熱蒸発とスパッタリングは、物理的気相成長(PVD)技術として広く使用されている2つの手法であり、それぞれに明確なメカニズム、利点、限界がある。熱蒸発は、材料を気化点まで加熱し、強固な蒸気流を形成することで、高い蒸着速度と短い運転時間を可能にします。これとは対照的に、スパッタリングでは、ターゲット材料に高エネルギーイオンを衝突させ、単一原子またはクラスターを放出させる。これらの方法のどちらを選択するかは、希望する蒸着速度、材料の種類、基板の互換性、アプリケーションの要件などの要因によって決まります。
キーポイントの説明
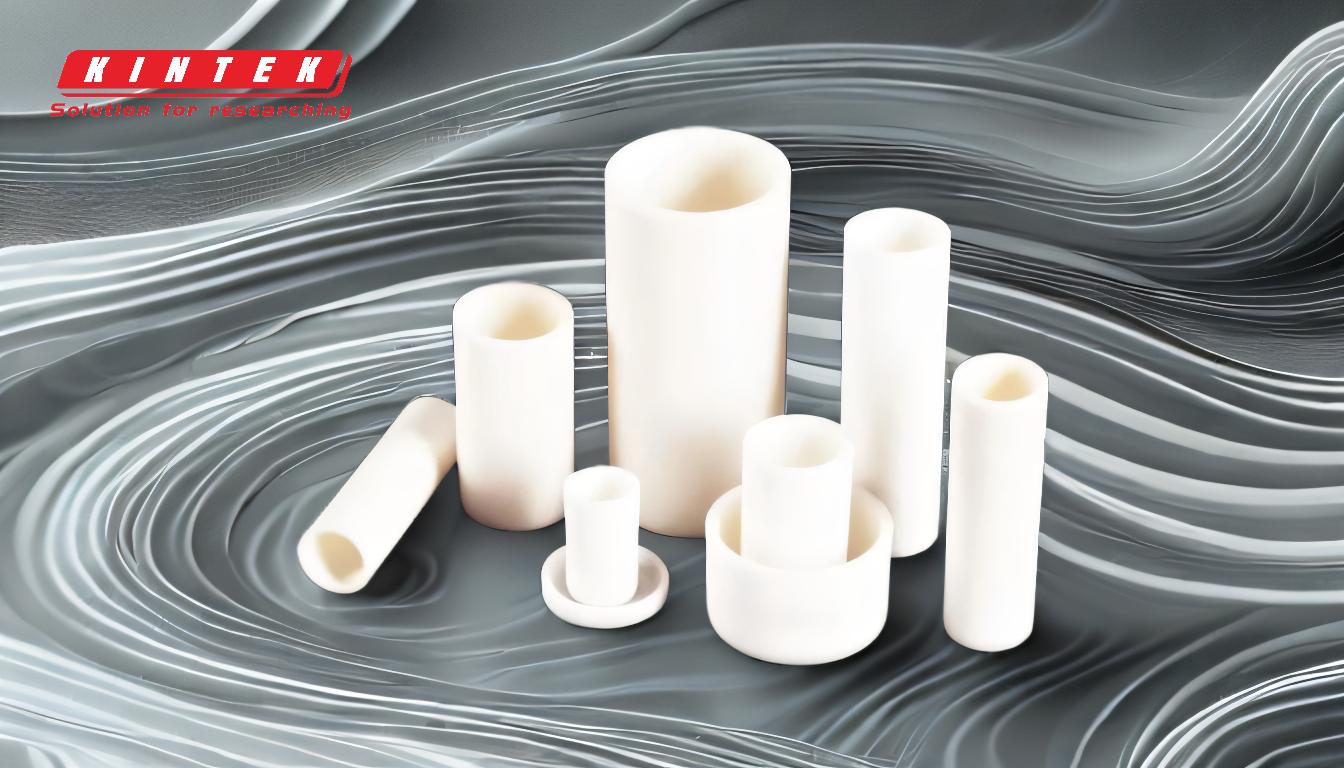
-
成膜のメカニズム:
- 熱蒸発:このプロセスでは、真空中で原料を気化するまで加熱する。その後、蒸気は基板上で凝縮し、薄膜を形成する。気化に必要な温度が高いため、この方法は比較的融点の低い材料に適している。
- スパッタリング:スパッタリングでは、真空チャンバー内でターゲット材料に高エネルギーイオン(通常はアルゴン)を衝突させる。この衝突によってターゲットから原子やクラスターがたたき落とされ、基板上に堆積する。このプロセスは熱に依存しないため、プラスチックや有機物のような熱に弱い基板を含む、より幅広い材料に適している。
-
蒸着速度:
- 熱蒸発:高い成膜速度で知られる熱蒸発法は、迅速なコーティングプロセスを必要とする用途に最適です。強固な蒸気流により、迅速な成膜が可能です。
- スパッタリング:一般に、スパッタリングは単原子または小さなクラスターを放出するため、成膜速度が低い。しかし、この遅いプロセスにより、均一性と密着性に優れた膜が得られることが多い。
-
材料適合性:
- 熱蒸発:分解せずに高温に耐えられる素材に限定される。このため、熱に弱い基板や融点の高い材料には適さない。
- スパッタリング:金属、合金、セラミック、さらにはプラスチックやガラスのような熱に弱い基材など、さまざまな材料を蒸着できる。プロセスに高温がないため、適用範囲が広がる。
-
フィルムの品質と接着性:
- 熱蒸発:成膜速度が速い反面、膜の均一性や密着性に欠けることがある。これは、精密な膜特性を必要とする用途では制約となる。
- スパッタリング:均一性、密着性、密度に優れた膜が得られる。このプロセスのエネルギッシュな性質は、蒸着された原子が基材と良好に結合することを保証し、高性能コーティングに適している。
-
色と美観のオプション:
- 熱蒸発:通常、アルミニウムのような素材本来の色に限定される。他の色を実現するには、スプレー塗装などの追加工程が必要になることが多い。
- スパッタリング:成膜プロセスを調整することで、より多様な色を提供する。そのため、装飾コーティングや特定の美的特性を必要とする用途に適しています。
-
プロセス温度:
- 熱蒸発:ソース材料を蒸発させるために高温を必要とするため、温度に敏感な基板では使用が制限されることがある。
- スパッタリング:低温で作動するため、プラスチック、有機物、ガラスなどのコーティングに適しており、ダメージを与える心配がない。
-
用途:
- 熱蒸発:光学コーティング、太陽電池、単純な金属膜の製造など、高い成膜速度が要求される用途でよく使用される。
- スパッタリング:半導体製造、装飾コーティング、機能性薄膜など、高品質で均一な膜と優れた接着性が要求される用途に適している。
これらの重要な違いを理解することで、機器や消耗品の購入者は、アプリケーションの特定の要件に基づいて情報に基づいた決定を下すことができ、最適な性能と費用対効果を確保することができます。
要約表
側面 | 熱蒸発 | スパッタリング |
---|---|---|
メカニズム | 真空中で物質を気化点まで加熱する。 | ターゲット材料に高エネルギーイオンを衝突させ、原子またはクラスターを放出させる。 |
蒸着速度 | 高い蒸着速度、迅速なコーティングプロセスに最適。 | 蒸着速度は低いが、均一性と密着性に優れる。 |
材料適合性 | 融点の低い材料に限定。熱に敏感な基板には適さない。 | 金属、合金、セラミック、感熱性材料に適合。 |
膜質 | スパッタリングに比べ、均一性と密着性に欠ける場合がある。 | 均一性、密着性、密度に優れた膜が得られる。 |
カラーオプション | 素材本来の色に限定。 | 装飾的、審美的な用途に、より多様な色を提供する。 |
プロセス温度 | 高温を必要とするため、熱に敏感な基材での使用が制限される。 | 低温で作動し、プラスチック、有機物、ガラスに適している。 |
用途 | 光学コーティング、太陽電池、単純金属膜 | 半導体製造、装飾コーティング、機能性薄膜。 |
お客様の用途に適したPVD技術の選択にお困りですか? 当社の専門家に今すぐご連絡ください にお問い合わせください!