プラズマ化学蒸着 (PECVD) は、従来の CVD プロセスと比較して、比較的低い温度 (通常は 200 ~ 400 ℃) で薄膜の蒸着を可能にする多用途の技術です。これは、電気エネルギーを使用してプラズマを生成することによって実現され、熱エネルギーのみに依存することなく、ガス混合物を活性化し、化学反応を促進します。 PECVD の低温機能は、ポリマーや特定の半導体などの温度に敏感な基板上に熱損傷を引き起こすことなく膜を堆積するために非常に重要です。さらに、PECVD には高い堆積速度、その場ドーピング、コスト効率などの利点があり、多くの産業用途で好まれる選択肢となっています。低温で高い堆積速度を達成するための重要な要素には、ガス流量、圧力、プラズマ密度などのプロセスパラメータの最適化や、高周波やマイクロ波放電などの高度な技術を活用して高密度プラズマを生成することが含まれます。
重要なポイントの説明:
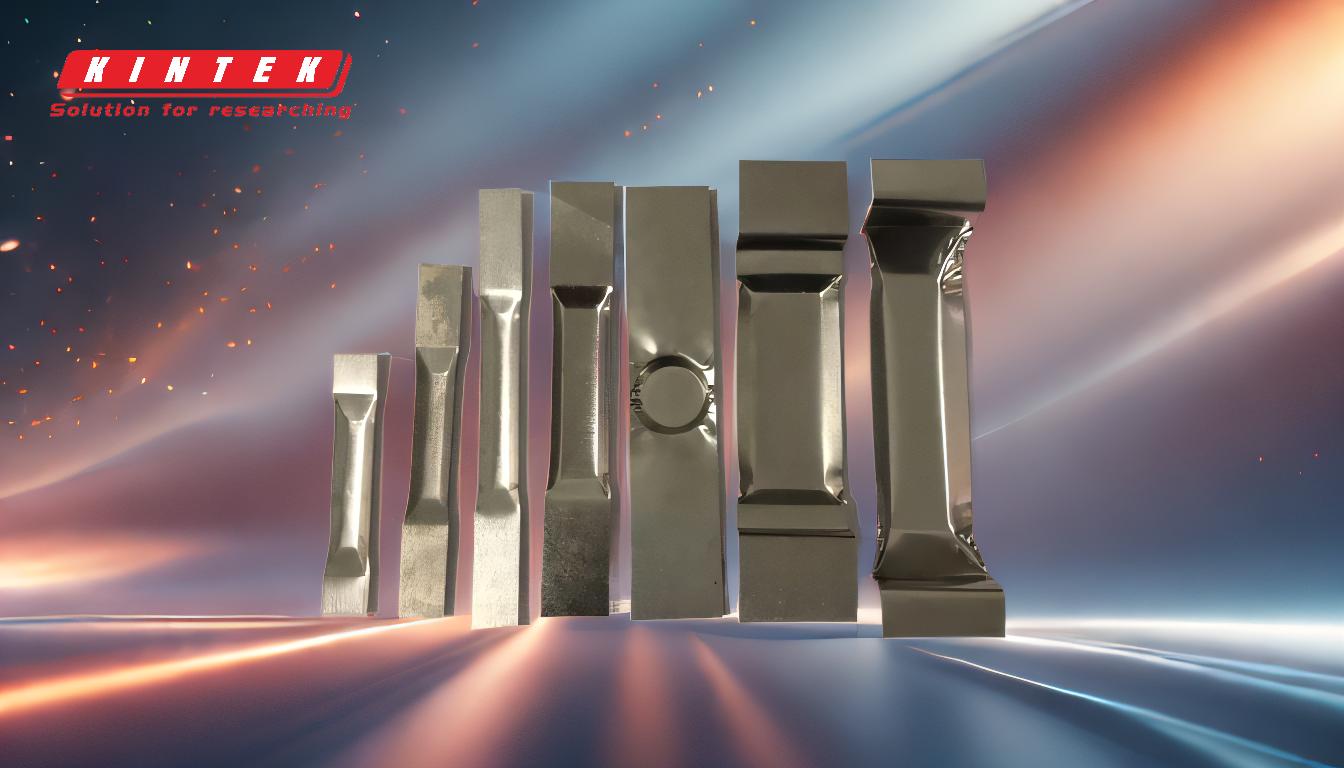
-
PECVDにおける低温成膜のメカニズム:
- PECVD では、電気エネルギーを使用してグロー放電 (プラズマ) を生成し、エネルギーを混合ガスに伝達し、ラジカル、イオン、励起分子などの反応種を生成します。
- 熱活性化に依存する従来の CVD とは異なり、PECVD は電子衝撃解離を利用して気相反応を推進し、はるかに低い温度 (200 ~ 400 °C) での堆積を可能にします。これは、温度に敏感な基材にとって特に有益です。
- PECVD プロセスの詳細については、次のサイトを参照してください。 PECVD 。
-
堆積速度の向上におけるプラズマの役割:
- 高周波 (RF) やマイクロ波放電などの技術によって生成された高密度プラズマは、反応種の濃度を大幅に増加させ、堆積速度の高速化につながります。
- プラズマのエネルギーは前駆体ガス内の化学結合を破壊するのに十分であり、より低い基板温度でも薄膜の形成を促進します。
-
プロセスパラメータの最適化:
- ガスの流れ: ガス流量を正確に制御することで、反応種を基板表面に安定して供給し、蒸着の均一性と速度を向上させます。
- プレッシャー: リアクター チャンバー内の最適な圧力レベルを維持することは、ガス分子の平均自由行程とプラズマ密度に影響を与え、どちらも堆積速度に影響します。
- 温度: PECVD は低温で動作しますが、200 ~ 400°C の範囲内でわずかに調整することで膜の特性と堆積速度を微調整できます。
- サンプルの配置: リアクター内で基板を適切に配置することで、プラズマと反応種への均一な曝露が保証され、堆積効率が向上します。
-
低温PECVDの利点:
- 基板の互換性: 低温で膜を堆積できるため、ポリマーやその他の熱に弱い材料など、使用可能な基板の範囲が広がります。
- 高い生産性: PECVD は成膜速度が速いため、生産効率が向上し、大規模製造に適しています。
- その場ドーピング: ドーピングは蒸着中に直接実行できるため、プロセスが簡素化され、製造ステップが削減されます。
- 費用対効果: LPCVD のような高温プロセスと比較して、PECVD は高品質の成膜を維持しながら、材料コストと運用コストを削減します。
-
フィルム特性に対する基板温度の影響:
- PECVD での堆積速度は基板温度に大きく依存しませんが、組成、応力、形態などの膜特性は温度変化に大きく影響されます。
- 基板温度を下げると熱応力が軽減され、デリケートな基板へのフィルムの接着力が向上します。
-
高い成膜速度を達成するための技術:
- 高密度プラズマ源: RF やマイクロ波放電などの技術は高密度プラズマを生成し、反応種の濃度を高め、堆積速度を高めます。
- 多原子ガスの放出: プラズマ放電で多原子ガスを使用すると、高い堆積速度を維持しながら堆積温度をさらに下げることができます。
- プロセス制御: 高度な監視および制御システムにより、プラズマの生成と成膜の最適な条件が保証され、効率と品質が最大化されます。
これらの要因を理解して最適化することで、PECVD は低温で高い堆積速度を達成でき、幅広い用途に非常に効果的で汎用性の高い堆積技術となります。
概要表:
重要な要素 | 説明 |
---|---|
プラズマ活性化 | 電気エネルギーを利用してプラズマを生成し、低温成膜を可能にします。 |
高密度プラズマ | RF またはマイクロ波放電により反応種が増加し、堆積が高速化されます。 |
ガス流量と圧力 | 正確な制御により、蒸着の均一性と速度が向上します。 |
基板温度 | 温度を下げると (200 ~ 400 °C) 熱応力が軽減され、フィルムの密着性が向上します。 |
高度なテクニック | 多原子ガスの放出とプロセス制御により効率が最大化されます。 |
PECVD が薄膜堆積をどのように最適化できるかをご覧ください。 今すぐ専門家にお問い合わせください !