電着は電気メッキとも呼ばれ、電流を利用して表面に材料の薄層を析出させるプロセスである。2つの電極(陽極と陰極)を、析出させる材料のイオンを含む電解質溶液に浸す。電流を流すと、電解液中の金属イオンが陰極で還元され、表面に固体層が形成される。陽極は、析出されるのと同じ材料でできていることが多く、溶解して溶液中のイオンを補充する。電流、電圧、電解液組成などのパラメーターを注意深く制御することで、電着はナノスケールでも精密で均一なコーティングを作り出すことができる。この技術は、エレクトロニクス、自動車、宝飾品などの産業で、保護、装飾、機能性コーティングの作成に広く利用されている。
キーポイントの説明
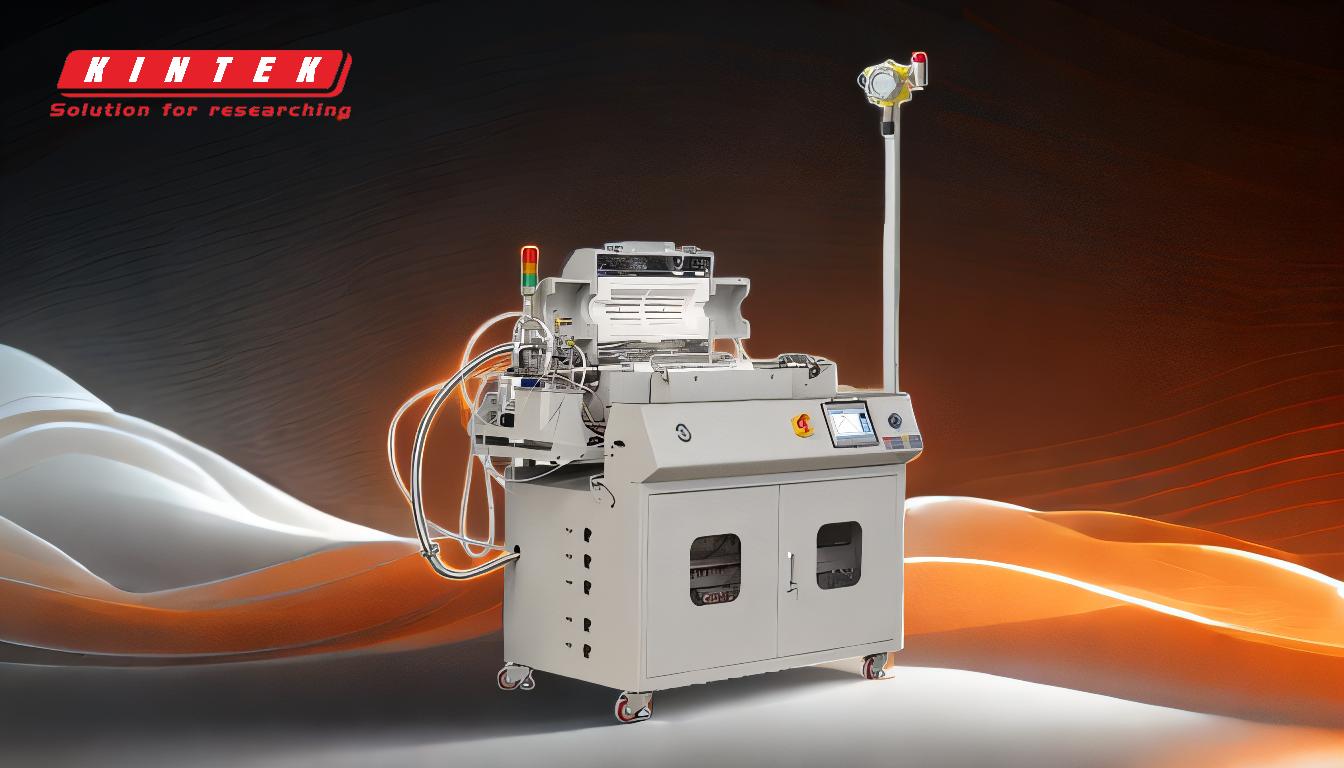
-
電着の基本原理:
- 電着は、電流が化学反応を引き起こす電気分解の原理を利用している。
- このプロセスには、電解質溶液に浸された陽極(プラスに帯電)と陰極(マイナスに帯電)の2つの電極が必要である。
- 電解液には析出させる材料(銅、ニッケル、金など)のイオンが含まれている。
-
電極の役割:
- 陽極:通常、析出する材料と同じ材料でできている(例えば、銅めっき用の銅陽極)。電解液に溶けて金属イオンを放出し、溶液の濃度を維持する。
- 陰極:コーティングされる対象物(金属部品など)。電解液中の金属イオンが陰極表面で還元され、固体層が形成される。
-
電気化学反応:
- 陽極では酸化が起こり、金属イオンが電解液中に放出される(例えば、Cu → Cu²⁺ + 2e-)。
- 陰極では還元が起こり、金属イオンが電子を獲得して固体の沈殿物を形成する(例:Cu²⁺ + 2e- → Cu)。
-
電解質組成の重要性:
- 電解液は、滑らかで均一な析出を確実にするために、適切な濃度の金属イオンやその他の添加剤を含んでいなければならない。
- 添加剤は、光沢、密着性、耐食性などのコーティング特性を向上させることができる。
-
制御パラメータ:
- 電流密度:成膜速度を決定する。電流が高すぎると、コーティングが粗くなったり、不均一になったりする。
- 電圧:電気化学反応の駆動力に影響する。
- 温度:反応の速度論と析出物の品質に影響する。
- pH:副反応や不要な化合物の析出を防ぐため、注意深く制御する必要がある。
-
電着の応用:
- 保護コート:腐食や磨耗を防ぐために使用される(自動車部品のクロムメッキなど)。
- 装飾仕上げ:美的魅力を提供する(例:宝飾品の金メッキ)。
- 機能性コーティング:導電性、はんだ付け性、その他の特性を向上させる(例:回路基板の銅めっき)。
- ナノ構造フィルム:エレクトロニクスや材料科学における高度な用途のための、超薄膜で精密なコーティングの作成を可能にします。
-
電着の利点:
- 精密:原子1個分の薄い層を蒸着できる。
- 汎用性:様々な材料や基板に適しています。
- スケーラビリティ:小規模から産業用まで適応可能。
-
課題と考察:
- 均一性:複雑な形状で一貫した厚みを得るのは難しい。
- 接着:デポジットは、剥離や剥落を避けるため、基材によく接着しなければならない。
- 環境への影響:電解液と副産物の適切な処理は、汚染を最小限に抑えるために不可欠である。
これらの重要なポイントを理解することで、電着の背後にある科学と工学、そして現代の製造と技術におけるその大きな可能性を理解することができる。
要約表
主な側面 | 詳細 |
---|---|
基本原理 | 電気分解を利用し、電流によって材料を析出させる。 |
電極 | 陽極(溶解してイオンを放出)、陰極(コーティングを受ける)。 |
電気化学反応 | 陽極で酸化、陰極で還元。 |
電解液組成 | 滑らかで均一な析出のための金属イオンと添加剤を含む。 |
制御パラメーター | 電流密度、電圧、温度、pH。 |
用途 | 保護コーティング、装飾仕上げ、機能性コーティング、ナノ構造フィルム |
利点 | 精度、汎用性、拡張性 |
課題 | 均一性、接着性、環境への影響。 |
電着がお客様の製造工程をどのように強化できるかをご覧ください。 今すぐご連絡ください !