化学気相成長法(CVD)と物理気相成長法(PVD)は、さまざまな産業で広く使われている2つの異なる薄膜蒸着技術である。どちらの手法も基板上に薄膜を堆積させることを目的としているが、そのプロセス、操作条件、結果には大きな違いがある。CVDは、ガス状の前駆物質を含む化学反応に依存し、一般的に高温を必要とし、腐食性の副生成物を生成する可能性がある。対照的に、PVDは固体または液体材料の物理的気化を伴い、低温で作動し、腐食性の副生成物を避けることができる。CVDとPVDのどちらを選択するかは、希望するフィルム特性、基板材料、アプリケーション要件などの要因によって決まります。
キーポイントの説明
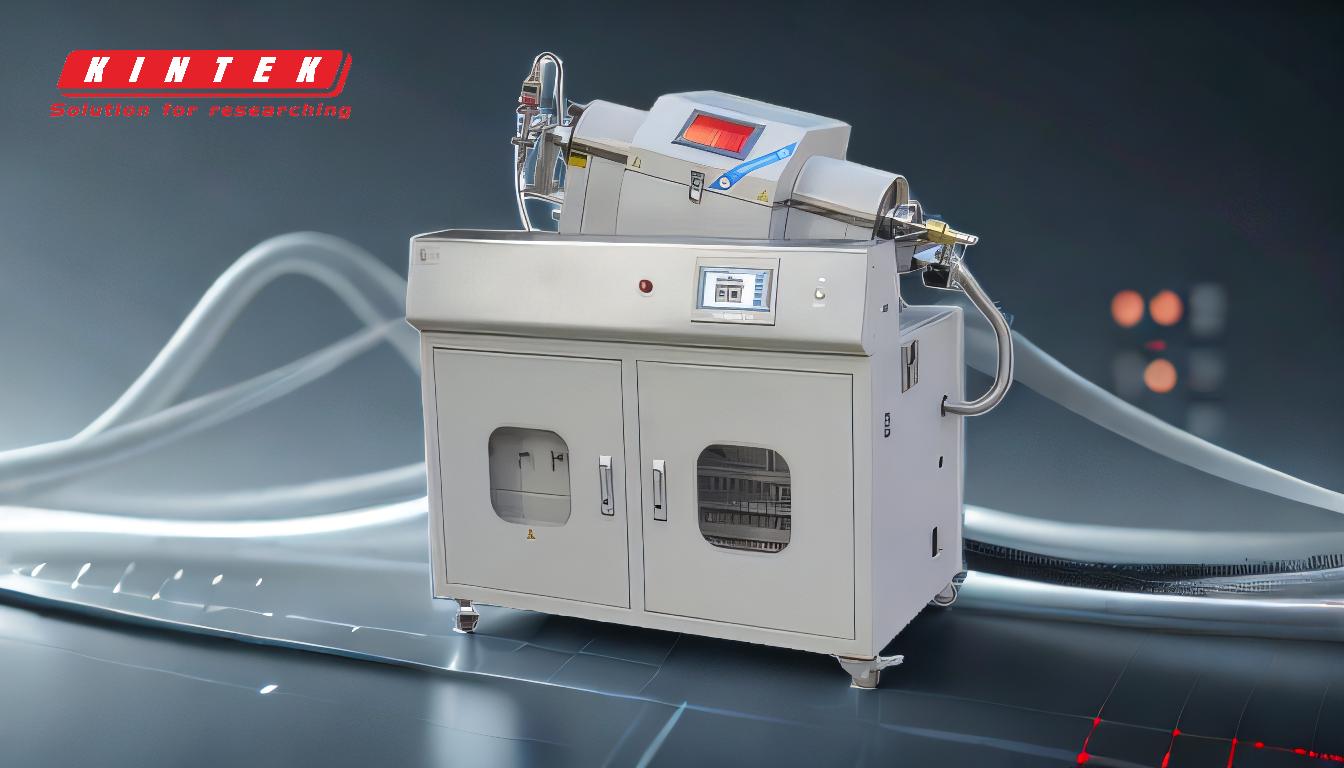
-
プロセスのメカニズム:
- CVD:加熱された基板表面でのガス状前駆体の化学反応を伴う。気体分子は基材に吸着し、反応し、固体膜を形成する。このプロセスは多方向性であるため、複雑な形状を均一にコーティングすることができる。
- PVD:固体または液体の材料を物理的に気化させ、蒸気として基板に運び、そこで凝縮させて薄膜を形成する。PVDはライン・オブ・サイトプロセスであり、平坦な形状や単純な形状に適している。
-
温度条件:
- CVD:通常、500℃から1100℃の高温で作動する。この高温環境は化学反応を促進するが、使用できる基板の種類が制限されることがある。
- PVD:CVDに比べて低温で動作するため、温度に敏感な基板に適している。しかし、電子ビームPVD(EBPVD)のように、比較的低温で高い成膜速度を達成できるPVD技術もある。
-
副生成物と不純物:
- CVD:腐食性のガス状副生成物が発生することが多く、プロセスが複雑になり、追加の安全対策が必要になることがある。また、高温のため、蒸着膜に不純物が混入することもある。
- PVD:腐食性の副生成物が発生せず、クリーンなプロセス。ただし、成膜速度はCVDに比べて一般的に低い。
-
蒸着率:
- CVD:一般に成膜速度が速く、厚膜や高スループットを必要とする用途に適している。
- PVD:EBPVDのような高度な技術では0.1~100μm/分の蒸着速度を達成できるが、一般的に蒸着速度は低い。
-
材料利用効率:
- CVD:ガス状の前駆体が複雑な形状を均一にコーティングできるため、材料の利用効率が高い。
- PVD:また、特にEBPVDのような技術では、非常に高い材料利用効率が得られる。
-
用途:
- CVD:高品質で均一な膜が要求される半導体製造によく使用される。また、工具、光学部品、耐摩耗性表面のコーティングにも使用される。
- PVD:装飾用コーティング、防錆層、耐摩耗フィルムなどに広く使用されている。ソーラーパネルや医療機器の製造にも使用されている。
-
設備と操作の複雑さ:
- CVD:高温と腐食性ガスを扱うための特殊な装置を必要とする。また、熟練したオペレーターと反応条件の正確なコントロールも要求される。
- PVD:真空条件と、場合によっては放熱を管理するための冷却システムが必要。装置は一般にCVD装置より複雑ではないが、熟練した操作が必要である。
まとめると、CVDとPVDのどちらを選択するかは、希望する膜特性、基板材料、操作上の制約など、アプリケーションの具体的な要件によって決まる。CVDは高温、高蒸着速度のアプリケーションに適しており、PVDは複雑な形状の低温、クリーンなプロセスに適している。
総括表
側面 | CVD | PVD |
---|---|---|
プロセスのメカニズム | 加熱された基板表面でのガス状前駆体の化学反応 | 固体/液体材料の物理的気化、基板上での凝縮 |
温度 | 高温 (500°C-1100°C) | より低く、温度に敏感な基板に適している |
副産物 | 腐食性ガス副生成物 | 腐食性副生成物なし |
蒸着率 | 高い | より低い(EBPVDのような高度な技術では0.1~100μm/min) |
材料効率 | 複雑な形状への高い均一コーティング | 特にEBPVDでは高い |
用途 | 半導体、工具、光学部品、耐摩耗表面 | 装飾コーティング、防錆層、ソーラーパネル、医療機器 |
装置の複雑さ | 高い、腐食性ガスと高温の取り扱いが必要 | 低い、真空条件と冷却システムが必要 |
CVDとPVDの選択でお困りですか? 当社の専門家に今すぐご連絡ください にご相談ください!