熱蒸発法は、特に簡便性、効率性、特定用途への適合性の面で、スパッタリング法に比べていくつかの利点がある。熱蒸発法では、真空中で材料が蒸発するまで加熱し、気化した原子を基板上に堆積させて薄膜を形成する。この方法は、温度差が小さく、製品の接触時間が短いことで知られており、熱に敏感な製品に最適です。また、金属電荷のアウトガスと再装填にも効率的で、揮発性の低い不純物が膜を汚染する前に蒸発が自動的に終了する。対照的に、スパッタリングはターゲット材料にイオンをぶつけて原子を放出させ、基板上に堆積させる。スパッタリングは再現性が高く、環境にも優しいが、合金を作る能力、単純さ、操作の複雑さの低さから、熱蒸発法が好まれることが多い。
要点の説明
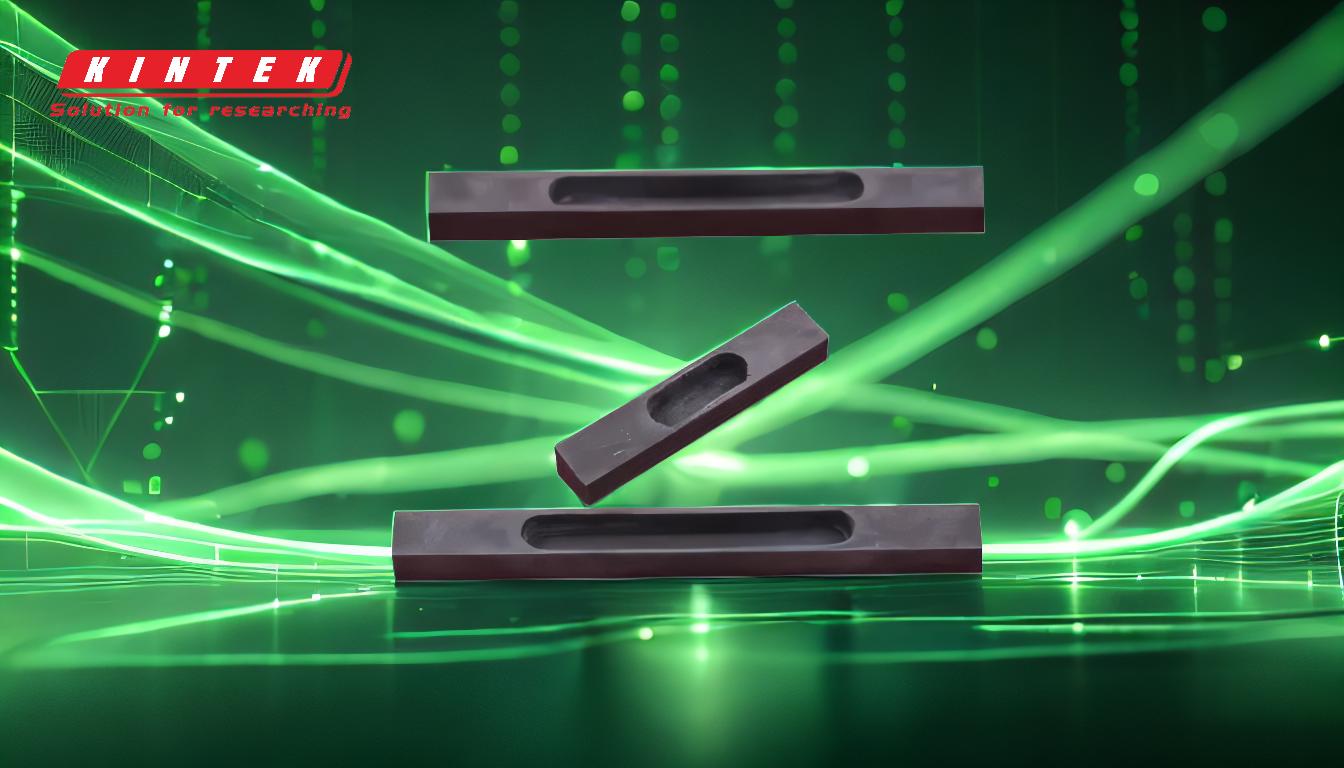
-
シンプルさと操作性:
- 真空中で材料を加熱し、蒸発させて基板上に堆積させる。このプロセスは、イオンボンバードメントとプラズマ発生を正確に制御する必要があるスパッタリングに比べて複雑ではない。
- 熱蒸発では抵抗ボートやコイルを使用するため、セットアップが簡素化され、操作やメンテナンスが容易になる。
-
効率とアウトガス:
- 熱蒸着は非常に効率的で、材料を効果的にアウトガス化する能力があり、クリーンな蒸着プロセスを保証する。これは、高純度膜を必要とする用途では特に重要です。
- この方法では、揮発性の低い不純物が蒸発する前に蒸発が自動的に終了するため、蒸着膜の純度が保証される。
-
熱に弱い製品への適性:
- 温度差が小さく、製品との接触時間が短いため、熱蒸着は熱に敏感な製品に最適です。これにより、基材や蒸着材料への熱損傷のリスクを最小限に抑えることができます。
-
合金と連続コーティングの作成:
- 熱蒸着は、複数のソースを使用することで合金を作成することができ、複雑な材料組成の成膜が可能です。
- コーターの構成により、蒸着またはスパッタリングによる連続成膜が可能であり、成膜の柔軟性を提供します。
-
産業用途:
- 熱蒸着は、太陽電池、薄膜トランジスタ、半導体ウェハー、カーボンベースのOLEDにおける金属接合層の形成など、さまざまな産業用途で広く使用されている。その汎用性の高さから、多くの薄膜蒸着プロセスで好まれている。
-
スパッタリングとの比較:
- スパッタリングは再現性が高く、少量の酸化物、金属、合金を正確に成膜できる反面、複雑で、より高度な装置を必要とする。
- 一方、熱蒸発法はシンプルでコスト効率が高く、高純度かつ熱影響を最小限に抑える必要がある用途に適している。
まとめると、熱蒸発法はスパッタリングに比べて、特に簡便性、効率、熱に敏感な用途への適合性という点で大きな利点がある。合金の作成や連続的なコーティングが可能なため、薄膜蒸着プロセスにおける汎用性がさらに高まる。熱蒸発法の詳細については、以下をご覧ください。 熱蒸発 .
総括表:
側面 | 熱蒸発 | スパッタリング |
---|---|---|
シンプルさ | 複雑なセットアップを最小限に抑えたシンプルなプロセス。 | イオンボンバードメントとプラズマ発生を正確に制御する必要がある。 |
効率性 | 効率的なアウトガスと自動ターミネーションにより、高純度フィルムを確保。 | 再現性は高いが、アウトガスの効率は低い。 |
熱感受性 | 温度差が小さいため、熱に敏感な製品に最適。 | 敏感な基板に熱損傷を与える可能性がある。 |
合金の作成 | 複数のソースを使用した合金の作成が可能。 | 合金作成の柔軟性に制限あり。 |
産業用途 | 太陽電池、薄膜トランジスタ、半導体ウェハー、OLEDなどに幅広く使用。 | 酸化物、金属、合金の精密蒸着に適している。 |
コストと複雑さ | 費用対効果が高く、操作が簡単。 | 複雑で高度な装置が必要。 |
熱蒸発法の活用にご興味がおありですか? 当社の専門家に今すぐご連絡ください までご連絡ください!