PVD(Physical Vapor Deposition)とCVD(Chemical Vapor Deposition)は、基板を材料でコーティングするために使用される2つの著名な薄膜蒸着技術である。どちらの手法も表面特性を向上させることを目的としていますが、そのプロセス、操作条件、得られるコーティングは大きく異なります。PVDは、通常真空中で材料を物理的に気化させ、化学反応を起こさずに基材上に堆積させる。これに対してCVDは、気体状の前駆物質と基材との化学反応によって固体皮膜を形成する。PVDとCVDのどちらを選択するかは、希望するコーティングの特性、基材の材質、アプリケーションの要件などの要因によって決まる。PVDは、動作温度が低く、環境にやさしく、耐摩耗性に優れているため、しばしば好まれますが、CVDは、高温で緻密で均一なコーティングを行うことに優れています。
キーポイントの説明
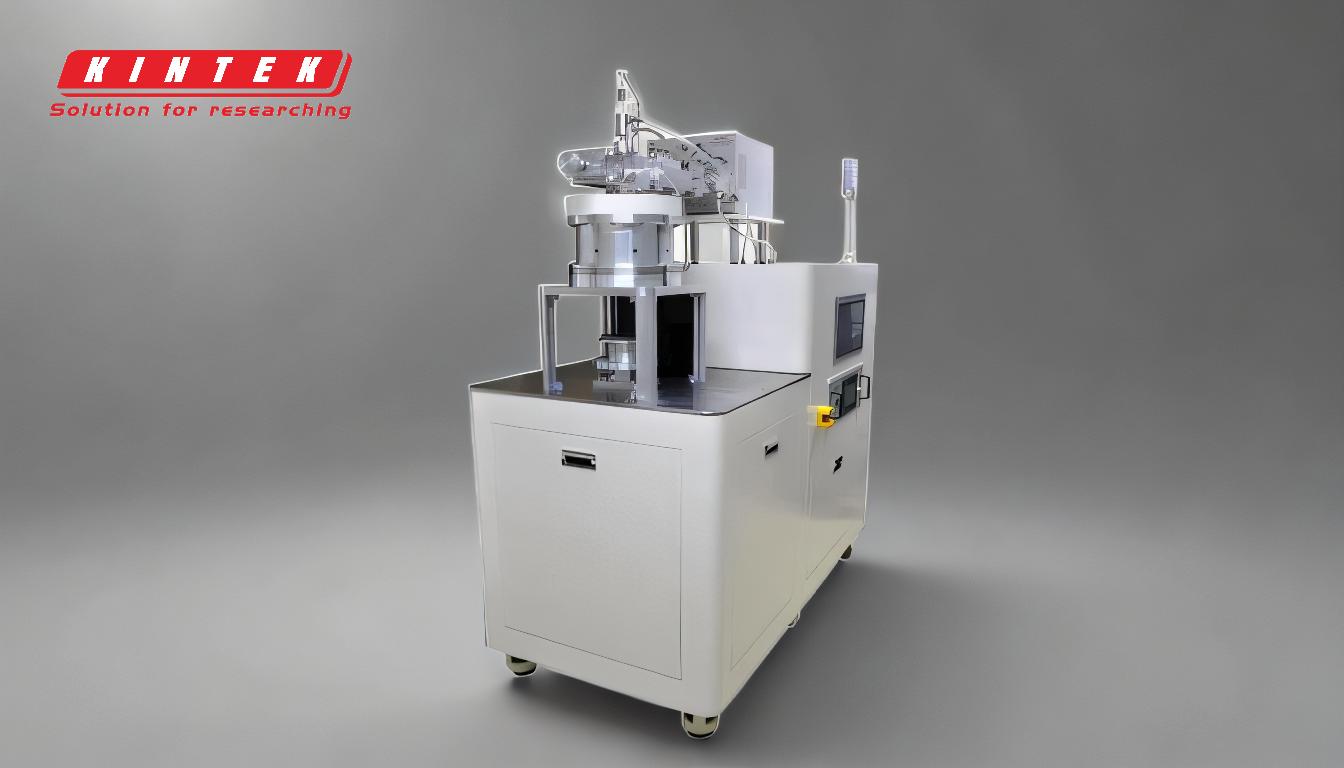
-
成膜メカニズム:
- PVD:スパッタリングや蒸着などの物理的プロセスにより、固体ソースから基板に材料を転写する。このプロセスはライン・オブ・サイト(line-of-sight)であり、材料は化学的相互作用なしに基板上に直接蒸着される。
- CVD:ガス状前駆体と基材表面の化学反応に依存する。反応により固体のコーティングが生成され、蒸着は多方向性であるため、複雑な形状をよりよくカバーすることができる。
-
使用温度:
- PVD:比較的低い温度、通常250℃~450℃で作動する。そのため、温度に敏感な基板に適している。
- CVD:450℃から1050℃の高温を必要とするため、素材によっては使用が制限されるが、より緻密で均一なコーティングが得られる。
-
コーティング材料:
- PVD:金属、合金、セラミックスなど、さまざまな材料の成膜が可能。汎用性が高く、硬くて耐摩耗性のコーティングを必要とする用途に適している。
- CVD:主にセラミックやポリマーの成膜に使用される。高純度で緻密なコーティングを必要とする用途に最適。
-
コーティング特性:
- PVD:高硬度、優れた耐摩耗性、低摩擦性を持つコーティングが得られる。CVDに比べコーティングの密度が低く、均一性に欠けるが、塗布が早い。
- CVD:密着性に優れ、より緻密で均一な塗膜が得られる。しかし、この工程は時間がかかり、引っ張り応力が発生するため、微細なクラックが発生する可能性がある。
-
用途:
- PVD:切削工具、自動車部品、装飾仕上げなど、耐摩耗性コーティングを必要とする産業でよく使用される。低温で使用できるため、温度に敏感な基材に適している。
- CVD:半導体製造、光学コーティング、高純度で緻密な膜を必要とする用途に広く使用されている。複雑な形状のコーティングが可能なため、複雑な部品に最適。
-
環境と経済性への配慮:
- PVD:有害な副産物が発生しないため環境に優しい。しかし、真空装置やエネルギー集約的なプロセスが必要なため、一般的に高価である。
- CVD:使用する前駆体によっては有害な副生成物を生成する可能性がある。大規模生産では費用対効果が高いが、動作温度が高く、化学物質の取り扱いが必要なため、運用が複雑になる可能性がある。
まとめると、PVDとCVDのどちらを選択するかは、希望するコーティング特性、基材、運用上の制約など、アプリケーションの具体的な要件によって決まる。PVDは、その汎用性、低温、優れた耐摩耗性で好まれることが多く、CVDは、複雑な形状に緻密で均一なコーティングを施す能力で好まれる。
総括表
側面 | PVD | CVD |
---|---|---|
成膜メカニズム | 物理プロセス(スパッタリング/蒸着)、ライン・オブ・サイト蒸着。 | ガス状前駆体と基板間の化学反応、多方向性。 |
使用温度 | 250℃~450℃、温度に敏感な基板に適している。 | 450℃~1050℃、緻密で均一なコーティングに最適。 |
コーティング材料 | 金属、合金、セラミックス | セラミックス、ポリマー |
コーティング特性 | 高硬度、耐摩耗性、低摩擦、密度が低い。 | 高密度、均一、優れた接着性、遅いプロセス。 |
用途 | 切削工具、自動車部品、装飾仕上げ | 半導体、光学コーティング、複雑な部品 |
環境への影響 | 環境に優しく、有害な副産物がない。 | 有害な副産物を生成する可能性があり、操作の複雑さが増す。 |
お客様のプロジェクトでPVDとCVDのどちらを選択するかお困りですか? 当社の専門家に今すぐご連絡ください をご利用ください!