スパッタリングは、基板上に薄膜を堆積させるために使用される物理蒸着(PVD)技術である。ターゲット材料に高エネルギーのイオン(通常はアルゴンなどの希ガス)を衝突させ、ターゲットから原子を離脱させる。これらの原子は真空中を移動し、基板上に堆積して薄膜を形成する。スパッタリングは、優れた密着性と膜特性の精密な制御により、高品質で均一な膜を作ることができるため、半導体、光学、コーティングなどの産業で広く利用されている。このプロセスは金属、合金、化合物など幅広い材料に対応し、比較的低温で実施できるため、プラスチックや有機物のような敏感な基板にも適している。
キーポイントの説明
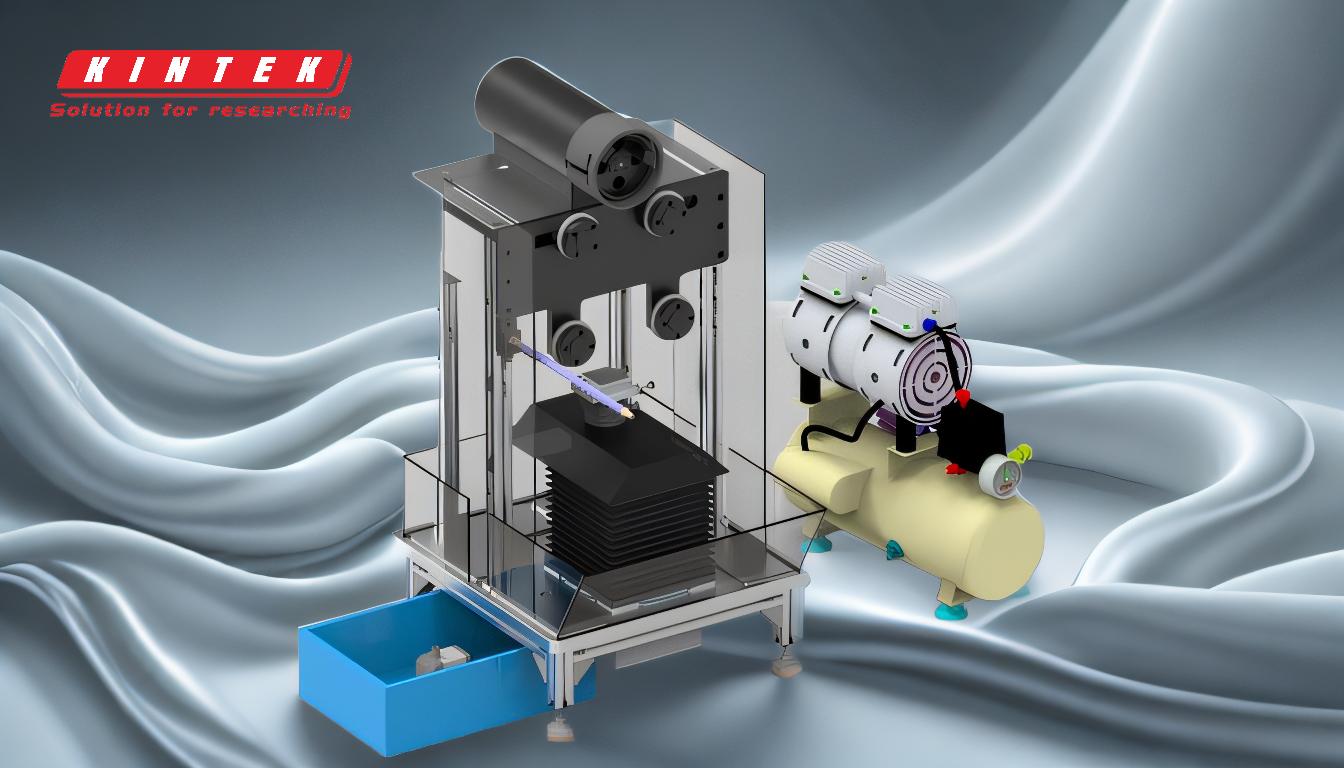
-
スパッタリングのメカニズム:
- スパッタリングでは、希ガスプラズマ(通常はアルゴン)を使用してターゲット材料に衝突させる。
- プラズマからの高エネルギーイオンがターゲットに衝突し、コリジョンカスケードと呼ばれるプロセスを経て原子が外れる。
- 放出された原子は真空中を移動し、基板上に堆積して薄膜を形成する。
-
スパッタリングの利点:
- 汎用性:スパッタリングは、金属、合金、化合物、さらには蒸発しにくい非常に融点の高い材料など、さまざまな材料を成膜することができる。
- 精度とコントロール:このプロセスでは、分子レベルの精度が得られるため、原始的な界面を形成することができ、プロセスパラメーターを制御することで膜の特性を調整することができる。
- 低温動作:スパッタリングは低温で行うことができるため、プラスチック、有機物、ガラスなどの繊細な材料のコーティングに適している。
- より良い接着性:スパッタで放出された原子は、蒸着された材料に比べて運動エネルギーが高く、その結果、基板への密着性が向上する。
- 均一性と密度:スパッタ膜は一般的に均一で、低温でも充填密度が高い。
- 再現性と自動化:スパッタ蒸着は、熱蒸着や電子ビーム蒸着などの他の方法と比べて再現性が高く、自動化が容易である。
-
スパッタ蒸着の応用:
- 光学フィルム:スパッタリングは、スパッタされた金属イオンを酸化または窒化して、所望の組成の酸化物層または窒化物層を形成することにより、光学薄膜を成膜するために使用される。
- 半導体:この技術は、金属、誘電体、その他の材料の薄膜を蒸着するために、半導体産業で広く使用されている。
- コーティング:スパッタリングは、ガラス、金属、プラスチックなど、さまざまな基材に保護膜や機能膜を形成するために用いられる。
- 高度なプロセス:スパッタリングは、エピタキシャル成長などの高度なプロセスをサポートします。
-
プロセスパラメータと制御:
- ガス組成:ガス(アルゴンなど)の選択や反応性ガス(酸素や窒素など)の導入は、蒸着膜の特性に影響を与える。
- 圧力とパワー:スパッタリングチャンバー内の圧力とターゲットへの印加電力を調整することで、成膜速度と品質を制御することができる。
- 基板の位置決め:ターゲットと基板の距離や基板の向きは、フィルムの均一性や密着性に影響を与える。
-
他の蒸着法との比較:
- 熱蒸発:熱蒸発法とは異なり、ターゲット材料を気化させるために高温を必要としないため、より幅広い材料や基板に適している。
- Eビーム蒸着:スパッタリングは、より複雑で一貫性のないE-ビーム蒸着に比べ、再現性に優れ、自動化が容易である。
- 化学気相成長法(CVD):スパッタリングは物理的プロセスであり、CVDは化学的プロセスである。スパッタリングは、化学的前駆体を必要とせずに純粋な膜を成膜できるため、しばしば好まれている。
-
メンテナンスと運用に関する考慮事項:
- メンテナンス・フリー:スパッタリングシステムは一般にメンテナンスフリーで、長寿命のターゲットが安定した気化源を提供する。
- 超高真空対応:このプロセスは、特定の高純度用途に不可欠な超高真空条件に適合する。
- 反応性析出:スパッタリングは、成膜プロセス中に酸化物や窒化物のような化合物膜を直接形成する反応性ガスを容易に取り込むことができる。
要約すると、スパッタリングは薄膜を成膜するための非常に汎用性が高く精密な方法であり、他の成膜技術と比べて多くの利点がある。幅広い材料に対応し、均一で密着性の高い薄膜を作製でき、低温で操作できることから、多くの産業および研究用途で好んで使用されている。
総括表:
アスペクト | 主な内容 |
---|---|
メカニズム | ターゲット材料に高エネルギーイオン(アルゴンなど)を衝突させ、薄膜を成膜する。 |
メリット | 多用途、精密、低温操作、優れた接着性、均一なフィルム。 |
アプリケーション | 半導体、光学フィルム、コーティング、エピタキシーなどの先端プロセス。 |
プロセス制御 | ガス組成、圧力、パワー、基板の位置決めを精密に調整。 |
比較 | 再現性と純度において、熱蒸着、E-Beam、CVDより優れている。 |
メンテナンス | メンテナンスフリー、超高真空対応、反応性蒸着に対応。 |
次のプロジェクトでスパッタリングを検討する準備はできていますか? お問い合わせ をご覧ください!