CVD(化学気相成長法)とPVD(物理気相成長法)は、インサートに広く使用されている2つのコーティング技術で、それぞれ異なるプロセス、特性、用途を持っています。CVDは高温(800~1000℃)で化学反応を行い、より厚い膜(10~20μm)を成膜しますが、PVDは低温(250~500℃)で物理的気化を行い、より薄い超硬質膜(3~5μm)を成膜します。CVDコーティングはより緻密で均一だが、加工温度が高いため、引張応力や微細なクラックが発生する可能性がある。一方、PVDコーティングは圧縮応力を形成し、滑らかで耐久性のある表面を必要とする精密用途に最適です。CVDとPVDのどちらを選択するかは、コーティングの厚さ、使用温度、特定のアプリケーション要件などの要因によって決まります。
キーポイントの説明
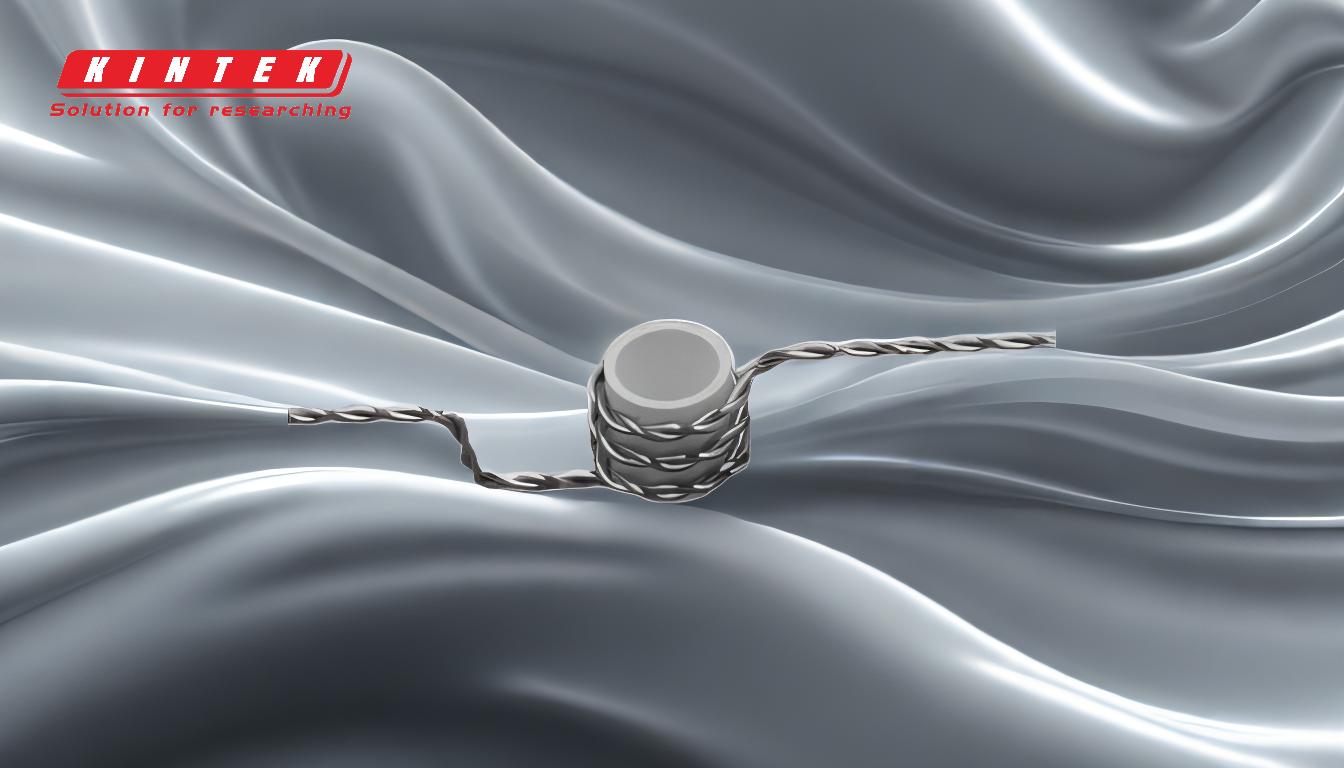
-
成膜メカニズム:
- CVD:高温(800~1000℃)でのガス状前駆体と基材との化学反応を伴う。その結果、複雑な形状を含むあらゆる表面上に均一なコーティングが形成される。
- PVD:スパッタリングや蒸着などの物理的プロセスを用いて、材料を基板上に直接、ライン・オブ・サイト方式で堆積させる。このため、露出している表面への被覆は制限されるが、膜の特性を正確に制御することができる。
-
使用温度:
- CVD:高温(800~1000℃)を必要とするため、基材の機械的特性に影響を与え、コーティングに引張応力や微細なクラックが発生する可能性がある。
- PVD:より低い温度(250~500℃)で動作するため、熱に敏感な材料に適しており、基材が変形するリスクを低減します。
-
膜厚と均一性:
- CVD:均一性に優れた厚膜(10~20μm)が得られ、高い耐摩耗性と耐久性が要求される用途に最適。
- PVD:優れた平滑性と精度でより薄いコーティング(3~5μm)を形成し、微細な表面仕上げと最小限の寸法変化を必要とする用途に適しています。
-
応力と密着性:
- CVD:加工温度が高いと、コーティングに引張応力が発生し、マイクロクラックが発生したり、密着性が低下する場合があります。
- PVD:冷却時に圧縮応力を発生させ、特に高精度用途でのコーティングの密着性と耐久性を向上させます。
-
材料適合性:
- CVD:主にセラミックやポリマーに使用され、優れた耐薬品性と熱安定性を持つ。
- PVD:金属、合金、セラミックスなど、より幅広い材料を蒸着できるため、さまざまな用途に対応できる。
-
用途:
- CVD:切削工具、航空宇宙部品、半導体製造など、厚い耐摩耗性コーティングを必要とする産業でよく使用される。
- PVD:医療機器、光学部品、装飾仕上げなど、薄く滑らかで精密なコーティングが必要な用途に適している。
-
コストと加工時間:
- CVD:一般に、高温と複雑な化学工程を伴うため、より高価で時間がかかる。
- PVD:処理時間が短く、コストが低いため、大量生産に適している。
まとめると、CVDとPVDコーティングインサートのどちらを選択するかは、コーティングの厚さ、使用温度、材料の適合性、希望する表面特性など、アプリケーションの具体的な要件によって決まります。CVDは高温環境下での厚く均一なコーティングに適しており、PVDは低温での滑らかで耐久性のある表面を必要とする精密な用途に適しています。
総括表
側面 | CVD | PVD |
---|---|---|
成膜メカニズム | 高温(800~1000℃)での化学反応、多方向性 | より低い温度(250~500℃)での物理的気化、ライン・オブ・サイト |
コーティング厚さ | 厚め(10~20μm)、均一 | より薄い(3~5μm)、超硬質で滑らか |
使用温度 | 高温 (800-1000 °C), 引張応力が発生する可能性がある。 | 低 (250-500 °C)、基材の変形を抑える。 |
応力と接着 | 引張応力、マイクロクラックの可能性 | 圧縮応力、接着力強化 |
材料適合性 | セラミック、ポリマー、高耐薬品性 | 金属、合金、セラミックス, 汎用性 |
用途 | 切削工具、航空宇宙、半導体 | 医療機器、光学、装飾仕上げ |
コストと加工 | 高価、時間がかかる | 費用対効果が高く、処理が速い |
CVDとPVDの選択でお困りですか? 当社の専門家に今すぐご連絡ください にご相談ください!