法では金属の表面に窒素が導入され、硬い窒化物が形成されます。低温で実行されるため、歪みが軽減され、完成したコンポーネントに適したものになります。
- シアン化: 金属を溶融シアン化物浴中で加熱し、炭素と窒素を表面に拡散させるプロセス。環境への懸念からあまり一般的には使用されていません。
-
機械的方法:
- ショットピーニング: これには、小さな球状メディア (ショット) を表面に衝突させて圧縮応力を誘発し、耐疲労性と表面硬度を向上させます。
- ローラーバニシング: 硬化したローラーを表面に押し当てて平滑化し、硬化させる冷間加工プロセスです。円筒部品の表面仕上げや硬度を向上させるためによく使用されます。
-
製品と材料:
- スチール: 低炭素鋼、合金鋼、工具鋼などのさまざまな鋼種は、一般的に上記の方法を使用して表面硬化されます。
- 鋳鉄: ダクタイル鋳鉄などの特定の種類の鋳鉄は、耐摩耗性を向上させるために表面硬化することもできます。
- 非鉄合金: チタンやアルミニウムなどの一部の非鉄合金は、表面特性を向上させるために窒化や陽極酸化などの表面硬化プロセスを受けることができます。
-
アプリケーション:
- 自動車産業: ギア、クランクシャフト、カムシャフトなどの部品は、高い応力や摩耗に耐えるために表面硬化が施されることがよくあります。
- 航空宇宙産業: 着陸装置やタービンブレードなどの重要な部品は、耐久性と安全性を確保するために表面硬化されています。
- 工具と機械: 切削工具、金型、金型は、寿命を延ばし、精度を維持するために表面硬化されています。
-
表面硬化のメリット:
- 耐摩耗性の向上: 硬化した表面は摩耗や磨耗に耐え、コンポーネントの寿命を延ばします。
- 疲労強度の向上: 表面硬化により圧縮応力が導入され、疲労破壊に対する耐性が向上します。
- ダクタイルコア: より柔らかいコアが靭性と延性を維持し、脆性破壊を防ぎます。
-
選択に関する考慮事項:
- 材質の適合性: すべての材料がすべての表面硬化方法に適しているわけではありません。選択は基材とその特性によって異なります。
- コンポーネントの形状: コンポーネントの形状とサイズは、硬化方法の選択に影響します。複雑な形状では、レーザー硬化などのより正確な方法が必要になる場合があります。
- コストと効率: 高周波焼入れなどの一部の方法は大量生産にコスト効率が高く、レーザー焼入れなどの他の方法はより高価ですが、より高い精度を提供します。
結論として、表面硬化には、金属の表面特性を向上させるために調整されたさまざまな方法と製品が含まれます。適切な方法の選択は、材料、用途、および望ましい結果に応じて決まり、コンポーネントが動作環境の要求に耐えられることが保証されます。
概要表:
カテゴリ | 方法/例 |
---|---|
熱処理 | 高周波焼入れ、火炎焼入れ、レーザー焼入れ |
化学処理 | 浸炭、窒化、シアン化処理 |
機械的方法 | ショットピーニング、ローラーバニシング |
材料 | 鋼、鋳鉄、非鉄合金 |
アプリケーション | 自動車、航空宇宙、工具、機械 |
利点 | 耐摩耗性の向上、疲労強度の向上、ダクタイルコア |
選択要素 | 材料の互換性、コンポーネントの形状、コストと効率 |
お客様のニーズに最適な表面硬化ソリューションを見つけてください— 今すぐ専門家にお問い合わせください !