等方性黒鉛製造工程は、コークスやピッチのような原料を均一な特性を持つ高性能黒鉛に変える多段階の手順である。主な工程には、コークス製造、粉砕、混練、静水圧成形、炭化、ピッチ含浸、黒鉛化、および機械加工や精製などの後処理段階が含まれる。重要な工程である静水圧成形では、フレキシブルな金型内で粉末カーボンに均一に高圧をかけ、対称的で緻密な構造を実現する。出来上がったグラファイトは、卓越した耐熱性、耐薬品性、高い電気伝導性、熱伝導性を示し、機械加工が容易であるため、半導体、航空宇宙、冶金などの産業における要求の厳しい用途に適している。
キーポイントの説明
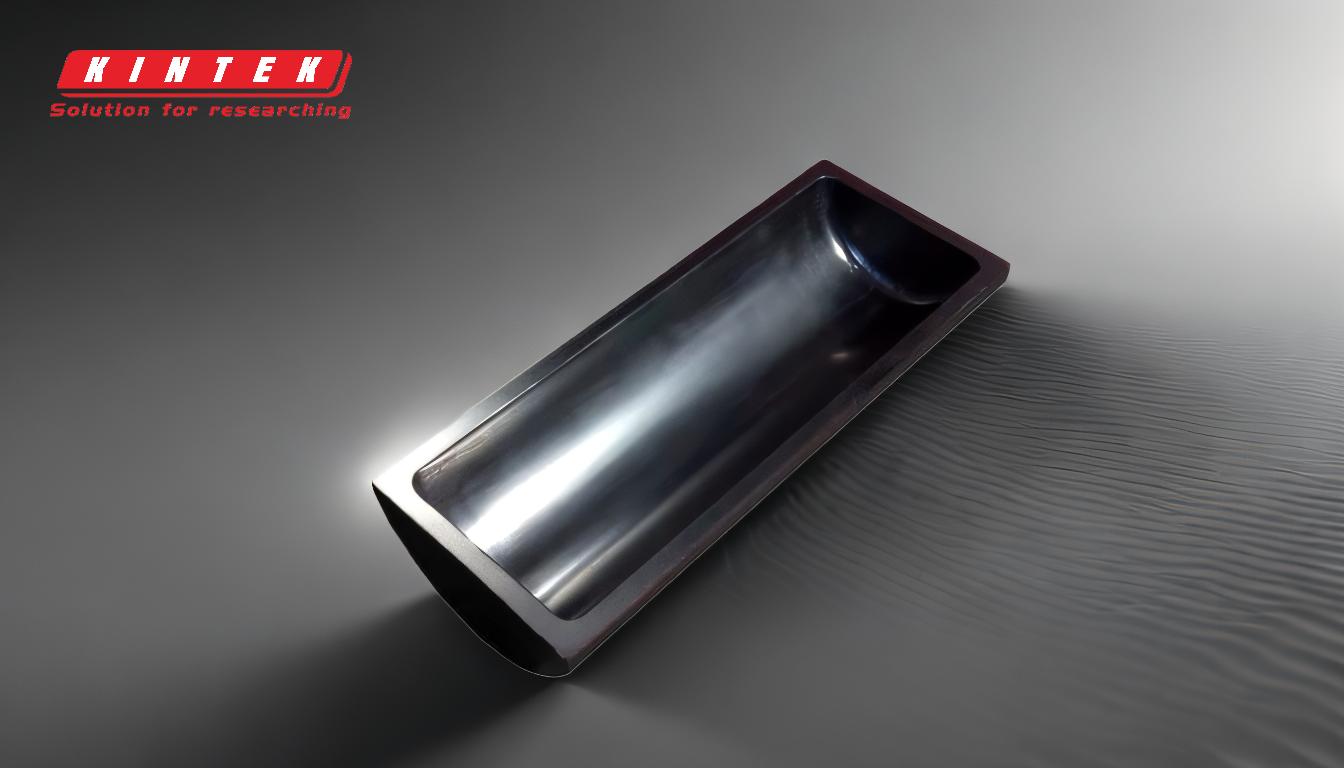
-
原材料の準備:
- このプロセスは、石炭や石油から得られる炭素を多く含む物質であるコークスの製造から始まる。このコークスを細かく粉砕する。
- 結合剤であるピッチは、粉砕されたコークスと混合され、均質な混合物を形成する。この工程により、炭素粒子が均一に分散され、結合される。
-
静水圧成形:
- 混合物はフレキシブルな金型に装填され、漏れを防ぐために密閉される。
- 通常150MPa以上の高圧が、圧力容器内の液体媒体を介して均一に加えられる。この アイソスタティック成形 このプロセスにより、粒が対称的に配置され、均一に分散され、緻密で均一な構造になります。
- プレス後、圧縮された粉末体は金型から取り出され、次の加工に備える。
-
炭化:
- 成形体は、酸素のない環境で800~1000℃前後に加熱される。この工程で揮発性成分が除去され、ピッチが固体炭素マトリックスに変換され、構造が強化されます。
-
ピッチ含浸:
- 密度と機械的特性をさらに高めるため、炭化体にピッチを含浸させる。この工程は、残存する気孔を埋め、材料の均一性を向上させる。
-
黒鉛化:
- 含浸体は、黒鉛化炉で超高温(2500~2800℃)で熱処理される。この工程により、アモルファスカーボンが結晶性グラファイトに変化し、優れた熱伝導性と電気伝導性が付与される。
-
後処理:
- 検査:黒鉛ブロックの欠陥と均一性を検査する。
- 機械加工:精密な形状やサイズに加工しやすく、さまざまな用途に使用できる。
- 精製:高純度グラファイトは、不純物を除去することによって達成され、多くの場合、不純物は5ppm以下のレベルまで減少する。
- 表面処理:黒鉛の表面特性を向上させたり、特定の用途に使用するために、追加の処理を施すことができる。
-
等方性黒鉛の特性:
- 高い耐熱性と耐薬品性:過酷な環境に適しています。
- 優れた耐熱衝撃性:急激な温度変化にもひび割れせずに耐える。
- 高い電気伝導性と熱伝導性:効率的な熱と電気の伝達を必要とする用途に最適。
- 温度による強度の増加:高温条件下でも優れた性能を発揮。
- 加工のしやすさ:複雑な部品の精密加工を可能にします。
-
用途:
- 等方性黒鉛は、その優れた特性と汎用性により、半導体、航空宇宙、冶金、エネルギーなどの産業で広く使用されています。
等方性黒鉛の製造工程は、高度で綿密に管理された手順であり、最終製品が高度な産業用途の厳しい要件を満たすことを保証している。
総括表
ステップ | 説明 |
---|---|
原料準備 | コークスの製造、粉砕、ピッチとの混合による均質な混合。 |
静水圧成形 | フレキシブルな金型で高圧成形し、緻密で均一な構造を得る。 |
炭化 | 800~1000℃に加熱して揮発分を除去し、炭素マトリックスを強化する。 |
ピッチ含浸 | ピッチを含浸させ、密度と均一性を高める。 |
黒鉛化 | 2500~2800℃で熱処理し、炭素を結晶性黒鉛に変化させる。 |
後処理 | 検査、機械加工、純化、最終使用のための表面処理。 |
主な特性 | 高い耐熱性/耐薬品性、優れた導電性、加工の容易さ。 |
用途 | 半導体、航空宇宙、冶金、エネルギー産業。 |
等方性黒鉛がお客様の産業用途をどのように向上させるかをご覧ください。 今すぐご連絡ください までご連絡ください!