熱処理後の冷却方法は、硬度、強度、延性な ど、所望の材料特性を得るために極めて重要で ある。冷却方法の選択は、材料、熱処理プロセス、およ び希望する結果によって異なる。一般的な方法には、炉内での徐冷、各種媒体 (水、油、ガス、ポリマー) での急冷、真空炉でのアルゴンなどの不活性ガスによる冷却があります。それぞれの方法には特定の用途と利点があり、急冷は最も広く使用されています。これらの方法を理解することで、特定の材料や性能要件に適した冷却技術を選択することができます。
キーポイントの説明
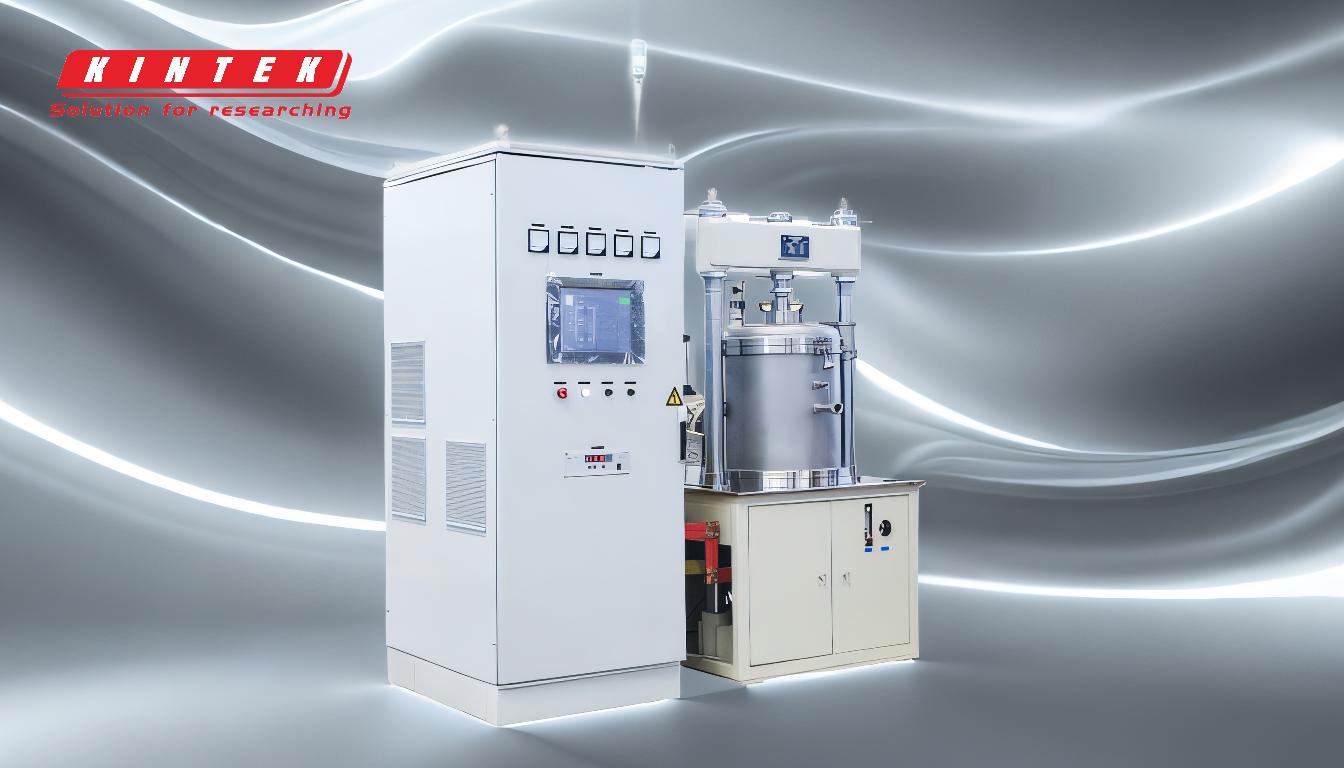
-
炉内徐冷
- プロセス:熱処理後、一部の材料は炉内でゆっくりと冷却される。この方法では、材料が制御された速度で冷却されるため、熱応力が発生せず、均一な冷却が保証されます。
- 応用例:通常、アニーリングのような、材料を軟化させ、内部応力を緩和し、延性を向上させることを目的とする工程に使用される。
- 利点:ひび割れや反りのリスクを低減し、急激な温度変化に敏感な素材に適している。
-
焼入れ
- プロセス:急冷とは、材料を急冷媒体に浸して急速に冷却することである。一般的な媒体には、水、塩水、油、ポリマー溶液、溶融塩、溶融金属、ガスなどがあります。
- 用途:高い硬度と強度を得るために、焼き入れや焼き戻しなどの工程で広く使用される。部品の約90%は、水、油、ガス、またはポリマー中で焼入れされます。
- 利点:急冷は、所望の微細構造と機械的特性を達成するのに役立つ。しかし、内部応力が発生し、その後の焼戻しが必要になる場合があります。
-
不活性ガスによる冷却
- プロセス:真空炉熱処理では、アルゴンなどの不活性ガスを加熱室内に循環させて部品を冷却します。不活性ガスは材料と化学反応しないので理想的です。
- 用途:高精度部品や酸化に敏感な部品など、制御された冷却環境を必要とする材料に適しています。
- 利点:クリーンで非反応性の冷却環境を提供し、コンタミネーションのリスクを低減し、均一な冷却を保証します。
-
特定の冷却媒体
- 水と塩水:非常に急速な冷却が可能で、鋼の高硬度化に最適。ただし、冷却速度が速いため、ひずみや割れが発生することがある。
- オイル:水よりも冷却速度が遅く、割れのリスクを低減。合金鋼や工具鋼によく使用される。
- ポリマーソリューション:水と油の中間の冷却速度を提供し、硬度と歪みのリスク低減のバランスを提供する。
- 溶融塩と金属:冷却速度の精密な制御が必要な特殊用途に使用。
- ガス種:窒素やアルゴンなど、高精度部品のガス焼入れに使用され、クリーンで均一な冷却環境を提供します。
-
冷却方法の選択
- 材料の検討:冷却方法の選択は、材料の特性や要求される結 果によって異なります。例えば、鋼材の場合、硬度を高めるために焼入れを必要とすることが多く、アルミニウム合金の場合、徐冷が有効な場合があります。
- プロセス要件:熱処理工程(例:焼きなまし、焼き入れ、焼き戻し)によって冷却方法が決まる。焼入れには急冷が不可欠であり、焼きなましには徐冷が好ましい。
- 部品形状:複雑な形状の場合、歪みや割れを防ぐために制御された冷却が必要になることがあり、ガス冷却やポリマー溶液のような方法が適しています。
-
冷却後の処理
- 焼戻し:内部応力を緩和し、靭性を向上させるために焼入れの後に行われることが多い。材料は低温まで再加熱された後、ゆっくりと冷却される。
- 応力緩和:材料の残留応力を低減するための熱処理で、新たな応力が発生しないように徐冷することが多い。
これらの冷却方法とその用途を理解することは、所望の材料特性と性能特性を達成するために適切な技術を選択する上で極めて重要です。
総括表
冷却方法 | プロセス | アプリケーション | 利点 |
---|---|---|---|
炉内での徐冷 | 熱応力を防ぐために炉内で制御された冷却。 | 材料を軟化させ、延性を向上させるアニール。 | 割れや反りを抑え、デリケートな素材に最適。 |
急冷 | 水、油、ポリマー、ガスなどを用いた急冷。 | 高い硬度と強度を得るための焼入れと焼戻し。 | 所望の微細構造が得られるが、応力を緩和するために焼戻しが必要になる場合がある。 |
不活性ガスによる冷却 | アルゴンや窒素を使用した真空炉での冷却 | 高精密部品や酸化に敏感な材料。 | コンタミのないクリーンで均一な冷却を保証します。 |
冷却媒体 | 水、塩水、オイル、ポリマー、溶融塩、ガス。 | 特定の素材と冷却ニーズに対応。 | 硬度と歪みリスクの低減のバランスをとります。 |
冷却後処理 | 焼戻しおよび応力除去による靭性の向上と残留応力の低減。 | 材料の性能を高めるために焼入れ後に不可欠。 | 靭性を向上させ、内部応力を低減します。 |
熱処理工程に最適な冷却方法の選択にお困りですか? 当社の専門家にご連絡ください。 にお問い合わせください!